
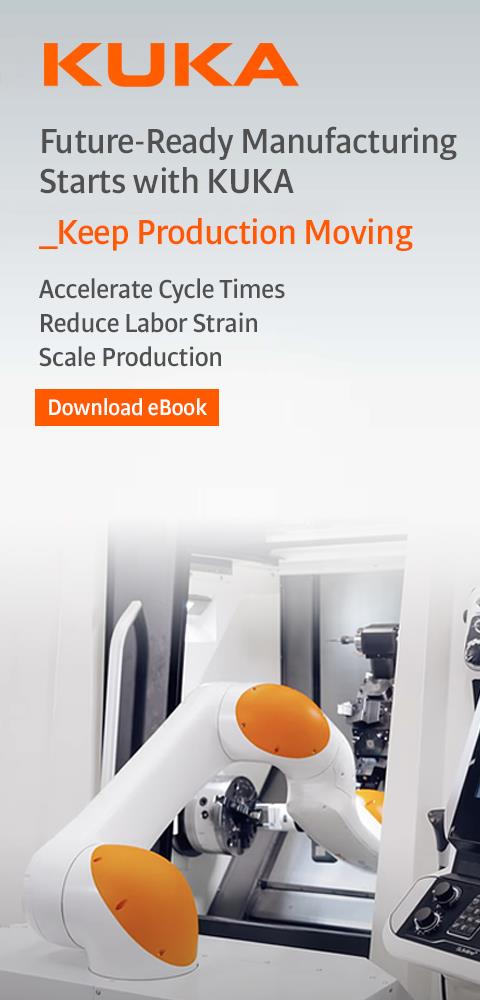
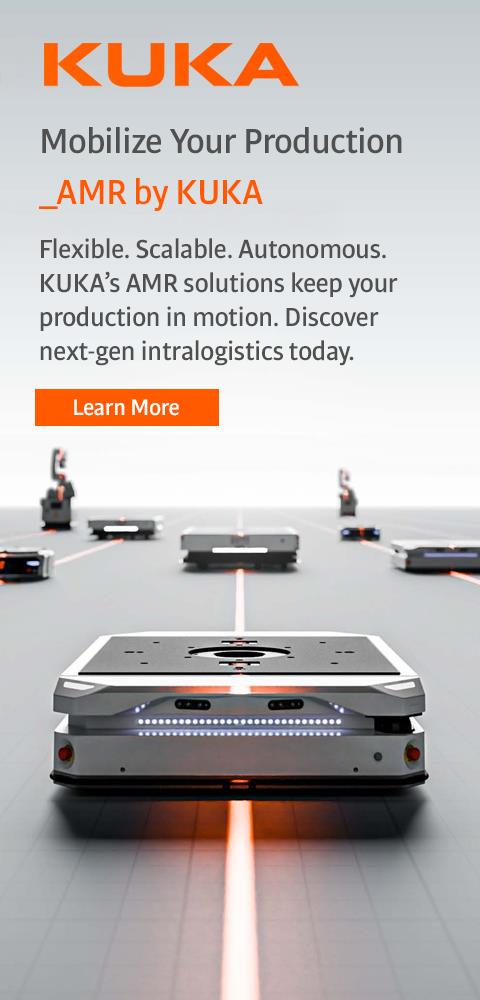
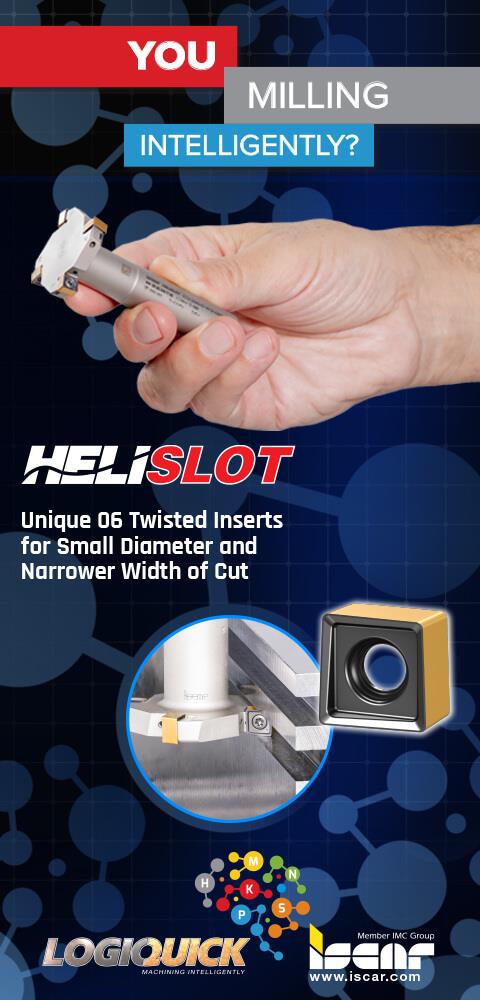
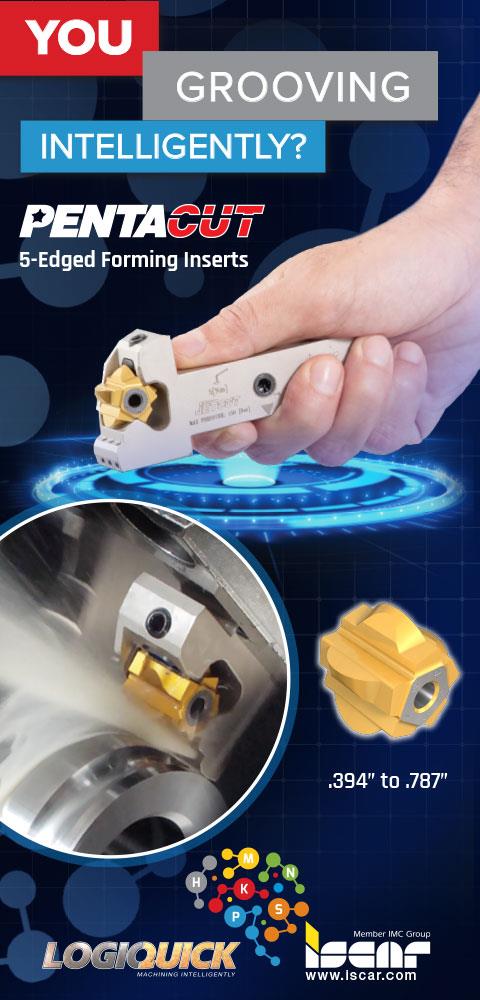
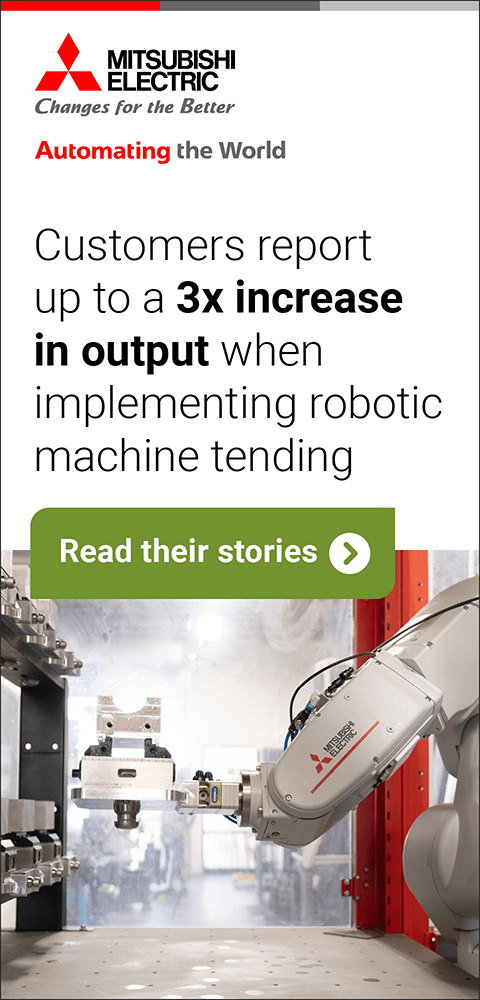
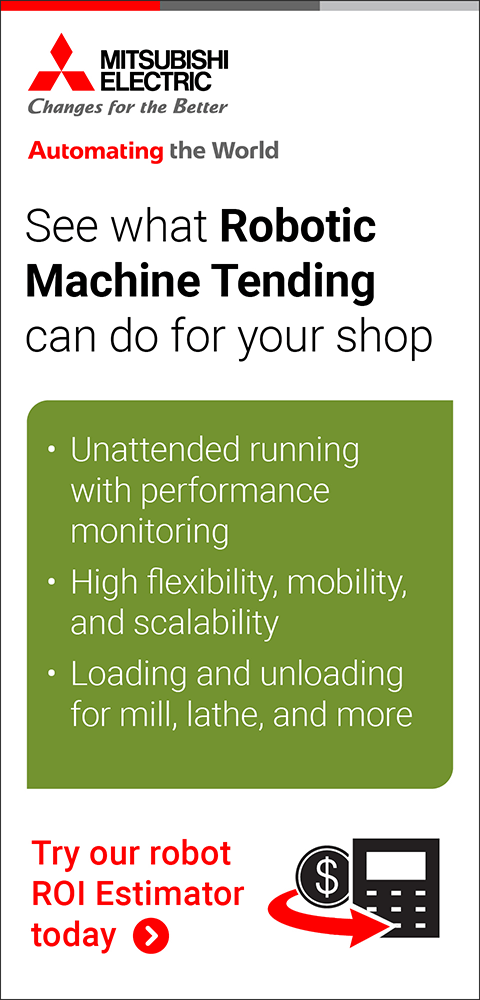




Qualifying Metal 3D Printer for Production of Aircraft Components
June 1, 2020

"Sample additively manufactured parts demonstrate how VELO3D's unique metal printing process can produce geometries that were previously impossible. Applications include aviation, oil & gas, aerospace and other industrial markets," said a company spokesperson.
VELO3D and Honeywell Aerospace have announced a partnership to qualify VELO3D's Sapphire system as a viable manufacturing platform for 3D print production of aircraft components.
The Sapphire system was selected for its unique capabilities for building highly complex geometries without the requirement of support structures. This enables customers to benefit from substantial time, cost and quality improvements," said a company spokesperson.
The VELO3D Sapphire system will be in Honeywell Aerospace's Phoenix facility. The qualification process is focused on Inconel, a nickel-based super alloy well suited for extreme temperatures. VELO3D will provide its expertise in developing suitable parameter sets for Honeywell Aerospace to complete material qualification utilizing the Sapphire system to achieve optimal material properties. The qualification process is anticipated to be complete by the third quarter of this year.
"We are qualifying VELO3D's Sapphire system with the aim of printing geometries that cannot be fabricated on existing 3D metal printers. VELO3D's technology will help Honeywell develop new production part applications while also meeting our material requirements for qualification," said Dr. Söeren Wiener, Senior Director of Technology and Advanced Operations for Honeywell Aerospace. "We intend to qualify this equipment through repeatability testing in our production environment, including build and post-processing, to generate an acceptable set of material property data and qualification of flight hardware."
"The geometric enablement we are able to offer customers like Honeywell Aerospace allows them to print what used to be `impossible parts' and, yet, do it with a strong business case of improved cost and better quality," said Benny Buller, founder and CEO of VELO3D. "We are excited to partner with Honeywell to demonstrate that 3D metal printing is a viable production manufacturing method for a wider range of end-use applications."
For more information contact:
Velo3D
511 Division St.
Campbell, CA 95008
408-610-3915
www.velo3D.com
< back