
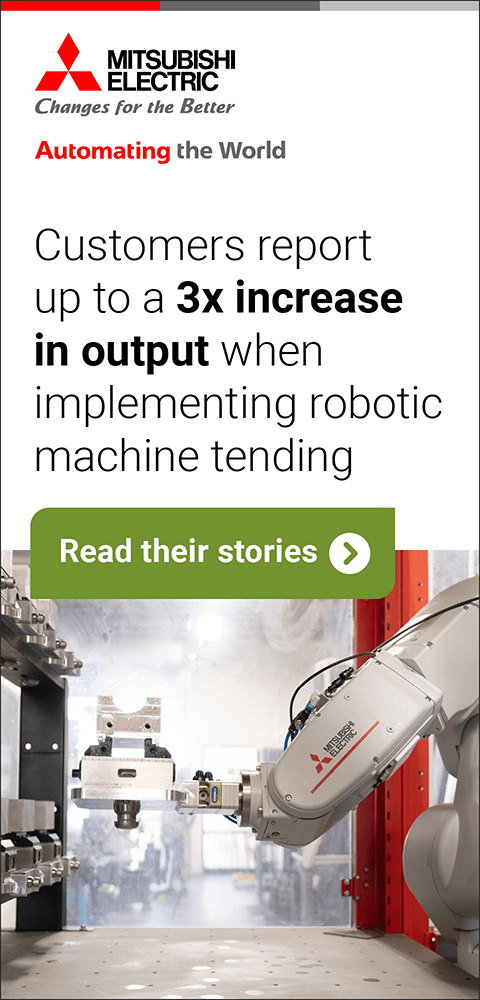
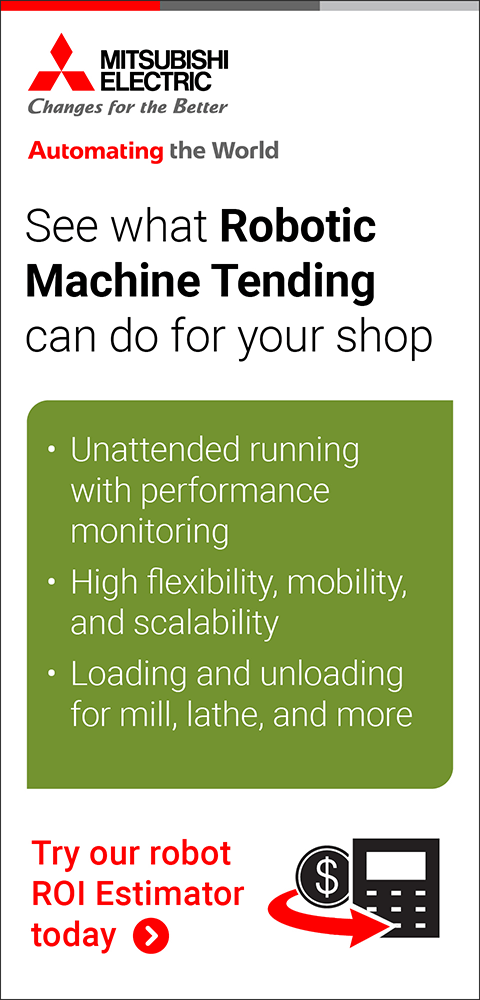




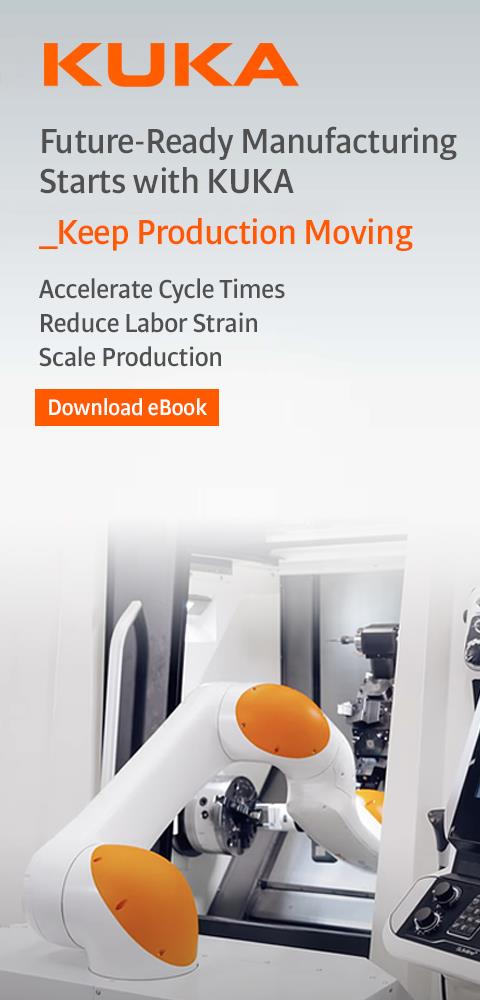
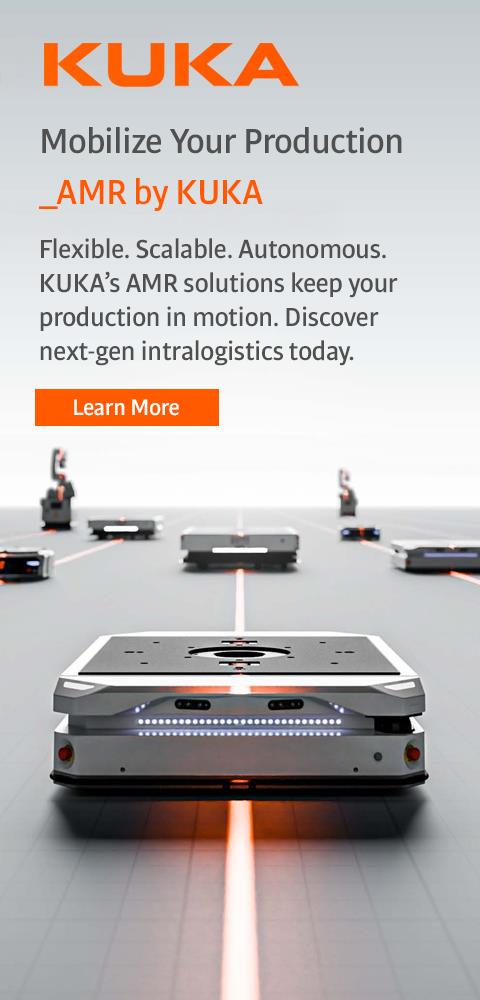
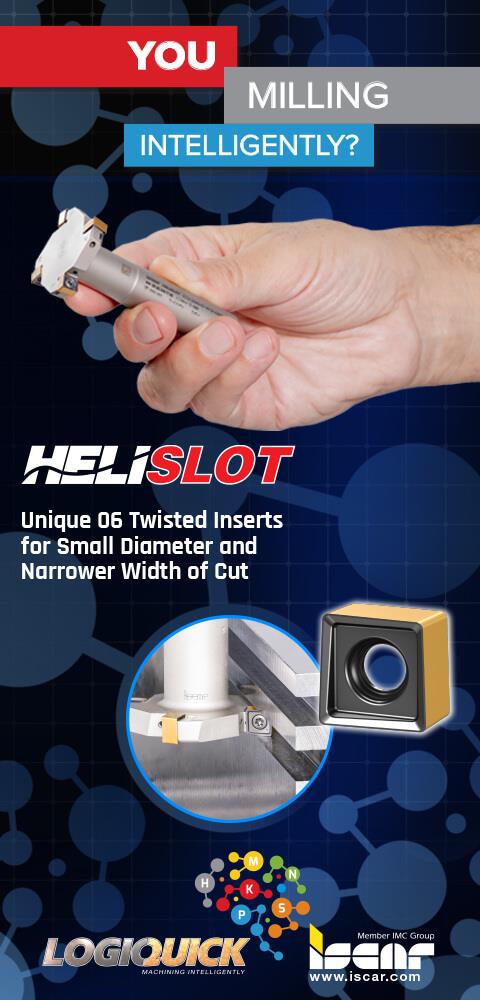
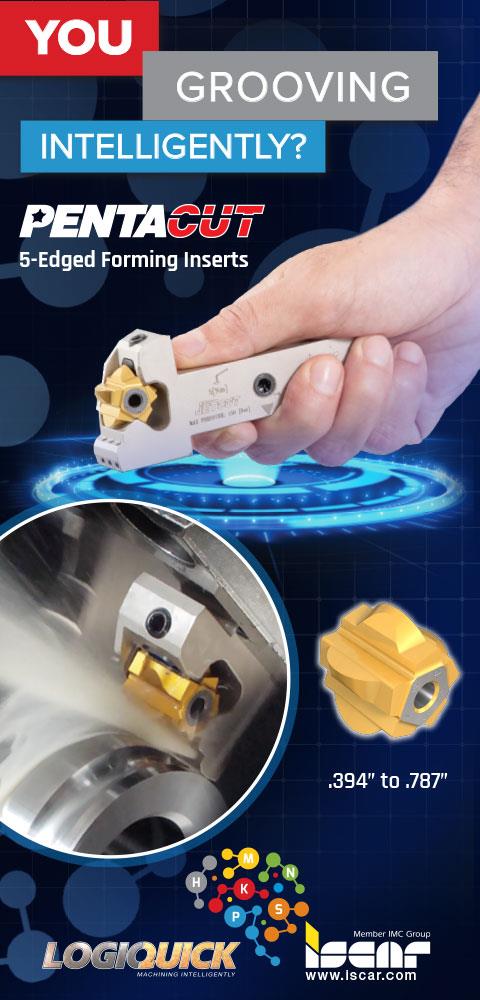
New Function Supports Step Cutting
May 1, 2022
With the addition of the patented iGroove function, Sodick has put a new spin on the capabilities of wire EDMs. Featured in three of Sodick's existing wire EDM lines (ALN, ALP and ALC), the addition of the iGroove and Stepcut functions are already showing improved results in accuracy and surface quality while simultaneously reducing wire consumption, the company reported.
iGroove
"The iGroove function is a new feature in the Sodick wire EDM lineup that cannot be found anywhere else," said a company spokesperson. The function rotates the wire from the top to the bottom of the workpiece, allowing the entire surface of the wire to be used during the cut. This eliminates the need for taper compensation due to wire wear. This twisting mechanism creates a consistent, fresh electrode surface from the top of the workpiece to the bottom, and, as a byproduct the wire feed speed can be slowed down. This leads to reduced wire usage without drawbacks that would otherwise be seen in slowing the wire feed, such as excessive electrode damage. These wire speeds are sourced from the built-in ALN conditions.
Stepcut
In tandem with the iGroove function, this lineup of wire EDM's also support step cutting. Step cutting is a process in which a workpiece of variable height is cut with a single program. This is possible due to Sodick's "Thinking Circuit," which makes a 2D mesh as it runs its initial cut to remember the approximate thickness of the workpiece in each location. With this mesh of thicknesses, the machine can automatically optimize its cutting conditions as it runs skim cuts.
"This simplifies the process greatly from the user's perspective because only a single condition is needed and the NC program can be written without any special instructions," said the spokesperson.
Results as Reported by Sodick
"Since the release of the iGroove series in Q4 of 2021, initial results have shown increases in accuracy, surface finish and especially wire savings," said the spokesperson. "It has been found that this machine lineup is especially suited for thick workpieces (60 mm or greater). Workpieces with varying thicknesses as well as workpieces that require multiple passes benefit from this technology the most. However, improvements are seen on less complex workpieces when compared to previous models."
Benefits include:
- Accuracy: By rotating the wire, the workpiece is always cut with a fresh wire surface. This advantage thereby improves the geometric accuracy and surface quality without having to compensate with taper or increased wire feedrate.
- Reduced wire use: Initial trials have shown that wire consumption can be reduced by over 25% on any given workpiece cut. Additional savings are seen on cuts that require multiple skim cuts.
For more information contact:
Sodick Inc.
601 Commerce Drive
Schaumburg, IL 60173
847-310-9000
sales@sodick.com
www.sodick.com
< back