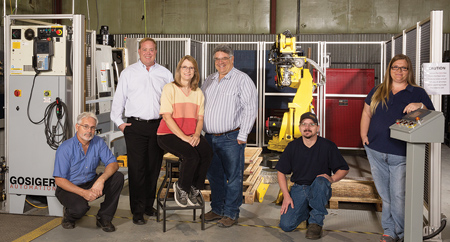
(l-r) Mike Kvia, Shop Foreman; Brad Young, Hartwig, Inc. Sales Engineer; Janice Hecht, Vice President; Scott Hecht, President; Michael Kvia, Programmer/Operator; and Annetta Bills, Office Manager of Wyoming Completion in front of the Gosiger Automation designed robotic work cell.
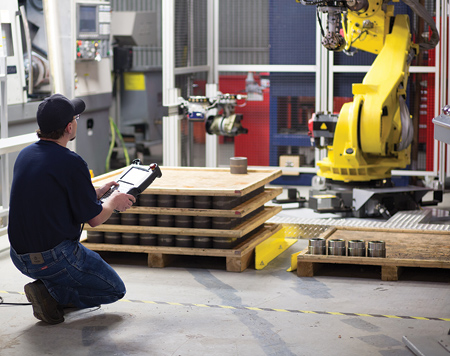
Michael Kvia, Programmer/Operator, calls up a new part program.
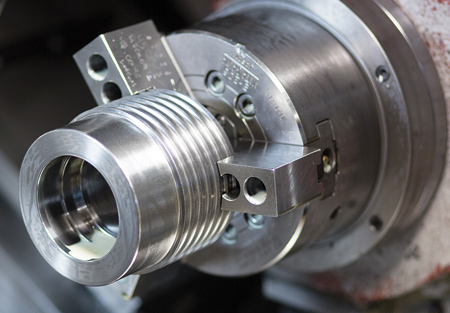
One of a family of parts machined on the Okuma horizontal lathe and ready to be unloaded by the FANUC robot.
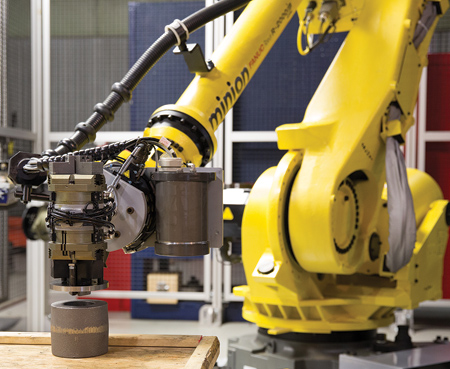
A FANUC R-2000iB/125L robot uses iRVision to identify the proper blank for loading into the automated cell.
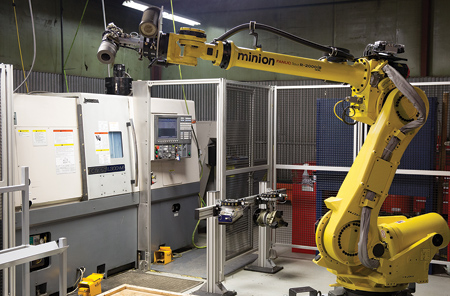
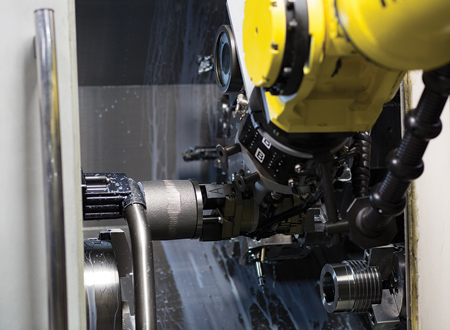
The FANUC robot loads blank into the Okuma Genos L300-MW horizontal lathe for machining.
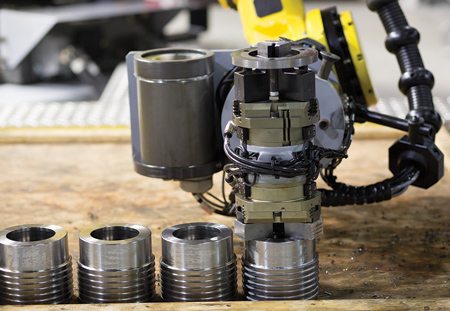
Robot places machined parts on outgoing pallets.
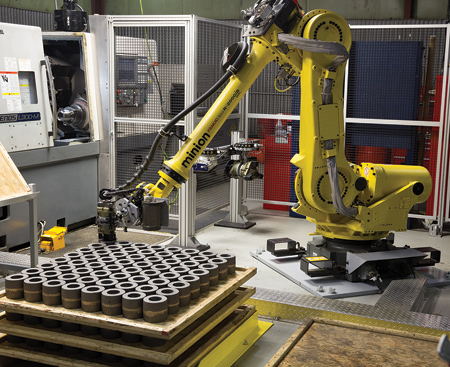
Blanks are placed on simple wooden pallets for loading into the automated work cell. In this way WCT can queue a large quantity of parts for hours of uninterrupted production.
Making down-hole tools for oil drilling means sharing the ups and downs of the oil industry. That is something Scott Hecht of Wyoming Completion Technologies, Inc. (WCT) knows well. "My wife and I started this business in a dairy barn in Powell, WY, in 1998 with one CNC lathe and one mill," he said. Over the years we have stuck with down-hole tool design and manufacturing despite the feast-or-famine nature of oil drilling. That means we have to ramp up production when the market is good without adding overhead."
"When we needed additional capacity to meet customer demands last year, we ran into a problem finding qualified CNC machinists," Hecht continued. "It is one of the downsides of being in a small, rural area. So we decided to automate more of our processes. We were already taking advantage of the automation built into our CNC machine tools, and we added automatic bar feeders in some cases, but we needed to be even more productive and cost-effective. That is when I began looking for another solution."
Hecht consulted with Okuma machine tool distributor Hartwig, Inc. It identified an Okuma Genos L300-MW horizontal lathe as the best-fit machine tool for WCT's requirements and brought in Dayton, Ohio-based Gosiger Automation, the authorized systems integrator for Okuma America, to design and install a robotic automation system around the machine tool.
"We not only needed fast production," Hecht explained, "but also a great deal of flexibility. Our orders fluctuate from a few dozen to thousands of parts, so we needed a system that was easy to set up and change over. For example, we make a series of cones with various dimensions and need to quickly call up each program as needed. The system Gosiger Automation designed for us gives us the speed and flexibility we need."
To achieve the flexibility Hecht required, Gosiger Automation designed a robotic automation system using a FANUC R-2000iB/125L robot equipped with iR Vision that picks a rough part from a wooden pallet, loads it into the lathe, removes the machined part and places it on an outbound pallet. For larger part runs, the operator can stack parts on the pallet using plywood sheets to separate the layers. Using these simple, hardwood pallets is a cost-effective way to queue a large quantity of parts in an automated cell to provide hours of uninterrupted production.
Because the system uses FANUC iR Vision, it requires limited set-up from part to part. Typically all that is required is to call up the new program and change the part gripper fingers, all of which takes just five minutes.
Also in the interest of flexibility, Gosiger Automation equipped the robot with a Schunk end of arm tool system that automatically selects the correct hand for the program chosen. There is a hand for small parts, another for large parts and a vacuum-equipped hand for transferring the plywood separation layers from inbound to outbound pallets.
According to Hecht, "When the oil business picks up again we plan to add a second lathe to the cell, which we can do because Gosiger designed the system to make it easy to expand."
When the time comes to add a second machine, the same robot will service both lathes, with each lathe operating from its own set of pallets. The robot will use its automatic tool change capability to service the two machines alternately, even when making different parts. Uptime for the two lathes is critical, so Gosiger Automation designed the guarding and safety system to allow either machine to undergo tool changes, set-up or maintenance without interrupting the other lathe.
"When we started down this path we hoped for a 25% - 30% improvement in productivity," said Hecht. "What we have is a 200% 500% improvement, depending on the parts being run. It used to take us two to four weeks, using two shifts, to fill some parts orders. Today we produce those same parts in just three days. It is really amazing how the cell just keeps cranking out parts. The only downside is that we really had to step up our machine maintenance, such as keeping the coolant level up, since the machine runs constantly. I am not complaining, though. It is a good problem to have."
"Making this commitment was a big step for a 15-person company like ours, but our attitude was that we could not afford not to do it," continued Hecht. "Fortunately, the Gosiger Automation people were good to work with and made it look easy. I see more automated cells in our future. It is a great way to level out some of the oil industry's ups and downs."
For more information contact:
Scott Hecht, President
Wyoming Completion Technologies
1110 Road 9
P.O. Box 46
Powell, Wyoming 82435
307-754-5429
hechts@directairnet.com
wct@directairnet.com
Brad Young
Hartwig, Inc.
8599 Prairie Trail Drive, Suite 400
Englewood, CO 80112
303-373-9450
brad.young@hartwiginc.com
www.hartwiginc.com
Mark Eddy
Gosiger Automation
108 McDonough Street
Dayton, Ohio 45402
877-288-1538
mark.eddy@gosiger.com
www.gosiger.com