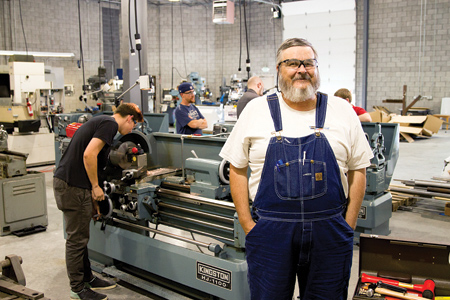
Instructor Barry Maxfield developed MATC's Machine Tool Technology program, which uses Kingston HJ 1100 engine lathes for manual machine training.
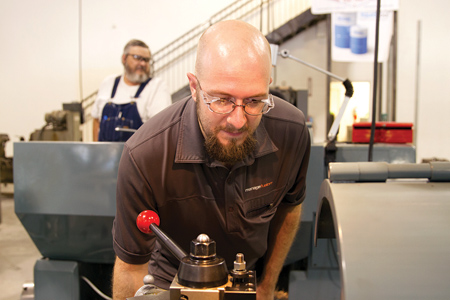
Student David Mayson said that he can transition easily between projects with the Kingston HJ-1100.
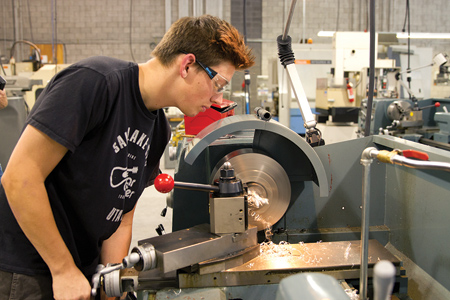
"When you have a set of blueprints and you are able to follow them and get a project done exactly right, it feels really good," said student Tyler Thompson.
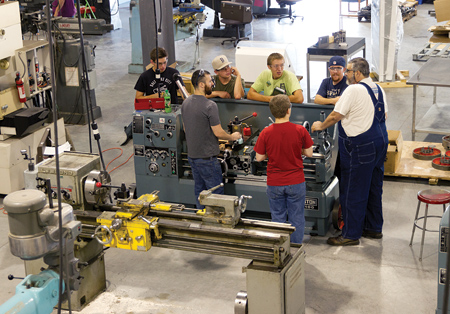
Barry Maxfield (far right) instructs some of his students on a Kingston HJ 1100 engine lathe.
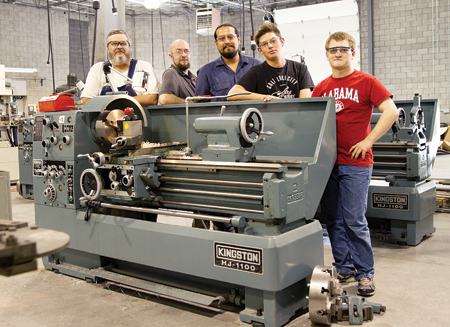
(l-r) Instructor Barry Maxfield, David Mayson, Chad Atene, Tyler Thompson and Ethan Christensen with a Kingston HJ 1100 engine lathe.
Mountainland Technical College's (MATC) Machine Tool Technology program mission is to put people to work - and with the program's current 100% job placement rate it is achieving just that. The two-year-old program, based in Utah, has grown from a handful of students in its first year to more than 50, and is expected to further expand in the near future.
Instructor Barry Maxfield, who developed the Machine Tool Technology program, noted that while the machining industry is strong nationwide, it is especially strong in Utah. Manufacturers are looking for employees, and young people are eager to work with machine tool technology and with their hands. "Most of my students are here to earn a diploma so they can go to work," he said.
"Right now in the U.S. we have a problem hiring and training machinists," continued Maxfield. "The traditional method used to be an 8,000 hour partnership with two years of school. There are few states that offer that kind of opportunity anymore. Here, we have a 990 hour course where my students learn from a journeyman machinist, and then I turn them over to an employer who spends another five years training them. The employers are excited because the students come to them with a knowledge base that they can work with."
Maxfield had the responsibility of purchasing the machines for the program, writing the curriculum and training the instructors. His students are required to complete the manual portion of the course before moving on to CNC machining. "You cannot be a really good CNC machinist unless you have good problem solving skills," said Maxfield. "Machinists need to know how to read blueprints and how to be safe, as well as how to do simple things by hand, such as sharpen a drill bit and calculate feeds and speeds from scratch. The best CNC set-up people and programmers are people who come from the manual side because they understand cutting dynamics, tooling, jigging and fixturing and so forth. Additionally, there is still a demand for manual machining that I do not believe will ever go away."
When it came time to select the manual machines for his program, Maxfield chose Kingston HJ 1100 engine lathes, which were purchased through Kingston dealer Machinery Consultants (Salt Lake City, UT). "We selected the HJ 1100s based on a recommendation that they could withstand the abuse that students can sometimes give a machine," said Maxfield. "Mistakes happen with seasoned machinists, so a student is certainly going to have things that are going to go wrong. Sometimes parts go `thud' on a machine. My Kingston lathes have had this happen many times. I had one student run a cross slide into a chuck and the machine withstood it. The Kingstons have stood up to everything. They are affordable but they are stout."
Students use high-speed steel tooling on the HJ 1100s. They cut out very soft steel, so they use a lot of 1018 low carbon steel. The school currently has six HJ 1100 engine lathes.
Projects, such as threading and measuring, are used to teach focus and discipline as well as technique. "I have many projects that involve threading because as a machinist you have to be able to see your point thread," said Maxfield. "That is a necessity. My students cut unified threads, step threads and multi-start threads. This allows them to get a feel for the concentration on that project and focus on what they are doing. A good machinist has good focus and is not swayed by other things happening in the shop. The same applies to measurement. Focusing on instruments allows the students to judge whether they have a good part or not."
Students have the opportunity to showcase their skills and creativity with their capstone projects. Each student proposes a project, creates a blueprint and then builds the project within a 60-hour period. Final projects so far have included a super-sized golf driver, a modified Volkswagen engine, a miniature V8 engine and several steam engines.
Student Tyler Thomson said that the machining program provides him with a creative outlet. "I can take a piece of scrap metal and turn it into something beautiful," he said. More importantly, he is developing a skills set that will provide him with a career doing what he enjoys. "When you have a set of blueprints and you are able to follow them and get a project done exactly right, it feels really good," he added. While the precision aspect is appealing to Thomson, he said the Kingston lathes are still user-friendly. "It is a super comfortable machine to work with," he said.
David Mayson was attracted to the school's machining program because it is the only one in the area where this type of course is offered. He plans to follow this course up with the CNC program. He believes that a manual machine knowledge base is an important foundation. "Learning about speeds, feeds, materials and tools beforehand can keep you from making big mistakes with a CNC," he said. Mayson said that the Kingston HJ-1100 is simple to use and operates smoothly, and he can transition easily between projects. "Also, the reference chart is great," he added.
Chad Atene is finishing up his machining studies at the school. His long-term goal is to have his own shop. While he has had some prior experience with lathes and mills, he said that the program was important for expanding his knowledge base. His final class project is a third-scale model Gatling gun made of brass, which requires a lot of detailed work. He said the HJ-1100s provide the needed spindle speeds as well as good finishes. "One thing I like about the machines is that they are fairly quiet," he added.
The MATC campus recently moved from Orem to South Orem to accommodate its growth. "We had so many businesses come to us asking for skilled students that we knew this was a trend that would skyrocket," said Director of Marketing Mark Middlebrook. "The early students in this program are finding good paying jobs that are providing them with stability and benefits."
MATC is a part of the Utah College of Applied Technology System (UCAT), a statewide system of Applied Technology Colleges (ATCs). MATC's goal is a hands-on training program for all students, both high school students and adults. The majority of programs are short term, and are flexible and inexpensive compared to four-year universities, according to Middlebrook.
For more information contact:
Mountainland Technical College
1410 Business Park Dr.
Orem, UT 84058
801-753-6282
www.mlatc.edu
Kingston Machine Tool Mfg., Inc.
5421 Business Drive
Huntington Beach, CA 92649
714-894-1648
sales@kingstonmachine.com
www.kingstonmachine.com
UT, WY
Machinery Consultants, Inc.
1390 West 200 South
Salt Lake City, UT 84104
billw@toolmachine.com
www.toolmachine.com