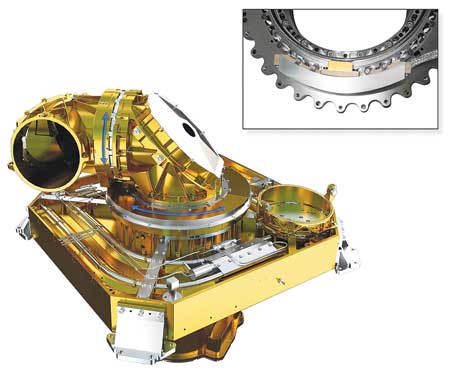
Tesat-Spacecom and Renishaw GEO space encoder (inset) with Tesat-Spacecom laser communication terminal that incorporates the encoder.
Renishaw, in collaboration with Tesat-Spacecom GmbH, has introduced a space-qualified angle encoder designed to provide high radiation hardness, high accuracy and qualification for 15 years of life in a GEO space environment.
"The system combines Renishaw's advanced optical encoder technology with Tesat-Spacecom's knowledge and experience in ruggedized space electronics," said a company spokesperson. "The GEO space encoder's readhead is designed to survive harsh environments, with 150 g vibration resistance and wide operating temperature range, combined with a robust optical detection principle. The readhead has a mass of only 300 g and power consumption is typically less than 1 W. Special attention on radiation hardness results in the encoder achieving qualification for 15 years of use in GEO space conditions.
"The scale consists of a stainless steel ring with graduations marked directly on the periphery, thus eliminating shock/vibration-induced breakages associated with traditional glass discs. The graduations include IN-TRAC reference marks that are directly embedded in the incremental channel, arranged in a distance-coded pattern so that the distance between any two adjacent reference marks is unique. This means that only a small rotation is required before absolute position is determined by the on-board field-programmable gate array (FPGA). The ring format enables easy integration into rotary axes, with a large through-hole to allow easy routing of utilities.
"The ring is mounted directly to the rotor, with the head mounted to the stator. There is no contact between the two parts, so no need for separate bearings or flexible couplings. This arrangement improves reliability and eliminates backlash, shaft wind-up (torsion) and other irregular metrology effects that plague traditional enclosed encoders.
High accuracy is achieved with short-range error less than 0.5 µrad RMS and long-range error less than 5 µrad (without mechanical errors). Combined with resolution of less than 0.5 µrad, the system is well suited to applications demanding precision metrology."
For more information contact:
Renishaw Inc.
5277 Trillium Blvd
Hoffman Estates, IL 60192
847-286-9953
usa@renishaw.com
www.renishaw.com/encoders
Tesat-Spacecom GmbH
www.tesat.de