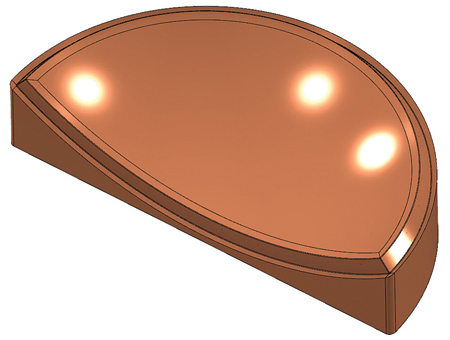
High-speed toolpaths are used for roughing operations for both parts and molds. Scoffield said, "The Dynamic toolpaths seem to be a lot faster. When we use big routers-they are not incredibly nimble sometimes-if they do not have to do a lot of moving, adjusting and retracting it saves a lot of time." Both scallop and raster paths were programmed for this cap plug.

The 7-axis robot uses a dial indicator to align a tooling fixture.
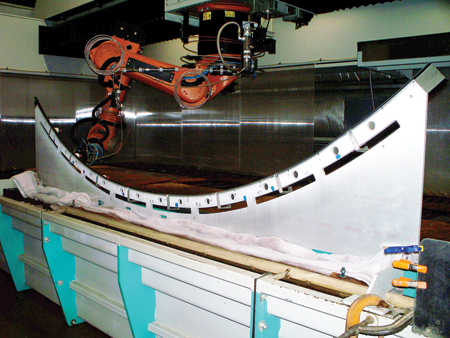
The robot uses 7-axis movement and the waterjet to trim the flange from a composite aircraft barrel frame. The robot also has router and drill capabilities.
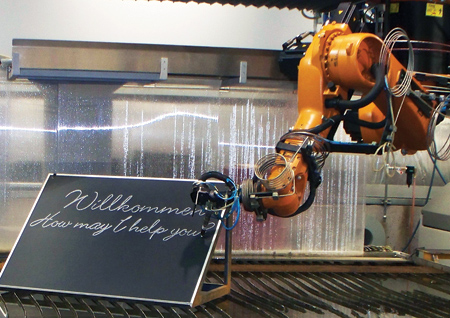
The 7-axis robot is capable of writing a message, in cursive, on a chalkboard.
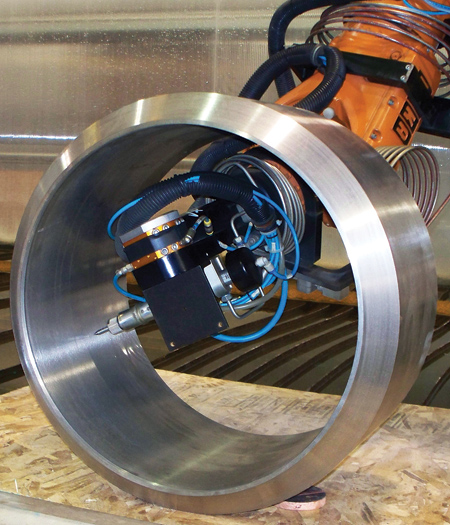
The robot's versatile range of motion allows it to cut a steel ring from the inside outward.
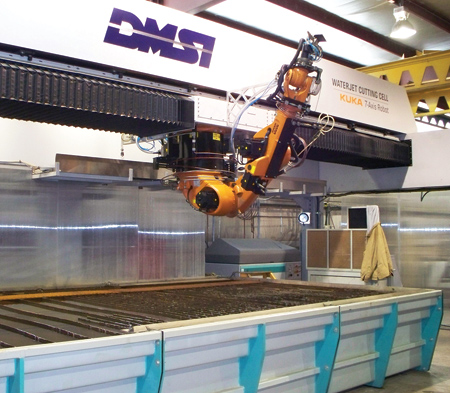
The robot demonstrates its height range.
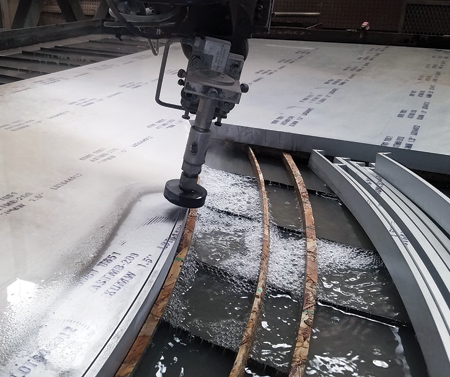
The robot cuts arcs out of 1.5" aluminum.
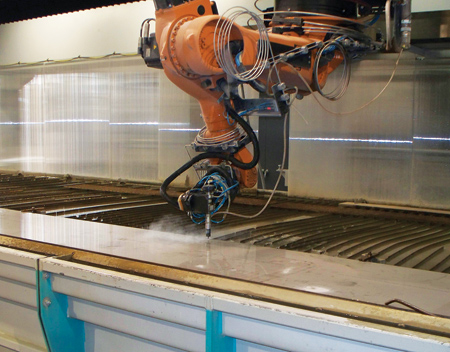
The 7-axis robot cuts through a piece of stainless steel measuring well over 1".
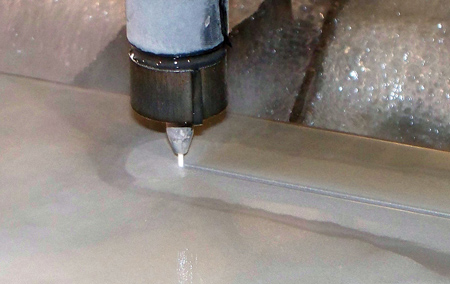
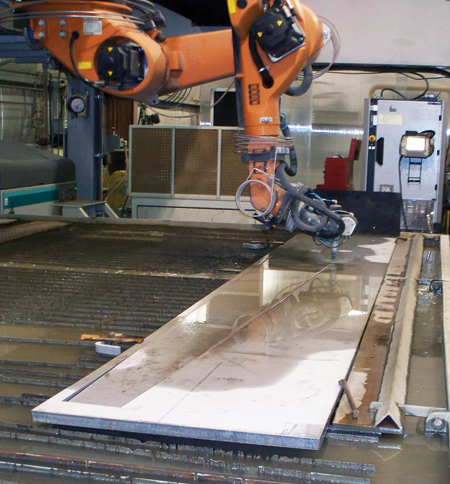
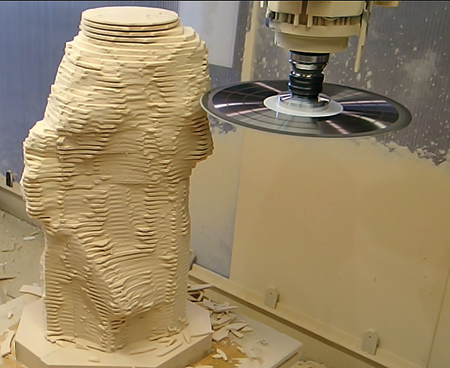
A 5-axis router uses a 12" carbide-tipped saw blade to rough out a foam mockup of a bust, testing a program that will later be used on marble.
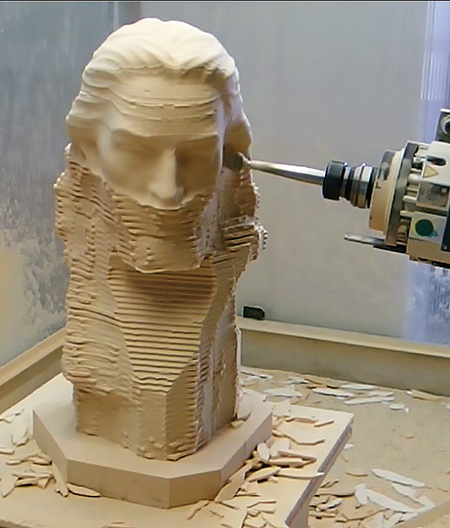
The router uses a 1" lollipop end mill and a 5-axis parallel toolpath to smooth out the rough saw blade cuts and start to form the bust.
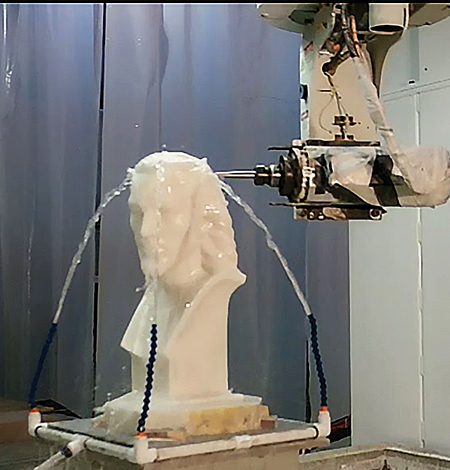
One of DMI's 5-axis routers carves a bust of Christ out of marble. The bust is placed in a tank and water is continuously pumped over the cutting surface.
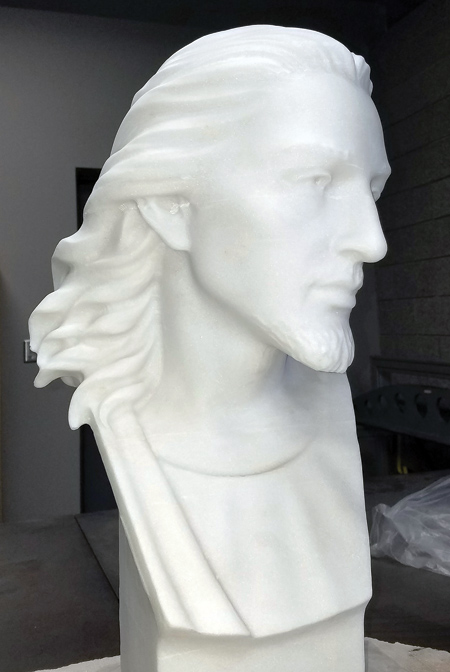
The finished marble bust of Christ.
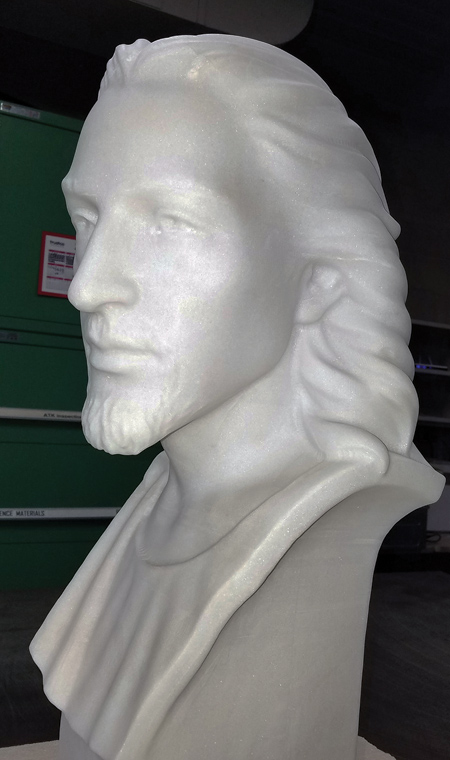
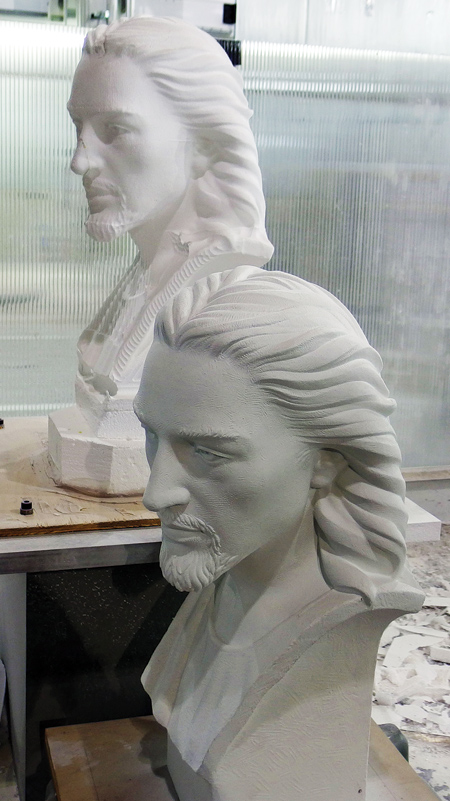
A side-by-side view of the marble bust next to its polystyrene counterpart.
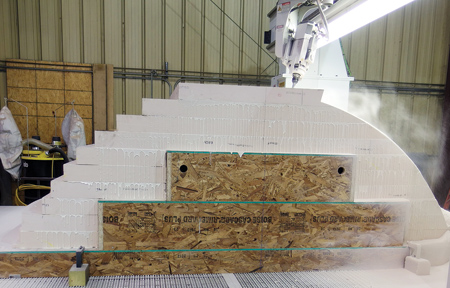
A 5-axis router uses a 1" flat end mill to shape a large dome that will be implemented to create the mold used in the construction of flight simulators.
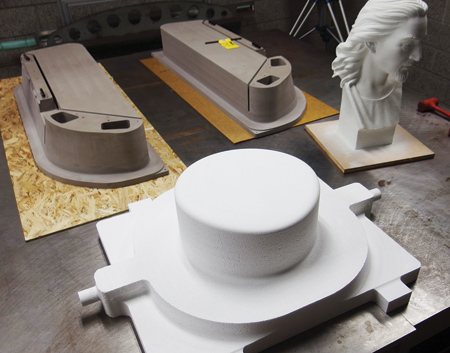
Various parts can be machined using the 5-axis router. Shown are a polystyrene casting plug used to create a plastics mold (foreground); two fixtures made from high-density foam that are used to inspect aerospace parts (background); and the bust of Christ.
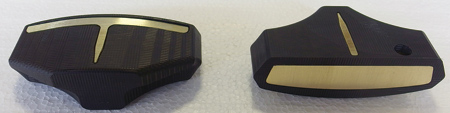
A prototype carbon putter head with a brass sight, bottom and face. The brass pieces were cut on the waterjet, and the carbon fiber was cut on the 5-axis router.
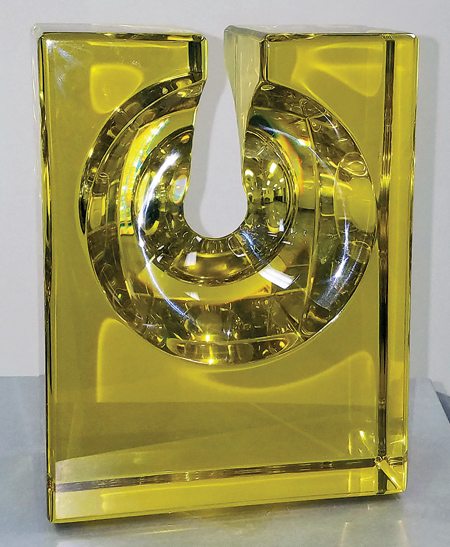
Glass art
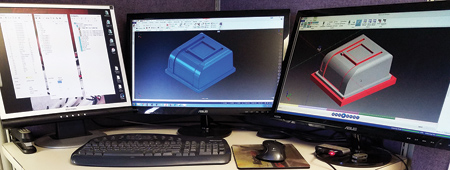
Scoffield's workstation is an example of the powerful equipment provided by SolidBox.
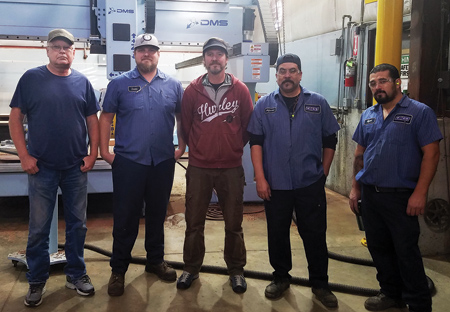
The shop crew: Ron Jensen, Dave Edgington, Nate Scoffield, Alfonso Torres, Miguel Popoca. Not pictured: Mike Long
The introduction of 5-axis machining centers was revolutionary to manufacturing for many reasons. One of the most impactful is that the extra axis allows a part to be machined on all sides and everywhere in between, reducing set-up time and allowing for more complex geometries to be achieved.
When a 7-axis robotic arm is added to an abrasive waterjet cutting operation, additional cutting and drilling can be accomplished in any direction. This is achieved by combining the flexibility-provided by the sixth and seventh axes-with a router to machine a given part without having to move it.
With the addition of these sixth and seventh axes, Diversified Metals Services, Inc. (DMSI) has been able to expand its waterjet and router cutting capabilities to accommodate a wide range of sizes and materials, allowing it to cut faster than ever before and with significant time savings.
DMSI works with customers ranging from the aerospace to medical to architectural to signage industries. It machines 3-D components on one of five waterjet machines-one 7-axis (the robot), three 5-axis and one 3-axis-as well as two 5-axis routers and one 3-axis router when necessary. The fastest 5-axis machine operates up to 87,000 PSI. Abrasives are 60 grit. While one machine cuts 3-D shaped components to customer specifications out of 3/4" thick carbon composite, another cuts similar components from glass for artistic or architectural applications.
According to Mike Long, DMSI President, programmers need to be well-trained in programming for the different industries the company serves. For example, the operator building a program for signage must recognize the need for flexibility in his program as to how the sign will be built. However, if he is building a program for aerospace or medical components, he must be familiar with a broad range of industry constraints to be able to achieve the customer's design. With tight lead times, there is no room for error.
"The protocol of managing a small operation and serving very large customers can be a challenge in that there is zero acceptance of any component that is not to the drawing. If we have one-offs, there is no room for error. We have one billet, we make one part," said Long.
In addition, turnaround times can be tight-once a design is finalized, the part is due on-site the next day. Finally, composites need to be handled in a certain way, otherwise micro fractures can occur. These are tiny cracks that can only be seen with a special machine, and usually discovered after the part has left the shop. In order for the whole operation to work smoothly, the team of three programmers and 20 machinists needs to be able to mitigate errors and downtime. Their CAD/CAM software is instrumental in verifying that the program is airtight and that the actual machining is done right the first time.
One project that tested the software's capabilities involved the machining of a marble bust of Christ. After using a portable CMM arm and laser tracker to reverse engineer a clay bust supplied by an artist, the programmers built the cut paths in the Mastercam CAD/CAM software. It was one of the first projects they did with the 5-axis router. Programming the cutting tool to avoid collisions between the router head and the marble stock, while machining the complex contours of a face, required some additional thought.
The software's Verify function played an important part in ensuring that these collisions did not occur. However, according to Nate Scoffield, head machine programmer, some customization was needed to build the toolholder. The bust is more of a square shape, but the software prefers that a holder be a cylindrical shape. The team built custom holders by using the dimensions of the actual transom head, yielding a holder that was bigger than needed to ensure there was enough clearance.
"Using Mastercam's Verify feature, we had no collisions with the marble, which would have been catastrophic," said Long. "The ability to see the job within the software allowed us to preview the cut path so we were able to make sure that collisions with the actual marble did not take place." Scoffield added that he learned many additional functions of the software by doing this project, including the compare feature, which indicates where a load is light or heavy on a color map.
"The bust was very complex and detailed," said Scoffield. "We are able to apply the knowledge we acquired from that particular project to everything we do today. It has also been beneficial for the aerospace industry."
Conquering Aerospace Challenges
Aerospace work requires a detailed process from the beginning, involving all departments from design to finish. The first step is to determine whether they can fulfill the requirements on the purchase order. From there, a committee reviews the job and agrees on the tool types, toolpaths and machines to be used to complete the part. "For the most part, not a single line of NC code goes through here without some kind of review, a simulation or a conference with the programmers as well as the machinists," said Long. The team imports the specifications directly into the software, and then orients it based on machine types. Then they determine the stock material and consider special toolpaths to reduce air cuts and time. "We try to get an idea of how we will accomplish the task by consulting with others. There are guys here with a lot of machining experience," said Long.
Dry runs are completed to ensure that the toolpaths are in place and in line with the fixturing, which poses an additional challenge when working with a 5-axis machine. "With 5-axis waterjet cutting, the tool is infinite," said Long. "It is lethal in 50 feet so anything below the fixtures can be destroyed. We need to path around or build a fixture so there is no interference with the fixture itself. That is quite a challenge in some cases." Using the software's Verify function, the team can perform a pre-inspection of sorts, indicating where the toolpath might have exited, and when more material was removed than was specified in the code or in the toolpath. Often, fixtures and tools are created for one time use.
Once everything is verified, it is time to manufacture the part. High-speed toolpaths are used for roughing operations for both parts and molds. Scoffield said, "The Dynamic toolpaths seem to be a lot faster. When we use big routers-they are not incredibly nimble at times-if they do not have to do a lot of moving, adjusting and retracting, it saves a lot of time."
The waterjet system can cut nearly any shape from materials ranging from 1/8" to 8" thick, with a radius as tight as 0.020" and tolerances up to +/- 0.005". The sixth and seventh axis robotic heads can cut in virtually any direction owing, in part, to their inverted position. According to Long, most robots are pick & place, where the robotic elements move the stock and the cutter is stationary, while their robotic arm is actually machining due to its inverted position. The sixth and seventh axes allow the robot to move along a cut path of 24' rather than perhaps 10'. Scoffield pointed out that the longer cutting path allows more parts to be machined at one time. When combined with the router, the robot provides additional cutting and drilling functions.
The investment in so many powerful machines required a considerable upgrade to DMSI's hardware infrastructure. The team relied on their Mastercam reseller, Marc Sullivan of Remote Machine (Salt Lake City, UT), whom Long has known for more than 40 years. He not only helped them with the bust of Christ project-Long said that Sullivan also supported them in some areas of the software that they had not visited and in determining which toolpaths would work in a particular job. He also connected Long and Scoffield with SolidBox (Salt Lake City, UT), which specializes in providing hardware that can handle the demands of SOLIDWORKS and Mastercam.
"Because they had a lot of issues with machines and computers crashing, I told them the only way they were going to know for sure if it is the software or computer is to buy a computer that has been tested and proven to work with SOLIDWORKS and Mastercam and guaranteed by people to do so," said Sullivan. Long decided to go with SolidBox due to its expertise in the field.
Tanner Knight, lead programmer at SolidBox, said the company performed a diagnostic of DMSI's workflow and supplied them with two work stations that would give the machine programmers enough power to process a toolpath without overtaxing the machine. "Once we discussed what they needed from the system and got the actual specs figured out, we stripped out any unnecessary software, creating a nice, firm platform for Mastercam," said Knight. "Then we installed Mastercam and benchmarked it so we knew the installation was rock solid." When DMSI received the system, SolidBox helped them integrate it into their network and ensure that the workflow was enhanced by the workstation rather than impeded.
DMSI has built a network of business partners on which it can rely when making the necessary investments in powerful equipment and software when complex jobs become just a little more complex. By adding a 7-axis robotic head to its already impressive machining operation, DMSI has been able to perform multiple operations at one time, serving many industries all at once. The key to doing it all faster is the equally powerful CAD/CAM software that now runs seamlessly on the right workstation.
For more information contact:
Diversified Metal Services Inc.
2845 West 9th South
Salt Lake City, UT 84104
801-972-6093
dmsi@divmet.com
www.diversifiedmetalservices.com
Michelle Nemeth
CNC Software, Inc.
671 Old Post Road
Tolland, CT 06084
800-228-2877
info@mastercam.com
www.mastercam.com