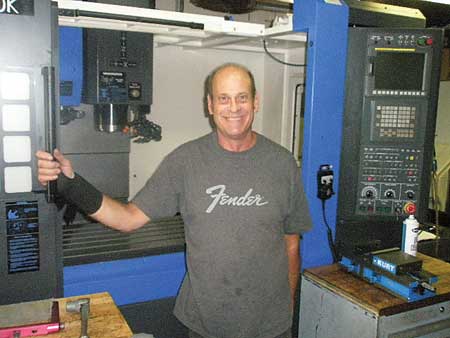
Jim Hickman, Owner, Machine Shop with the Hwacheon Vesta 1000 vertical machining center.
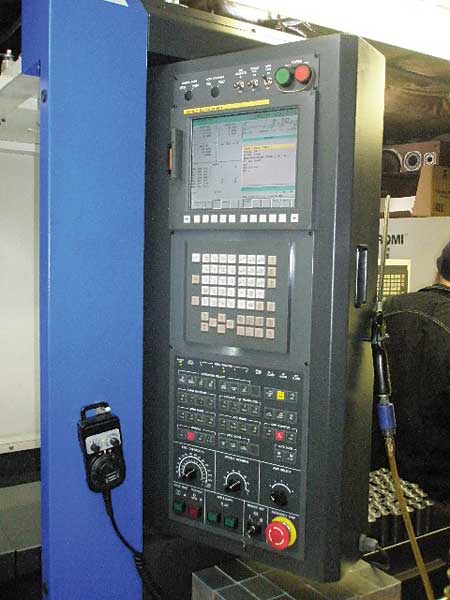
"The Optima optimization software is a very valuable tool that both inexperienced and experienced programmers find easy to use. Programmers simply use convenient G-code programming and a number of data sets for specific tools and process control," said Jim Hickman, Owner, Machine Shop.
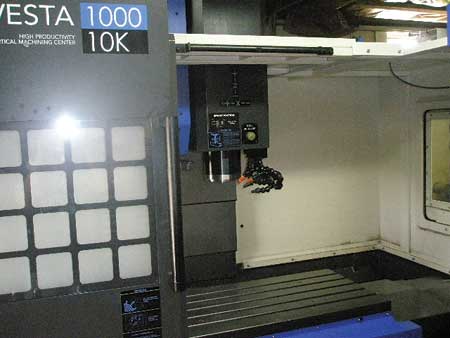
Hwacheon Vesta 1000 vertical machining center spindle and table.
The aptly named "Machine Shop" in Des Moines, IA, was primarily and originally known as a motorcycle performance shop. When the volume of work in performance parts began to slow, the owner, Mr. Jim Hickman, chose to broaden his customer base through the acquisition of new, more versatile manufacturing equipment. Specific criteria included the ability to efficiently handle a wide variety of prototype and short run production work, using materials from aluminum to cold rolled steel.
Mr. Hickman knew that a high level of rigidity and the ability to take a heavy cut without bogging down were machine qualities that would significantly benefit his customers' production work. After researching the available equipment options, he decided that a Hwacheon Vesta 1000 vertical machining center (VMC) met his needed specifications. The Vesta 1000 also employs the Optima cutting feed optimization software, further enhancing its value for the shop.
"The weight and rigidity of the machine frame, together with the Optima cutting feed optimization software, help achieve impressive tolerances" said Mr. Hickman. "The Optima optimization software is a very valuable tool that both inexperienced and experienced programmers find easy to use. Programmers simply use convenient G-code programming and a number of data sets for specific tools and process control."
According to Hwacheon, the Hwacheon Optima cutting feed optimization software utilizes an adaptive control method to regulate the feedrate in real time to sustain a consistent cutting load while machining. As a result, cutting tools are less prone to damage and machining time is reduced. All this shows up on a graphic display of tool load and feedrate.
The shop now works with a wide range of parts and materials and Mr. Hickman says the software has been vital. The machine adjusts to the material automatically every time, from cold rolled steel to aluminum in all shapes, sizes and part specifications. The Optima software manages speeds and feeds on corners in order to maintain a consistent spindle load. Generally, CNC mills operate with a set speed and feed. Adjusting this to manage cutting loads throughout a process - without spending machine time on trial cuts - is difficult. "With the Optima cutting feed optimization system, you just turn it on. With a consistent load on the spindle we save on tool cost and unscheduled tool changes and end up with a smoother finish," said Mr. Hickman.
The Vesta 1000 VMC, with a total machine weight of more than 14,000 lbs., is designed for heavy-duty machining. Its direct drive 10,000 RPM spindle provides stable high-speed cutting and high torque values. The spindle and gear box are oil-cooled to minimize thermal displacement and promote spindle life. The machine has an 1,100 x 500 work surface area, XYZ axis travels of 1,000 mm (39.37"), 550 mm (21.65") and 500 mm (19.69") and table load capacity of 700 kg (1,543 lbs.). Users have a choice of 24- or 30-tool storage magazines.
According to Hwacheon, the Vesta also has machining software components that monitor different variables related to work environment and machining conditions to adjust for best results and machining efficiency. Spindle displacement control is also possible with standard Hwacheon software. Software may also be used to constantly monitor temperature at a number of points within the spindle assembly, predicting thermal displacement and making necessary adjustments accordingly.
The Machine Shop now produces about 30 different parts a month with lot sizes running from a few pieces to 250 or more. Work is produced for industries ranging from recreation to automotive and die repair. Jim Hickman says that with the Hwacheon Vesta 1000 VMC, he knows his shop can produce work on time and to the quality demanded, from tough steels to freer cutting material.
For more information contact:
Hwacheon Machinery America
555 Bond St.
Lincolnshire, IL 60069
847-573-0100
www.hwacheon.com
Machine Shop
6821 Fleur Drive
Des Moines, IA 50321
515-285-4332
hickrace@msn.com
www.themachineshopinc.com