
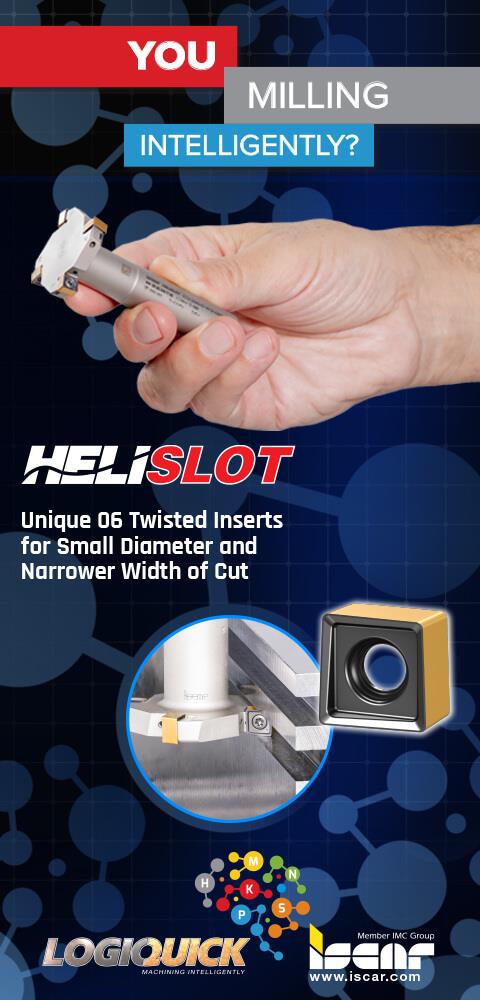
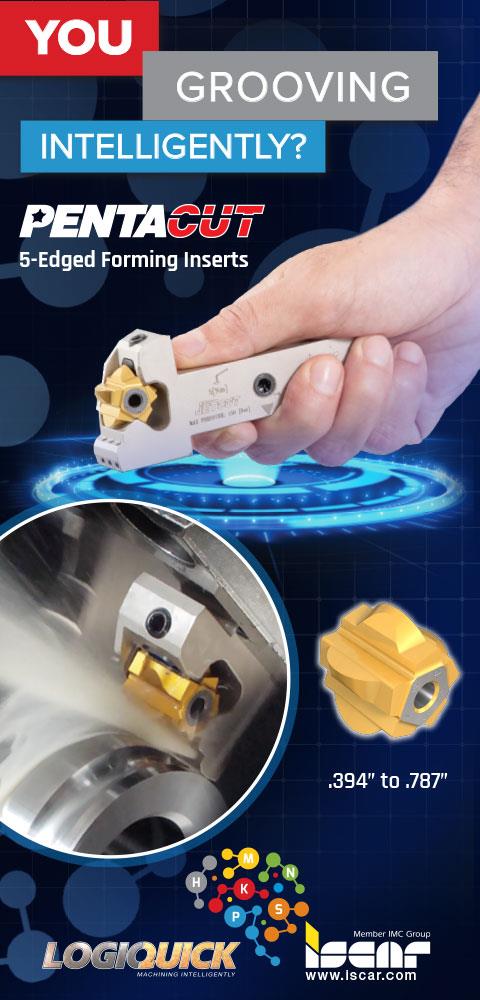
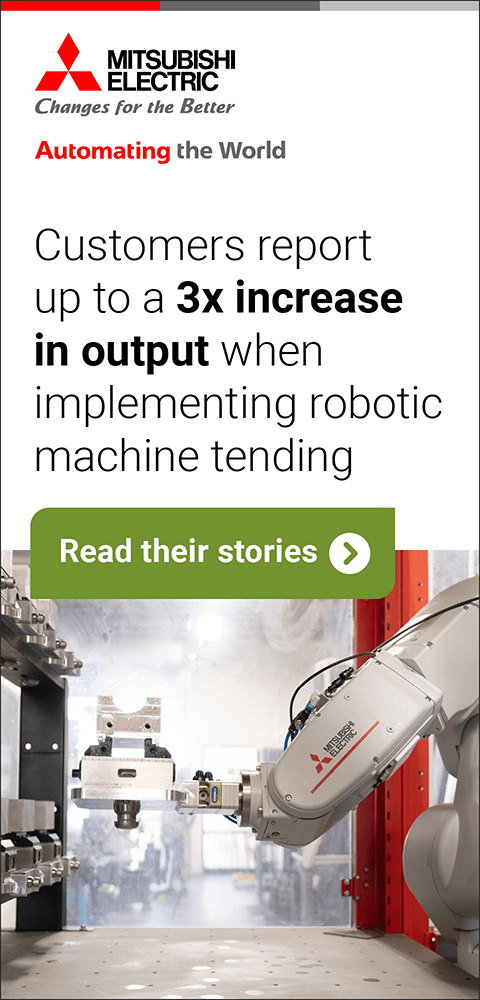
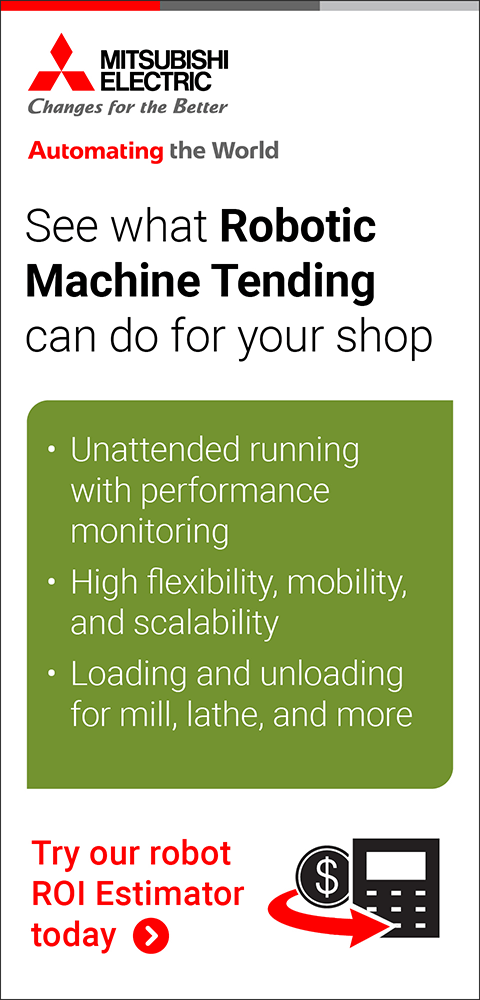




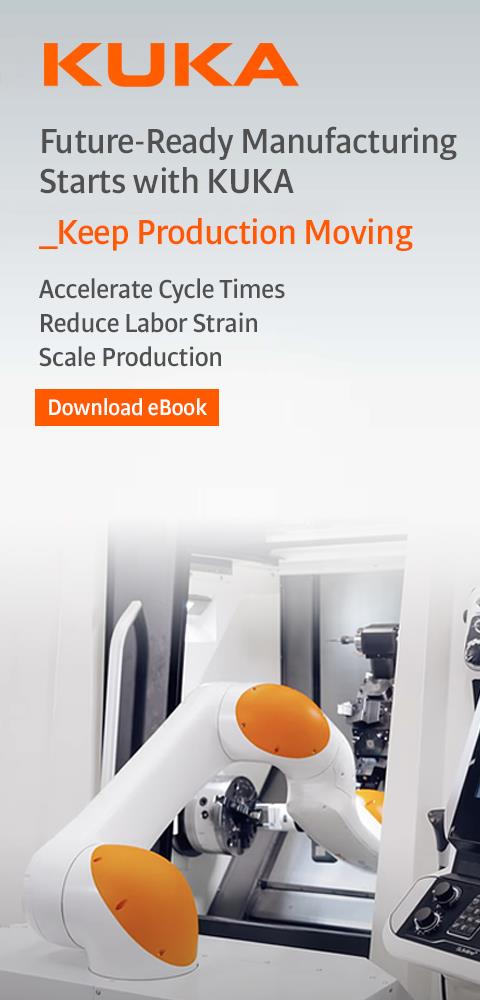
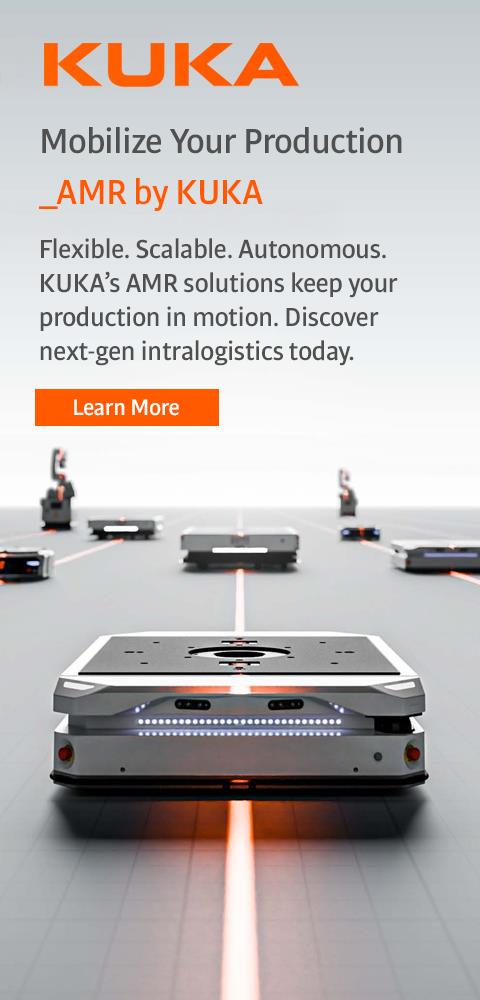
The MIM Advantage
July 1, 2022
Smith Metal Products has announced its Metal Injection Molding (MIM) cost advantage over costly high-performance metals requiring significant machining to achieve the final part geometry.
"When Titanium, Inconel or other expensive metals in bar, rod or blocks require substantial hog-outs or hollow-outs, a sintered MIM part may cost less than the raw material alone prior to machining," stated Todd Jensen, General Manager at Smith Metal Products.
"With MIM feedstock only costing approximately 20% to 25% more than raw Titanium or Inconel, the final net shape for a MIM part uses approximately 50% or less material volume than the raw unmachined materials," said a company spokesperson. "Additionally, machining time costs money, and in some cases excessive material is left on the parts just to save money, even though that added weight is not desired. Therefore, a significant cost advantage comes into play for Smiths MIM capabilities and presents cost advantages and great opportunities for product manufacturers."
In recent months, Smith Metal Products has landed new projects for aeronautics, firearms and medical components due to the high cost of many high-performance materials. These projects were previously machined parts and fit the MIM criteria being typically less than 100 grams and lengths up to 4" by .25" thick or can be "cored out" to have thinner wall sections. Smith can help customers trim down part designs with free basic Design for Manufacturability assistance. Annual volumes for MIM components start at roughly 15,000 and range into millions per year.
Smith Metal Products 3D Binder Jet Metal Printing capability is designed to support a customer's research and development efforts with a bridge to MIM molded parts. "This capability is especially desirable for reducing time-to-market developmental programs. In addition to not requiring time-consuming and expensive mold building to evaluate MIM parts, the new process can eliminate and/or significantly shorten lead time from R&D into full volume production," said the spokesperson.
For more information contact:
Smith Metal Products
15045 Per Road
Center City, MN 55012
651-257-3143
sales@smithmetals.com
www.smithmetals.com
< back