
PDQ, Inc. Owner Ron Gronback with new Hurco VMX42i

a multi-vise set-up on the VMX42i

PDQ, Inc. Owner Ron Gronback with a part machined on the Hurco VMX42i. This part starts as a 15 lb., 2" thick block of aluminum. Finished weight is less than 1 lb.
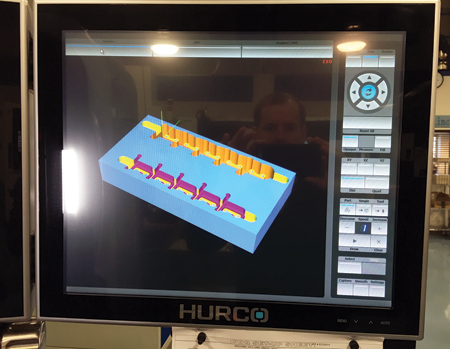
the new Max 5 graphics screen

solid rendering of a part
PDQ, Inc. was founded in 1989 by Ron Gronback, Sr. Unlike many new job shops that take on all kinds of work, Gronback implemented a targeted business plan that focused on high-precision aerospace parts from Tier 1 aerospace OEMs such as Hamilton Sundstrand and other divisions of United Technologies. Gronback, along with a small experienced dedicated team of eight, worked tirelessly at the 4,500 sq. ft. Rocky Hill, CT, shop to deliver the highest quality product on time.
Ron Gronback, Jr. took the helm in 2000 and has overseen a healthy average growth rate of 15-20% per year as the team has grown to 25 employees and the facility to 15,250 sq. ft.
Since PDQ's inception, Hurco has been a part of the company's success story. While PDQ has many different CNC machines in the shop, the PDQ team realized that Hurco CNC machines solved a problem all shops lament: the shortage of skilled labor.
"The shortage of skilled labor was the driving factor that led to buying our first Hurco," said Gronback. "We needed flexible, well-rounded operators who could set up and program on their own. With the Hurco control, we were able to train operators, even those who were new to CNC programming and set-up, and have them proficient within a few weeks."
Service after the purchase was another determining factor that led PDQ to invest in Hurco CNC machines. Brooks Associates is the Hurco distributor for Connecticut and continuously ranks as one of the builder's top U.S. distributors. "The after-market support was a critical factor," Gronback said. "Brooks Associates was able to install the machine and train us within days of receiving our new Hurco VMX42i mill."
Currently, PDQ has two Hurco VM series mills (XYZ travels of 26" x 16" x 20") equipped with a 4th axis table; a VMX30 mill (XYZ travels of 30" x 20" x 24"); and two VMX42i mills (XYZ travels of 42" x 24" x 24"). PDQ also has machine tools equipped with FANUC controls. Gronback said that eliminating bottlenecks is another reason he continues to add Hurco vertical machining centers (VMCs) to his equipment list.
"At the end of the day, it is about throughput," said Gronback. "Since the Hurco control has an intuitive and user-friendly interface, the operators are more self-reliant and comfortable programming parts. This leads to higher productivity. Our Hurco machining centers do not have the bottlenecks associated with offline programming."
Gronback in particular likes the new generation of the Hurco control that was introduced in 2015. Called MAX5, the control is equipped with multiple ergonomic features designed to increase operator productivity and enhance usability.
"The new control layout screens are exceptional. Our MAX4 control was already highly user-friendly, but the MAX5 takes it to the next level," said Gronback. "In regards to the control's NC/Conversational Merge feature, the ability to use G-code programs in the same environment as conversational programming is extremely beneficial."
The Hurco control provides programming flexibility with conversational programming, industry standard G-code programming and the aforementioned NC/Conversational Merge feature. With NC/Conversational Merge, the operator can leverage the simplicity of conversational features, such as transform plane, pattern operations, scaling, tool probing, part probing or unlimited work offsets, to NC programs. "Even tried and true G-code programmers appreciate the immense amount of time NC/Conversational can save, especially with one-offs," said a Hurco spokesperson.
PDQ's Hurco mills are equipped with another exclusive feature from Hurco that simultaneously increases throughput and surface finish quality. "The motion control system, called UltiMotion, includes numerous technological advancements that have been providing benefits to customers like PDQ since Hurco invented the technology in 2012," said the Hurco spokesperson. "Its dynamic variable look-ahead mechanism is fundamental to the motion system. The dynamic variable look-ahead is completely unlike traditional look-ahead. With UltiMotion, the control software evaluates the geometry and motion profile and makes sure there is enough look-ahead information to make optimized maneuvers. The patented look-ahead mechanism is another reason why better surface quality can be obtained in a shorter period of time."
UltiMotion also has rapid cornering capability that allows the spindle to travel through corners at high speed with negligible deviation without overshooting or stopping, which is especially beneficial when machining parts with repetitive tasks, such as drilling or tapping. For rigid tapping, UltiMotion deploys a coordinated motion control mechanism that monitors the spindle angle at all times and controls the axes to follow the spindle position. It also has the flexibility to choose higher speed/RPM to retract the tap tool out of the hole.
"As one of New England's premier aerospace suppliers, PDQ exceeded $9 million in annual sales for 2015 and continues to be recognized for customer service excellence, quality and exceeding its customers' requirements," said Gronback.
For more information contact:
PDQ, Inc.
24 Evans Rd.
Rocky Hill, CT 06067
860-529-9051
info@pdqcorp.com
www.pdqcorp.com
Hurco Companies, Inc.
One Technology Way
P.O. Box 68180
Indianapolis, IN 46268
800-634-2416
info@hurco.com
www.hurco.com
NE ONLY
ME, VT, NH, CT, MA, RI, N. NJ, NY (far South)
Brooks Associates, Inc.
300 Longwater Dr, Unit A
Norwell, MA 02061
800-458-6607
781-871-3400
www.brooksmachinery.com