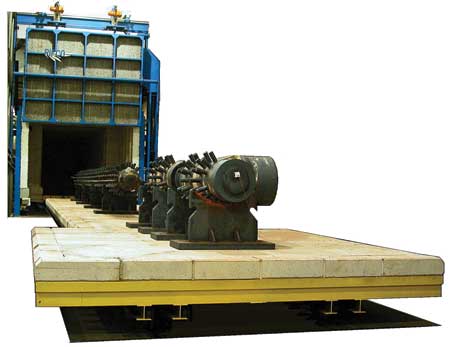
Custom-engineered T-shaped car bottomed natural gas fired furnace now undergoing final installation and calibration sequencing. Thirty-eight burners provide 28-million BTUs of computer balanced heating capacity throughout its 15 ft. wide x 15 ft. long x 10 ft. high T-head section and the 10 ft. wide x 10 ft. high x 75 ft. deep overall table size.
East End Welding (EEW), a large specialty welding company located in Brimfield, OH, recently debuted a cavernous, custom-designed stress-relief furnace. The enormous oven is projected to satisfy the stringent fabrication requirements of its largest projects, ensure quality and improve customer delivery cycles.
EEW is also a producer of high-pressure steam components for the power generation industry. For the latest innovation, EEW contracted with Robbins Industrial Furnace (RIFCO) of Sheffield, OH, to design the mammoth furnace, with computer-controlled natural gas burners deliver 28.5 million BTU of balanced heating throughout its 75-foot depth. The furnace is car-bottomed with a T-shaped configuration at the open-end measuring 15 ft. wide x 10 ft. high x 15 ft. deep. The remainder of the car measures 10 ft. wide x 10 ft. high x 60 ft. deep, accounting for the overall length of 75 feet deep. The load capacity of the car is 300,000 pounds. Most of the structural components of the furnace were fabricated in-house by EEW.
"We had been building fabrications in excess of 50 feet for some time," said an EEW spokesperson, "and the trend with our customers is toward even larger ones. The area's largest outsourced furnace services could only offer us 35 feet in depth. Some customer requirements do not allow fabrications to cool between welding and post-weld heat treating (PWHT). Shipping off-site to perform stress relief usually involves additional delays, transportation costs and concern over loss of control of project elements. So it was clear that we needed to build our own furnace in-house, and we had to go big.
"At 75 feet, our new furnace can handle most any of the projects we have seen to date with room to spare. We are fairly confident this furnace is the largest job shop furnace in our region."
"Much of the beauty of this beast-of-an-oven lies in its sensitive temperature control via the all-digital computerized management system for the 38 natural-gas burners interspersed throughout its depth and height. The system imparts precise burner firing cycles and pulsing strategies to evenly heat all sectors of the interior. Computer pre-programming offers an almost endless variety of balanced temperature ramp-up, soak cycle and ramp-down recipes-all with precise multiple-zone monitoring and documentation. Typical stress-relief temperatures are in the 1,200 degrees F. range, and the system was designed so that additional heating up to 1,850 degrees F. can be attained," said a company spokesperson.
Stress-relief or PWHT is often required after the fabrication of large carbon steel components to restore dimensional stability after welding; for pressure parts after extensive welding is performed; and following the welding of some alloys to remove heat-affected zones. Left untreated, these stresses and heat-affected zones may result in warping, distortion, cracking and loss of corrosion-resistance properties. Stress-relief or Post-Weld Heat Treatment is utilized to counteract these concerns, allowing further work to proceed, or to serve as a final treatment to ensure the designed service life is achieved. In some instances the process restores corrosion-resistance is restored to the finished part.
The welding and fabrication processes for some alloys of piping systems are much more complex and demanding than those for lesser steam systems, requiring that a precisely controlled PWHT process cycle be conducted immediately following the welding operations. This PWHT stress-relief must be performed, as the term implies, to remove stresses but also to reverse any embrittlement resulting from the welding process, thereby ensuring that the designed high-pressure service life is achieved.
"It became abundantly clear that a very large furnace capable of precise stress-relieving procedures was required, and that it was needed here under roof. It was also obvious that an addition to the physical plant was needed to accommodate it," said the company spokesperson.
After a lengthy review and design process, ground was broken for the construction in the Spring of 2011. During the early months of 2012, the oven underwent final operating calibrations and received performance certifications.
The subsequent "shakedown phase" was completed, with all results exceeding expectations, enabling EEW to offer the furnace's capabilities not only within its constituent industries but beyond, wherever oversize capacity is required for heat treatment procedures to 1,850 degrees F., with charting documentation capabilities of up to 42 thermocouples.
EEW does not offer engineering or metallurgical services, but is an ISO 9001:2008-certified operation fully prepared to meet the stringent, documented recipes and furnace-time requirements that customers may require.
For more information contact:
Steven Snowberger
Communications & Compliance
East End Welding
357 Tallmadge Rd
Brimfield, OH 44240
330-677-6000
ssnowberger@eastendwelding.com
www.eastendwelding.com