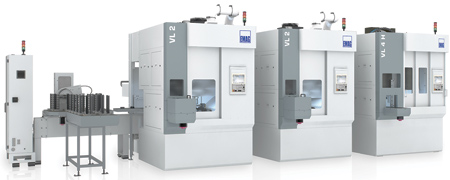
EMAG's modular machines are oriented toward productivity, reliability and cost optimization.
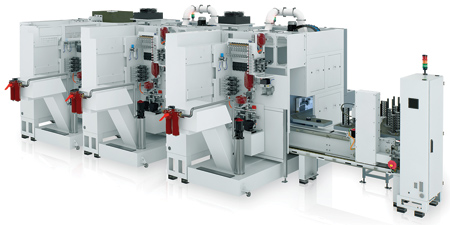
In the TrackMotion automation system, a TransLift unit runs through the machines on a rail system or "track."
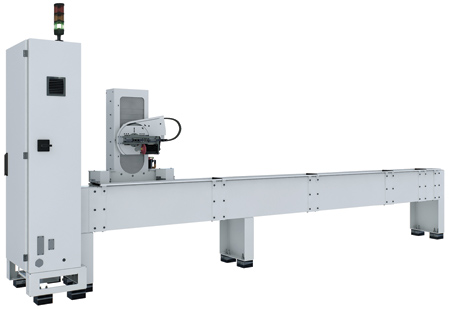
TrackMotion is a modular automation system that is compatible with EMAG's modular machines.
The TrackMotion automation system from EMAG is designed to add enhanced flexibility, modularity and productivity to EMAG's modular machines.
The TransLift, a lift and turnover carriage with programmable electric gripper, races back and forth on a rail. The TransLift covers 160 yards (150 m) in a minute, rapidly conveying the parts between the machines and the part storage facility. The system is designed to put the focus on the individual part.
The TrackMotion automation system consists of just two components, the rail system or "track" that gives it its name, and the lifting and rotating TransLift unit that moves along that track. The TransLift is also what makes this system so flexible since it not only transports the part, but can rotate it as well and is equipped with a Z-axis that permits lifting up to 25.5" (650 mm). This allows the use of stackers for infeed and outfeed, or the deployment of measuring and marking stations at different heights along the track. The track itself is positioned at the rear of the machines, right behind the machining area. To make room for it, the modular machines' energy container has been offset from the rest of the machine body. The resulting "tunnel" behind the machines now permits speedy transportation of parts on the track. This close arrangement of automation system and machine makes it possible to construct manufacturing systems in very tight spaces.
The rail system is assembled from four different tracks with lengths of 94.5", 47", 23.5" and 12" (2,400, 1,200, 600 and 300 mm). Standardized end pieces are fitted at the start and end, containing the electric motors for the horizontal movement of the TransLift. The TransLift itself is offered in two different versions to cater to the range of workpieces processed by the modular machines. The electric gripper can be easily programmed to adapt it to the diameter of the specific workpiece.
Due to matched interfaces, set-up of the entire system is easy and can be carried out centrally from the machine control unit. For instance, the TransLift receives the information about the transported workpiece (such as its diameter) directly from the machine control and is programmed accordingly. The part determines the size and number of the machines and the technologies required, and the TrackMotion automation system is then simply adapted to the length of the manufacturing system and the diameter of the part.
A complete manufacturing system with TrackMotion consists of three coordinated units: the modular machines, the TrackMotion automation system and the infeed and outfeed conveyors. These conveyors, which act as storage units for the parts, can be laid out flat (for large workpieces) or in a 3-D structure as "stackers" for smaller workpieces. The latter option, in particular, offers enhanced performance in a small space, allowing several hundred workpieces to be stored ready for processing. The machines themselves are usually equipped with an L-shuttle automation component, which transports the parts to and from the pick-up station. With only a few workpieces on the move at any given time in the entire system, the status of every single workpiece can be ascertained on demand. This simplifies quality management, as parts with deviating values are easy to identify.
For more information contact:
Peter Loetzner
EMAG LLC
38800 Grand River Ave.
Farmington Hills, MI 48335
248-477-7440
info@usa.emag.com
www.emag.com
Southwest
AR
David Fitzgerald
EMAG LLC
Charlotte, NC
248-595-1117
dfitzgerald@emag.com
www.emag.com
NM
Peter Loetzner
EMAG LLC
38800 Grand River Ave.
Farmington Hills, MI 48335
248-442-6590
info@usa.emag.com
www.emag.com
LA, OK, TX
Ric Lorilla
EMAG LLC
Houston, TX
248-595-1530
rlorilla@emag.com
www.emag.com
Southeast
AL, FL, GA, MS, NC, SC, TN, VA
David Fitzgerald
EMAG LLC
Charlotte, NC
248-595-1117
dfitzgerald@emag.com
www.emag.com
Northeast
NY, PA
James Petiprin
EMAG LLC
38800 Grand River Ave.
Farmington Hills, MI 48335
248-910-8413
jpetiprin@emag.com
www.emag.com
CT, DE, MA, MD, ME, NH, NJ, RI, VT
Jonathan Chomicz
EMAG LLC
Hartford, CT
248-497-8526
jchomicz@emag.com
www.emag.com
WV
David Fitzgerald
EMAG LLC
Charlotte, NC
248-595-1117
dfitzgerald@emag.com
www.emag.com
Midwest
MI, OH
James Petiprin
EMAG LLC
38800 Grand River Ave.
Farmington Hills, MI 48335
248-910-8413
jpetiprin@emag.com
www.emag.com
IL, IN, WI
Tod Petrik
EMAG LLC
Chicago, IL
248-470-2646
tpetrik@emag.com
www.emag.com
IA, KS, MN, MO, NE, ND, SD
Bill Konetski
EMAG LLC
Minneapolis, MN
612-804-0857
bkonetski@emag.com
www.emag.com
KY
David Fitzgerald
EMAG LLC
Charlotte, NC
248-595-1117
dfitzgerald@emag.com
www.emag.com
West
AZ, CA, CO, ID, MT, NV, OR, UT, WA, WY
Peter Loetzner
EMAG LLC
38800 Grand River Ave.
Farmington Hills, MI 48335
248-442-6590
info@usa.emag.com
www.emag.com