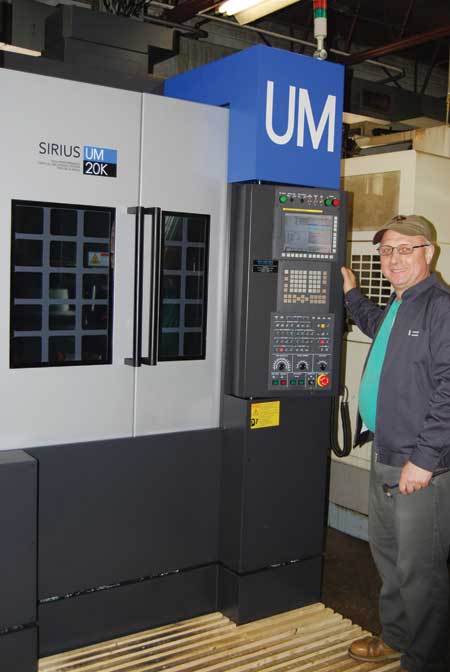
Avers Machine & Mfg selected a Hwacheon Sirius UM VMC to upgrade its milling capability and improve set-ups. Operator Andy Zgiet said, "I quickly learned to appreciate the new machine's accessibility and ease of operation."
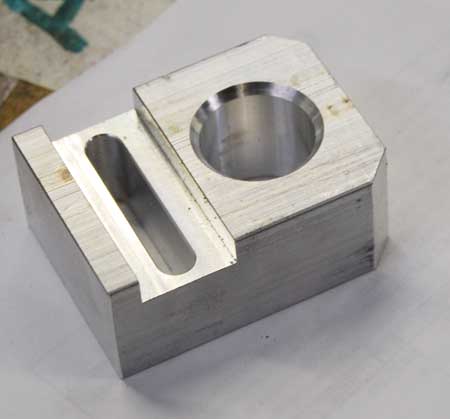
The Hwacheon 20,000 RPM spindle is integrated within the motor to limit vibration, noise and power loss at high speed rotation. "Standard Hwacheon software (HSDC) monitors the spindle for possible thermal displacement and makes necessary adjustment in real time, avoiding wasted cycle time and promoting milling precision," said a company spokesperson.
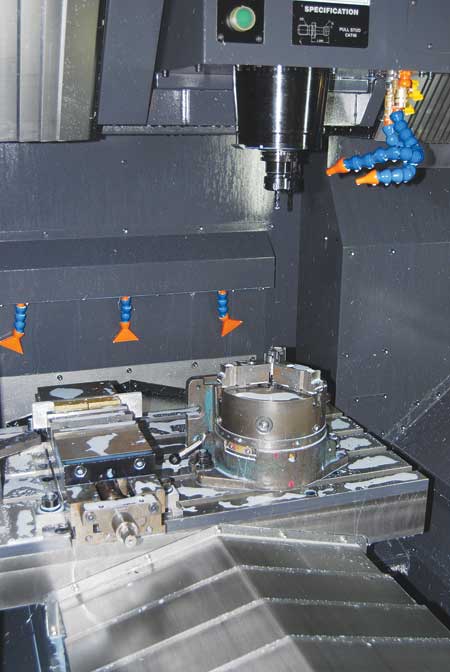
Avers created a new fixture for the machine that allows it to machine four aluminum parts for a packaging customer complete in one set-up, taking only 5 minutes. Previously, the cycle time was 7 minutes to do two parts.
Avers Machine & Mfg, a high quality job shop, needed to upgrade its milling capability and improve set-ups to increase productivity. "We were looking for a larger machine to do multiple set-ups," said Chris Wellman, Vice President, Avers. "We wanted a mill with a fairly large work area, yet we had to accomplish this within limited floor space - and it had to be a high RPM machine."
The Hwacheon Sirius UM vertical machining center (VMC) fit the requirements. "We created a new fixture for the machine that allows us to do four aluminum parts for one of our packaging customers in one set-up," said Wellman. "Previously, we were taking 7 minutes to do two. Now, with the Hwacheon and the new set-up, we are doing four pieces in 5 minutes." The job includes milling, drilling tapping and creating slots.
Another job became available for Avers that the Hwacheon made possible to quote. "We could not quote the job before because we lacked the spindle RPM required to put a .062 inch end mill into a pocket running at 17,000 RPM," Wellman said. "Now, because of the additional speed the machine provides, we successfully quoted the job and we are getting greater productivity."
Avers produces precision machined components in various materials such as aluminum, tool steel, plastics, high alloy steels, stainless steels, brass and bronze, with quantities from low to higher volume and emphasis on quality of product made to customer specifications.
"Hwacheon design casts its own bases, gearing couplings and chucks. The base to me is a key component of the machine," said Wellman. "As a properly designed foundation, it provides us a much better chance at running optimally."
Heavy and stable, the Sirius UM is a high speed, high precision 3-axis vertical designed for mold and die work. The machine has an 850 mm (33.46") x 500 mm (19.70") work table with 800 kg (1,764 lb.) load capacity, XYZ strokes of 750 mm (29.53") x 500 mm (19.70") x 450 mm (17.72") and rapid positioning of 24 m/min. Rigid roller linear guide ways support stable performance at Avers over long cycles. The 40-taper tools are changed in 2.5 seconds.
According to the company, the machine design eliminates vibration and heat during machining. A bilateral gate structure distributes the vibration, weight and heat throughout the entire machine frame. The distance between the spindle and the body is designed short, so the machine stays stable even during long shifts and multiple operations.
The 20,000 RPM spindle is integrated within the motor to limit vibration, noise and power loss at high speed rotation. Cooled oil is injected directly onto the spindle bearing for effective cooling, and the motor and the spindle assembly are jacket-cooled to limit the displacement caused by heat. To achieve greater precision, standard Hwacheon software (HSDC) monitors the spindle for possible thermal displacement and makes necessary adjustment in real time.
In addition, high pressure through the spindle coolant has made a big difference in Avers' ability to tap and drill parts faster.
Sirius UM provides enhanced feed performance using the Z-axis 6-block LM guide. The servo motor is coupled directly to the drive; and while the tensile preload ball screws provide smooth operation, the roller linear guide allows for rapid feed and rigid performance.
Before final finish passes, the machine can, with Hwacheon HFDC (Hwacheon frame displacement control system) software, dynamically compensate for any changes that may have occurred in machine kinematics due to temperature, vibration or changes in the tool itself.
Avers Machine utilizes industry leading technical software for its daily operations. Building virtual solid models allow it to perform a number of enhanced customer services, such as reverse engineering, complex machining, and evaluation of existing assemblies for cost reduction processing. "I take advantage of the latest technological developments, such as high feed cutters, variable pitch end mills, Solidworks and Delcam's Vortex milling paths," Wellman said. "I find that doing so can keep us ahead of the competition."
With 24 employees, Avers serves the packaging, energy, hydraulic industries and government projects and specializes in tight tolerance milling and turning.
For more information contact:
Avers Machine & Mfg Inc.
4625 North Ronald Street
Harwood Heights, IL 60706-4718
708-867-3335
sales@aversmachine.com
www.aversmachine.com
Hwacheon Machinery America
555 Bond St.
Lincolnshire, IL 60069
847-573-0100
info@hwacheon.com
www.hwacheon.com