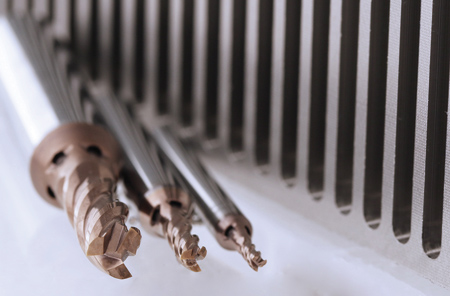
The innovative geometry of the CrazyMill Cool P&S makes efficient drill/milling from 1 mm dia. with one single tool possible.
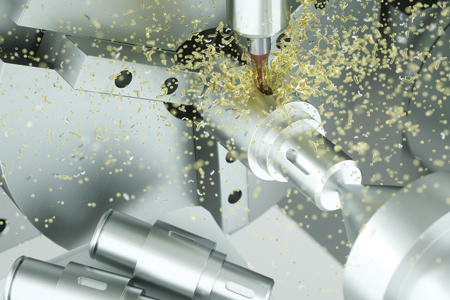
Coolant ducts integrated into the shank prevent overheating of cutting edges and facilitate the evacuation of chips from the milling area.
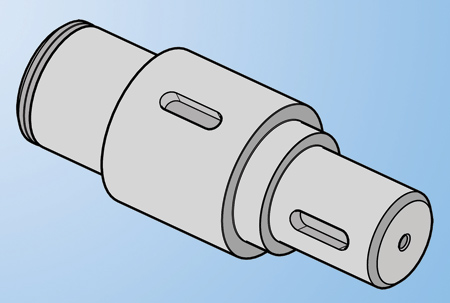
Milling of keyways is a typical application for the CrazyMill Cool P&S.

Plunging vertically (drilling), milling a groove into solid material and subsequent final finishing all in one operation is possible with the CrazyMill Cool P&S from Mikron Tool. "Anyone who needs to mill grooves and pockets in the smallest of spaces will appreciate this new tool," said a company spokesperson. A typical application is the milling of keyways for drive shafts of motors.
"Drilling and milling each have specific characteristics. To combine the strengths of both operations in a single tool is quite demanding-especially if small diameters are involved and when the result has to be reached efficiently and with high precision. This new 3-flute solid carbide plunge mill offers features that make it a really unique tool," said the spokesperson.
"Due to a special cutting-edge geometry and a stable process, vibration-free plunging (drilling) is possible," continued the spokesperson. "A correction in the center stabilizes the central cutting edge and reduces penetration force. The especially large chip area in the top section permits it to absorb a good quantity of chips during the drilling process and then evacuates these laterally into the equally enlarged chip flutes. Adapted chip and relief angles, together with stable cutting edge corners, avoid lateral hooking up and the subsequent breaking out of the cutting edges due to vibrations, which is one of the central problems when drilling with a milling cutter."
As with other mills of the CrazyMill Cool family (two and four flutes), this new tool has coolant ducts integrated into the shank, which bring the coolant directly to the cutting edges and affords constant and targeted cooling. This prevents the overheating and chipping of the edges even with high speeds and feeds. The chips are continuously flushed from the milling area, which may not be possible at times in tight and angled spaces with conventional external coolant supply. These geometry and cooling factors, combined with a heat- and wear-resistant coating and the use of an ultrafine grain carbide, offer enhanced performance.
"A few criteria have to be considered when choosing the right milling cutter," said the spokesperson. "When machining a keyway, for instance, a lateral finish milling is necessary and therefore the tool diameter has to be chosen accordingly. Generally, the tool manufacturer recommends users to adhere to the guidelines in regards to the indicated cutting parameters for drilling and milling processes."
A practical example: with this new plunge-mill, the keyway of a gear workpiece is milled from A to Z. In the first step, the mill (diameter 2 mm/.079") plunges vertically in to the material, directly down to a depth of 1xd, with a speed of 120 m/min (394 SFM) and a feed of 0.002 mm (.00008") per revolution and flute. Subsequently, the groove is milled into the solid material, while maintaining a feed of 1xd, increasing the cutting speed to 200 m/min (656 SFM) and the feed to 0.007 mm/Z (.00028"). With the finishing operation, the final keyway dimension as well as required surface quality are reached.
CrazyMill Cool P&S is available from stock in diameters 1 to 6 mm (.039" to .236") and for milling depths up to 2.5xd. All milling cutters have a high-performance surface coating and feature three to five shank-integrated coolant ducts.
For more information contact:
Mikron Corp. Monroe
200 Main Street
Monroe, CT 06468
203-261-3100
mmo@mikron.com
www.mikron.com