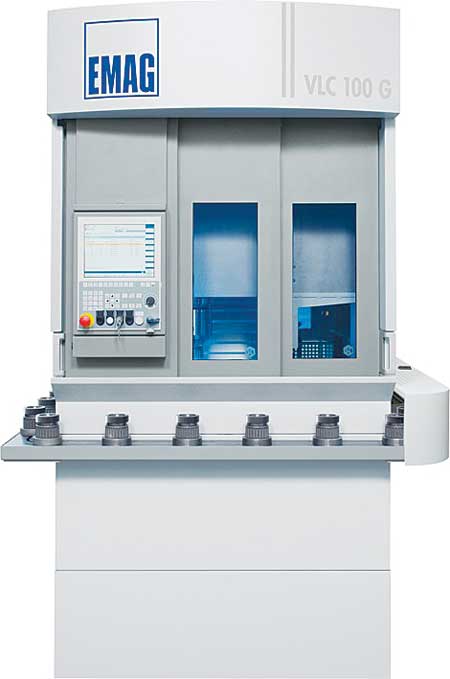
VLC 100 G Vertical Pick-up Grinder
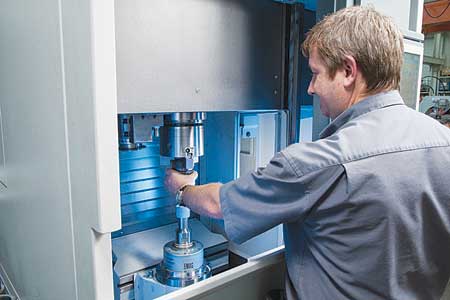
Generously designed maintenance and service doors make the machine easy to access.
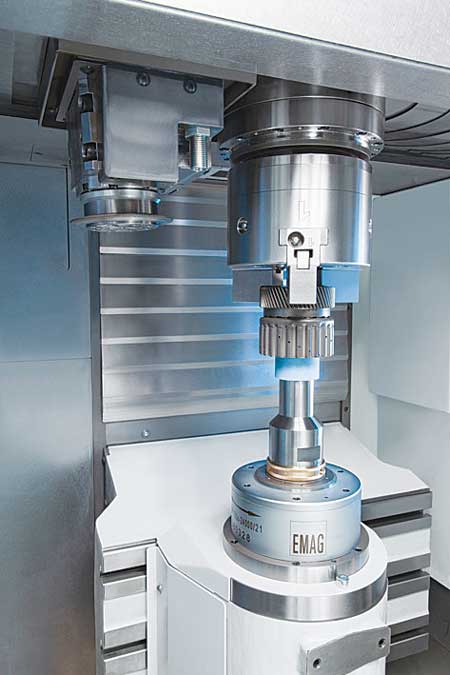
The VLC 100 G is equipped with three axes (XZC). The machine uses its overhead pick-up spindle to load itself. The machining area features one or two grinding spindles for internal and/or external work.
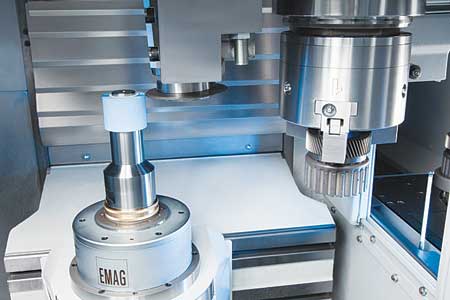
The dressing unit with diamond roll.

The workpieces are mounted on pallets and taken into the VLC 100 G by the conveyor belt. The pick-up spindle then further automates the whole loading and unloading process.
For today's automobile manufacturers, even the smallest components with complex geometries must be produced with increasing levels of precision. The VLC 100 G Vertical Grinding Center from EMAG has been designed for efficient, error-free machining processes for the production of small chucked components with a maximum diameter of 100 mm.
"Small chucked components are typically produced in large quantities," said an EMAG spokesperson. "The demand for components, such as gearwheels, planetary gears, chain gears and flanged components for cars, for instance, have necessary quantities that typically go into the millions; short cycle times in the production of these components have become mandatory. For instance, the internal contour of a gearwheel must be ground in the shortest possible time and the machine's workholding unit must be loaded with a new workpiece just as quickly. In many production environments, this represents a critical moment, because the idle time is commonly a decisive factor in establishing the economic viability of the whole process."
The VLC 100 G utilizes its onboard pick-up system to load itself. While one workpiece is being machined, the operator - or the automation system - is putting the raw parts on the conveyor belt. This reduces idle time and increases output rates. Another benefit is the vertical machining concept. The design is intended to ensure that the grinding sludge falls to the bottom of the machine unhindered, where it is then transported out of the machine.
Measuring processes can also be integrated into the machine, making quality control an integral part of the whole process. The measuring probe is located between the machining area and pick-up station, where it is protected from contamination.
An important feature of the VLC 100 G is that it offers the possibility to use two grinding spindles, which can be used to perform different grinding operations or to handle both rough- and finish-grinding work. The first wheel performs the rough job of removing excess material from the raw part at high feedrates (the CBN wheel is specially designed to absorb the necessary forces), while the second wheel (with different specifications) takes over the finishing work. "For the removal of large amounts, two wheels offer a shorter cycle time than one, with the first wheel designed to do the rough grinding and the second one in charge of finish grinding work," said Dr. Guido Hegener, Managing Director of EMAG Salach Maschinenfabrik GmbH in Germany.
The machine can be integrated into existing production. "Programming the workpieces with our new EMAG NAVIGATOR software is simple and intuitive, saving valuable setup time. For many production environments, this is an advantage that should not be underrated," said Dr. Hegener. The stand-alone machine occupies about 4.5 square meters (48 sq. ft.), further allowing ease of integration.
For more information contact:
Peter Loetzner
EMAG LLC
38800 Grand River Avenue
Farmington Hills, MI 48335
248-477-7440
info@usa.emag.com
www.emag.com
Southwest
AR
Ken Pope
EMAG LLC
Mobile: 256-642-6842
615-308-7170
kpope@emag.com
NM
EMAG LLC
248-477-7440
info@usa.emag.com
TX, OK, LA
David Harris
OCTG Sales Manager
EMAG LLC
248-755-9167
dharris@emag.com
Southeast
MS, TN, AL, GA, FL, SC, NC, VA
Ken Pope
EMAG LLC
Mobile: 256-642-6842
615-308-7170
kpope@emag.com
Northeast
PA, NY
Kirk Stewart
EMAG LLC
Mobile: 248-996-4703
248-442-5960
kstewart@emag.com
ME, NH, VT, MA, RI,
CT, NJ, DE, MD, WV
EMAG LLC
248-477-7440
info@usa.emag.com
Midwest
IN, OH
Kirk Stewart
EMAG LLC
Mobile: 248-996-4703
248-442-5960
kstewart@emag.com
ND, SD, NE, KS, MN, IA, MO, WI, IL
Bill Konetski
EMAG LLC
Mobile: 612-804-0857
bkonetski@emag.com
KY
Ken Pope
EMAG LLC
Mobile: 256-642-6842
615-308-7170
kpope@emag.com
MI
Rob Nash
EMAG LLC
Mobile: 248-755-4290
248-442-6569
rnash@emag.com
West
MT, WY, CO, ID, UT,
AZ, WA, OR, NV, CA
EMAG LLC
248-477-7440
info@usa.emag.com