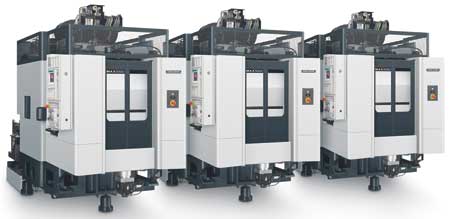
MAX3000 for pump and valve housings.
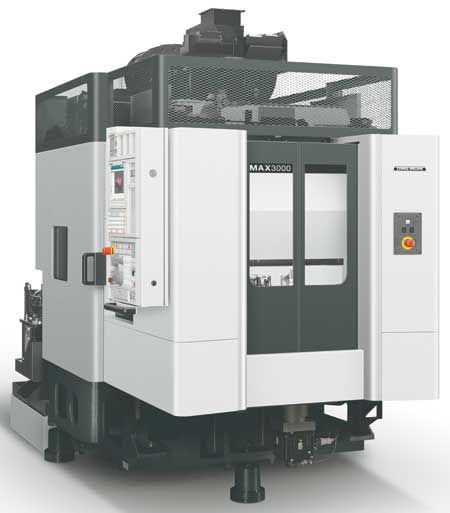
MAX3000 for pump and valve housings.
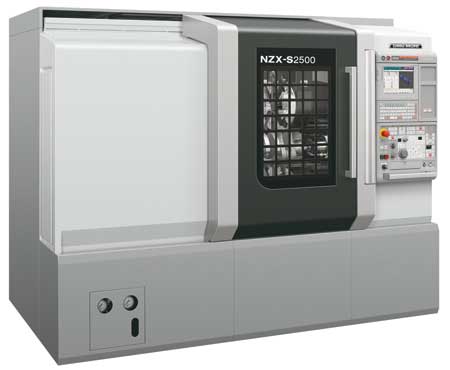
NZX-S2500 for crankshaft and camshaft manufacturing.
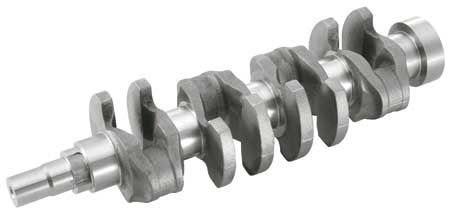
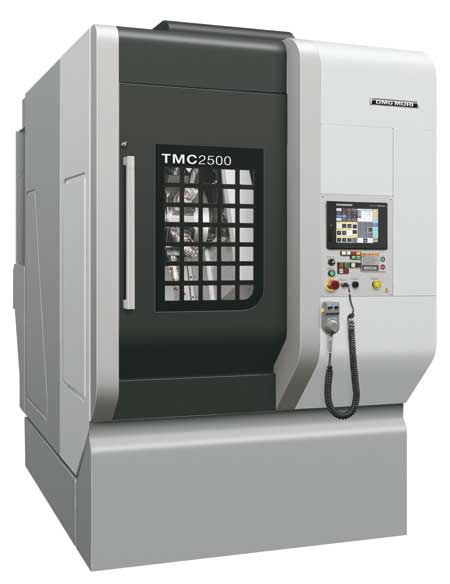
TMC2500 for machining connecting rods.
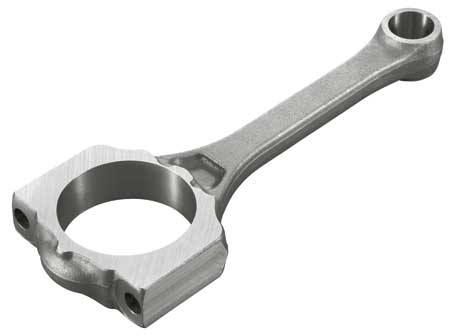
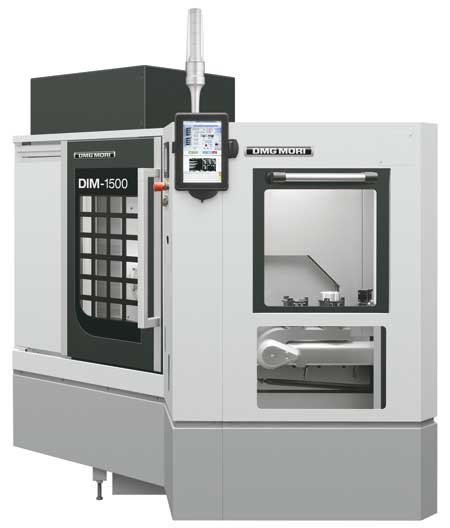
DIM1500 for automotive components up to a 100 mm cube.
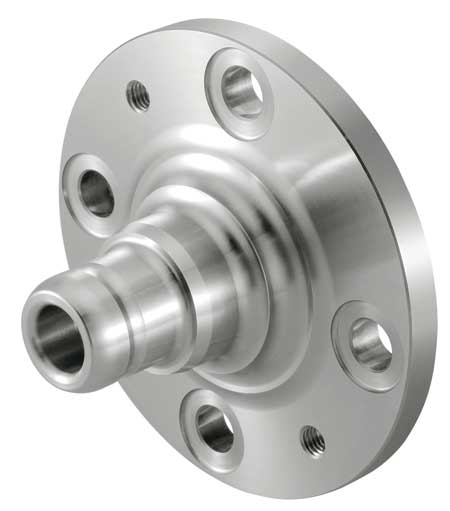
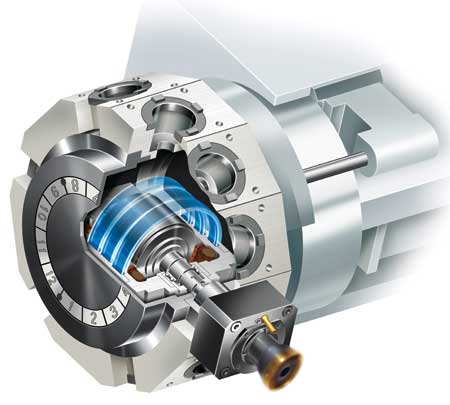
The BMT turret uses proven components in the development of automotive-specific customer solutions.
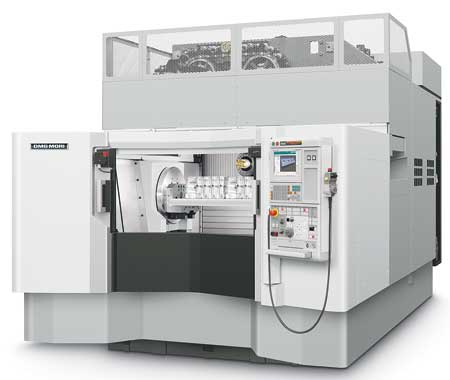
The compact i80L horizontal machining center from DMG MORI is specifically targeted towards manufacturers of cylinder heads and crank cases.
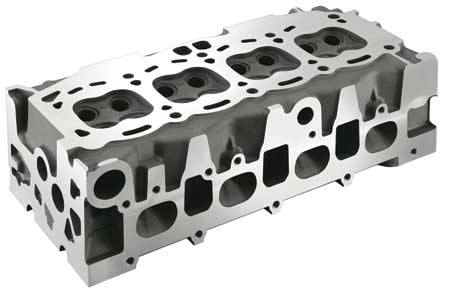
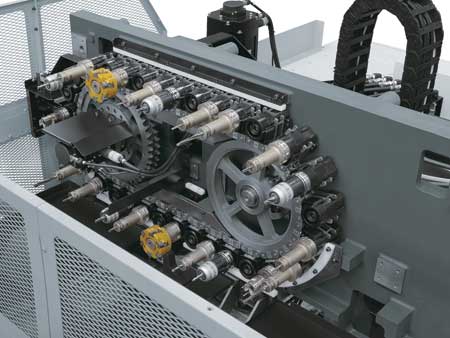
The i80L's tool magazine is mounted above the machine to save space and stores up to 30 tools.
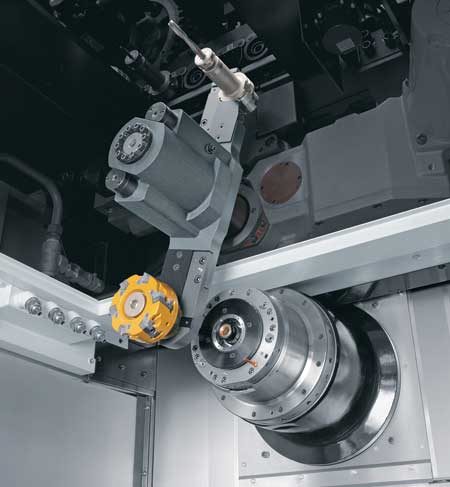
The tool changer's double gripper helps ensure minimal chip-to-chip times of 4.4 seconds for the i80L/50 and 3.3 seconds for the i80L/40.
In spite of differences in detail, many workpieces which require machining in the automobile industry are similar - at least as far as dimensions and manufacturing requirements are concerned. In the context of the trend towards standardization and configurability of machining systems in the automobile industry, this opens up prospects for metal cutting machine tools.
"MORI SEIKI has been successful for many decades as a manufacturer of specialized manufacturing systems for the automobile industry and its suppliers. This tradition is now to be expanded and accelerated thanks to the combined expertise available within the DMG MORI concern," said Ralf Riedemann, Managing Director of MORI SEIKI Europe AG, President of MORI SEIKI GmbH and General Manager of the European Engineering Department.
According to Riedemann, the key to success in specialized manufacturing solutions lies mainly in the right customer orientation. He explains, "As a supplier of high-tech machines, we today have much greater responsibility for optimizing customers' processes. For this reason, every project is preceded by a detailed analysis of the components to be manufactured. Only then is the best solution for the specific application determined."
In most cases, an economic solution, which either fulfils the requirements as a stand-alone machine or as an automated manufacturing system, is found based on the standard program.
Even if the standard range is unable to meet the requirements, as Ralf Riedemann underlines: "DMG MORI can produce a specialized machine from proven components and modules with manageable design effort so cost effectively that it offers the user the kind of added value which he would otherwise only be able to achieve by investing in far more expensive special designs."
However, every ambition to specialize has its economic limits, as Riedemann concedes. One of the decisive factors in this context is whether it will be possible to make customer development available to the global market after a certain period. There are some current examples of such machines in DMG MORI's latest product portfolio, which all have one thing in common.
In each case, the work area is designed to suit the envisaged parts to be manufactured. This minimizes the space required, reduces downtime for handling or for automatic loading and unloading, and cuts down on the use of materials and therefore cost. As a result of the work area being reduced to the minimum dimensions necessary, the effects of temperature are also reduced, which makes for higher component accuracies even in tough, continuous operation. Ralf Riedemann adds: "All automotive machines are of course already prepared for the use or integration of automation."
The high-performance range of automotive machines from DMG MORI includes the compact MAX3000 vertical center, which for example, can process valve housings as well as pump housings. The MAX3000 has an SK30 interface and is equipped with a high-speed pallet changer. Its compact design means the machining center requires a footprint of only 4.6 m2, in spite of the pallet changer. The clamping surface of 600 mm x 300 mm is suited for machining small automotive parts. Rotary tables can also be used for added flexibility.
The MAX3000 achieves a traverse speed of 60 m/min in all axes. In addition, high acceleration rates reduce machining times - particularly when frequent changeovers between feed and rapid traverse are required, such as when machining several components in one set-up. The fast pallet changeover time of two seconds, or just less than three seconds chip-to-chip, also aids in productivity.
The SK30 interface machine center offers rigidity with a speed of up to 15,000 RPM and a spindle bearing inside diameter of 55 mm. This enables a diversity of parts from different materials to be machined. The machine is therefore equally suited to high-speed milling of aluminum, heavy-duty cutting of steel and the machining of magnesium, iron, cast iron or stainless steel.
The MAX3000 range is supplemented by various options. These include chip disposal, coolant systems and measuring probes. Integral solutions for automation or machine linking are also available. In all cases, these are configured or developed individually for the particular project by DMG MORI Systems.
A second example from the DMG MORI range are the compact NZX-S2500 twin turret lathes, which are used, among other things, for the complete machining of crankshafts and camshafts. "The NZX-S2500 is a prime example of the company's development capabilities in the automobile field. Traverse distances, spindle power and feed rate in particular have been explicitly matched to the requirements. The machine also features a symmetrical structure (in relation to the spindle center), which reduces the effects of temperature on the machining results and increases precision," said a company spokesperson.
Further design attributes of the NZX-S2500 are the vertical machine bed for chip disposal, access to the working area and tool magazine for easy manual set-up or as a basis for efficient automation solutions, and the use of roller guides on all axes for stable process conditions and reliability. In addition, axis traverse speeds of up to 36 m/min and indexing times for the two 8-station turrets of 0.2 seconds enhance productivity.
The TMC2500 may also implement a milling application. With this compact machining center, an 8-station turret with BMT technology with directly driven tools acts as a milling spindle above the swiveling table. This allows for the machining of, among other things, connecting rods.
As a milling facility, the BMT turret, which originates from the turning sector, achieves chip-to-chip times of 1.5 seconds, while the short travel distances in conjunction with the high-speed axes offer reduced positioning times. The TMC2500 lends itself to automation. "The range of applications extends well beyond the automotive sector and, in principle, is limited only by the traverse distances. In all cases, slideways on all axes provide process stability, guarantee precision and ensure long tool service life," said the spokesperson.
Another product in the portfolio is the DIM1500 turn-mill center for small components that fall within a 100 mm cube. Of note is the position of the spindle and 12-station turret with BMT technology, which are arranged horizontally at an angle of 45° to one another. "This saves installation space and reduces positioning movements and, in addition, results in optimum force conditions for demanding turning and milling operations," said the spokesperson.
The workpiece spindle operates at a speed of up to 6,000 RPM and a torque of up to 200 Nm, and can be fitted with a tool changer if the machine is to be automated. The BMT turret's direct drive accelerates tools to a speed of 10,000 RPM and also reduces the chip-to-chip time to 1.47 seconds due to high-speed indexing.
In regards to both the TMC2500 and the DIM1500, Ralf Riedemann explains: "In many metal cutting processes in the automotive industry and in other sectors, and particularly when machining aluminum, contamination in the vicinity of the tool changer repeatedly causes problems. These difficulties are not encountered owing to the design of the BMT turret, and this increases the reliability in tough manufacturing operations."
The i80L, aimed at the automotive sector, is an ultra-compact horizontal machining center for the productive manufacture of engine components in large batches. The compactness has also been achieved by, among other things, positioning the tool magazine in the top area of the machine. Furthermore, the basic configuration of the machine has been designed without a pallet changing system. This means that the i80L only requires a footprint of 2,550 x 4,685 mm.
The machine concept provides all options for manual set-up as well as for customized automation solutions, for example, by means of gantry loaders or transfer line systems. Furthermore, the design of the i80L means that it can be configured to form a highly automated production line, for example for cylinder heads or engine blocks, using additional machines and machining units.
Another feature of the i80L is the size of the work area. XYZ axis travels are 800 x 550 x 850 mm. "This means that even large 6-cylinder engine blocks can be machined without difficulty. Alternatively, customers can use the available space to position two workpieces in the work area at the same time and machine them in parallel. This reduces the number of machines required and consequently minimizes the investment," said the spokesperson.
The i80L features rapid traverse speeds of 60 m/min in all axes and the various high performance spindles. The machine is available in two different designs with an HSK A100 spindle and speeds of up to 8,000 RPM (for the i80L/50 version) or with a 12,000 RPM HSK-A63 spindle for the i80L/40 version. The positioning time of the swivel table with its double-sided DirectDrive technology A-axis is another feature and the whole process, including clamping and releasing, takes 1.5 seconds for both versions.
The minimal chip-to-chip times of 4.4 seconds for the i80L/50 and 3.3 seconds for the i80L/40 also have a positive impact on productivity. The i80L/50's tool magazine provides capacity for 20 tools of up to 110 mm diameter when fully loaded or up to 280 mm if adjacent pockets are left free. The maximum tool length here is 550 mm, and the maximum weight is up to 30 kg. For the i80L/40, the magazine has a capacity of up to 30 tools and the maximum tool diameter is 140 mm. When fully equipped, it is 70 mm. The maximum tool length is specified as 390 mm in the data sheet, and the maximum weight is 12 kg.
For manual set-up, the table can be moved in the Z-axis, which improves accessibility to the workpiece when manual intervention in the work area is required. The operator is therefore only 500 mm away from the set-up position. The low height of the machine, which also reduces the loading height and consequently the loading time for possible gantry loader automation, is also oriented towards the requirements of automation.
For more information contact:
DMG MORI USA
2400 Huntington Blvd.
Hoffman Estates, IL 60192
847-593-5400
www.dmgmori.com
Southwest
DMG MORI - Dallas
9001 Currency Street #200
Irving, TX 75063
972-929-8321
www.dmgmori.com
TX, LA
DMG MORI Ellison Technologies - Dallas
9001 Currency Street #200
Irving, TX 75063
972-812-5500
www.ellisontechnologies.com
DMG MORI Ellison Technologies - Houston
3403 N. Sam Houston Pkwy. West #100
Houston, TX 77086
713-365-9500
www.ellisontechnologies.com
OK
DMG MORI - Tulsa
7633 E 63rd Place, Suite 300
Tulsa, OK 74133
918-932-2893
www.dmgmori.com
Southeast
DMG MORI - Charlotte
4345 Morris Park Drive
Charlotte, NC 28227
704-940-3380
www.dmgmori.com
VA, NC, SC
DMG MORI Ellison Technologies - Charlotte
4345 Morris Park Drive
Charlotte, NC 28227
704-545-7362
www.ellisontechnologies.com
S. AL, GA, MS, TN
DMG MORI Ellison Technologies - Nashville
7118 Crossroads Blvd.
Brentwood, TN 37027
615-661-6800
www.ellisontechnologies.com
FL
DMG MORI - Clearwater
4585 140th Ave. North, Suite H1008
Clearwater, FL 33762
727-530-1490
www.dmgmori.com
Northeast
DMG MORI - Newark
1160 Parsippany Blvd, Suite 103
Parsippany, NJ 07054
973-257-9620
www.dmgmori.com
DMG MORI Tyler Machine Tool
111 Ledge Rd.
Seabrook, NH 03874
603-474-7730
www.dmgmori.com
DMG MORI Tyler Machine Tool
68 Nutmeg Road South
South Windsor, CT 06074
860-528-4010
www.dmgmori.com
Boldt Machinery, Inc.
4803 Pittsburgh Ave.
Erie, PA 16509
814-833-9836
www.boldtmachinery.com
Boldt Machinery, Inc.
104 Boss Rd.
Mattydale, NY 13211
315-463-5754
www.boldtmachinery.com
MD, DE
DMG MORI - Charlotte
4345 Morris Park Drive
Charlotte, NC 28227
704-940-3380
www.dmgmori.com
DMG MORI Ellison Technologies - Charlotte
4345 Morris Park Drive
Charlotte, NC 28227
704-545-7362
www.ellisontechnologies.com
Midwest
DMG MORI - Chicago
2400 Huntington Boulevard
Hoffman Estates, IL 60192
847-593-5400
www.dmgmori.com
DMG MORI Ellison Technologies - Chicago
4630 Weaver Parkway
Warrenville, IL 60555
630-393-8900
www.ellisontechnologies.com
DMG MORI - Cincinnati
5333 Mulhauser Road
Hamilton, OH 45011
513-874-2736
www.dmgmori.com
DMG MORI Ellison Technologies - Cincinnati
5333 Mulhauser Road
Hamilton, OH 45011
513-874-2736
www.ellisontechnologies.com
DMG MORI Ellison Technologies - Cleveland
6955 Treeline Drive
Brecksville, OH 44141
440-546-1920
www.ellisontechnologies.com
DMG MORI Ellison Technologies - Davenport
145 West 76th Street
Davenport, IA 52806
563-388-0800
www.ellisontechnologies.com
DMG MORI Ellison Technologies - St. Louis
16 MB Corporate Park Ct.
St. Charles, MO 63301
636-946-7077
www.ellisontechnologies.com
DMG MORI - Detroit
29050 Cabot Drive
Novi, MI 48377
248-324-1928
www.dmgmori.com
DMG MORI Ellison Technologies - Detroit
29050 Cabot Drive
Novi, MI 48377
248-324-1928
www.ellisontechnologies.com
DMG MORI Ellison Technologies - Grand Rapids
1550 Gezon Parkway SW, Suite B
Wyoming, MI 49509
616-261-8665
www.ellisontechnologies.com
DMG MORI Ellison Technologies - Indianapolis
8930 Bash Road, Suite A
Indianapolis, IN 46256
317-577-3723
www.ellisontechnologies.com
DMG MORI Ellison Technologies - Milwaukee
N27 W23750 Paul Road
Pewaukee, WI 53072
262-523-3400
www.ellisontechnologies.com
DMG MORI Ellison Technologies - Minneapolis
13400 10th Avenue North
Plymouth, MN 55441
763-545-9699
www.ellisontechnologies.com
DMG MORI - Kansas City
7500 College Blvd, 5th Floor
Suites 520/521/522/524
Overland Park, KS 66210
913-871-1373
www.dmgmori.com
DMG MORI - Wichita
3450 N Rock Rd
Building 500, Suite 505
Wichita, KS 67266
316-425-7993
www.dmgmori.com
West
DMG MORI - Los Angeles
5740 Warland Drive
Cypress, CA 90630
562-430-3800
www.dmgmori.com
Southern CA
DMG MORI Ellison Technologies - Los Angeles
9890 Pioneer Blvd.
Santa Fe Springs, CA 90670
562-949-8311
www.ellisontechnologies.com
Northern CA
DMG MORI Ellison Technologies - San Francisco
2607 7th St. Suite C
Berkeley, CA 94710
866-814-7238
www.ellisontechnologies.com
WA, ID, MT
DMG MORI Ellison Technologies - Seattle
19625 62nd Ave. South, Suite A109
Kent, WA 98032
253-872-1661
www.ellisontechnologies.com
OR
DMG MORI Ellison Technologies - Portland
10159 SW Commerce Circle #K
Wilsonville, OR 97070
503-682-3280
www.ellisontechnologies.com
AZ
Ellison Machinery
1610 S. Priest Dr. #101
Tempe, AZ 85281
480-968-5335
www.ellisonaz.com
CO
Triad Machine Tool Co., Inc.
7885 West 48th Avenue
Wheat Ridge, CO 80033
303-424-0268
www.triadmt.com
UT, ID, MT, WY
New West Machine Tool Technologies
7990 South 1530 West
West Jordan, UT 84088
801-561-2001
www.newwestmachine.com