
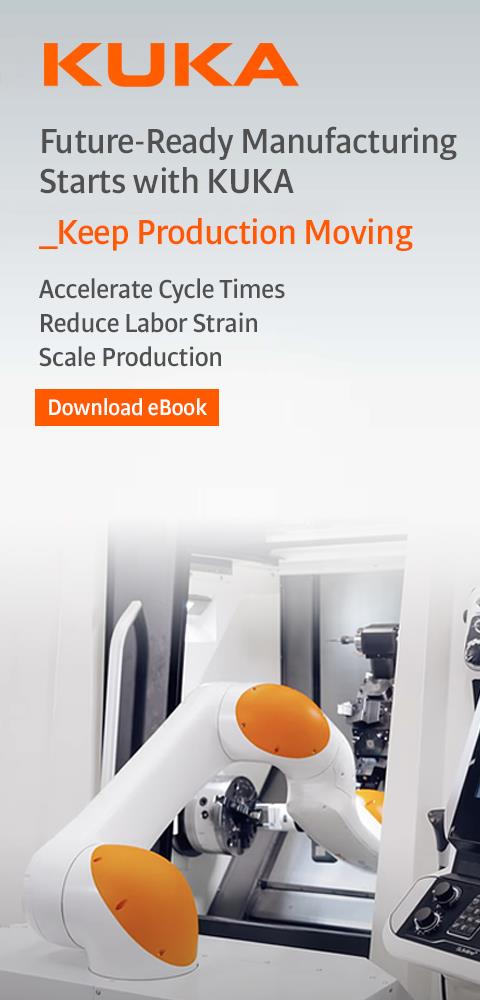
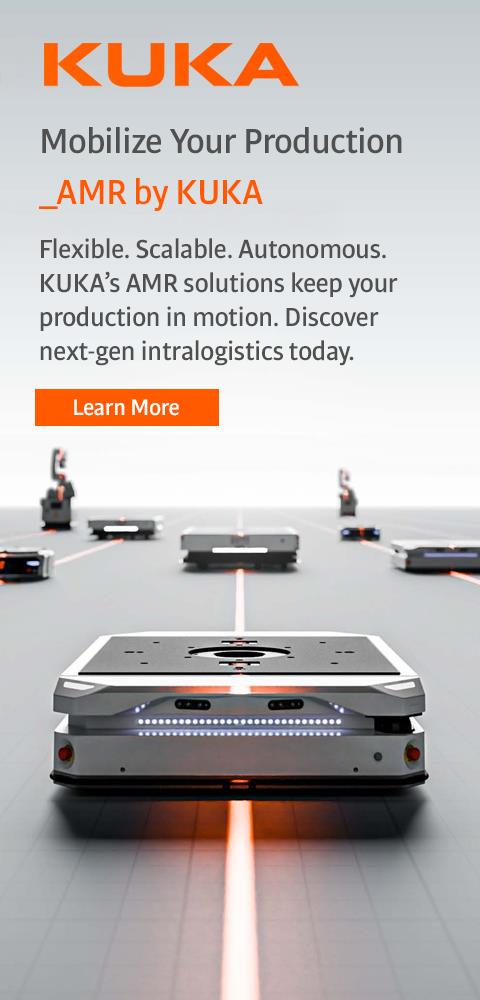
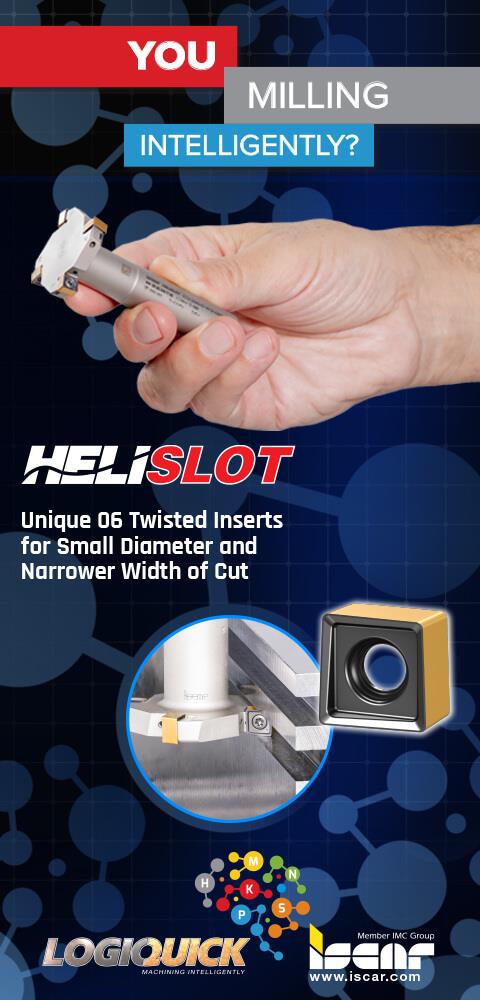
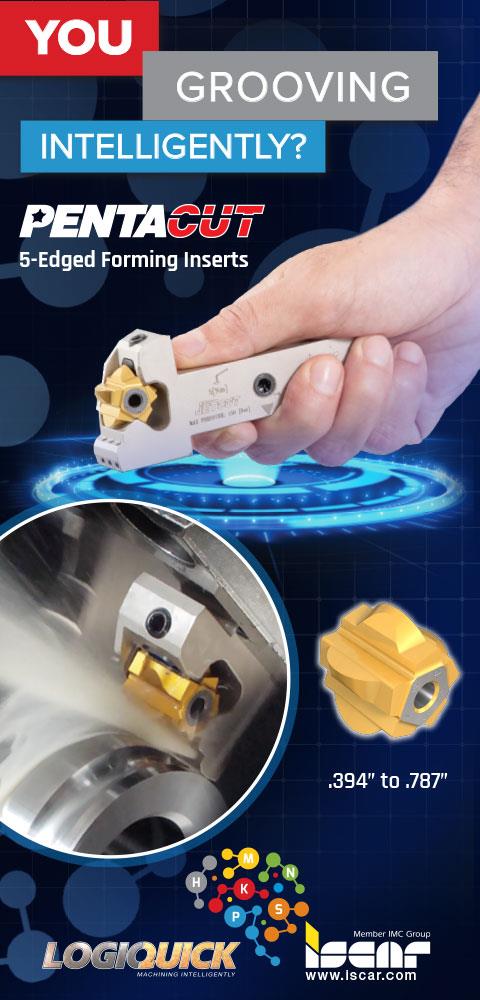
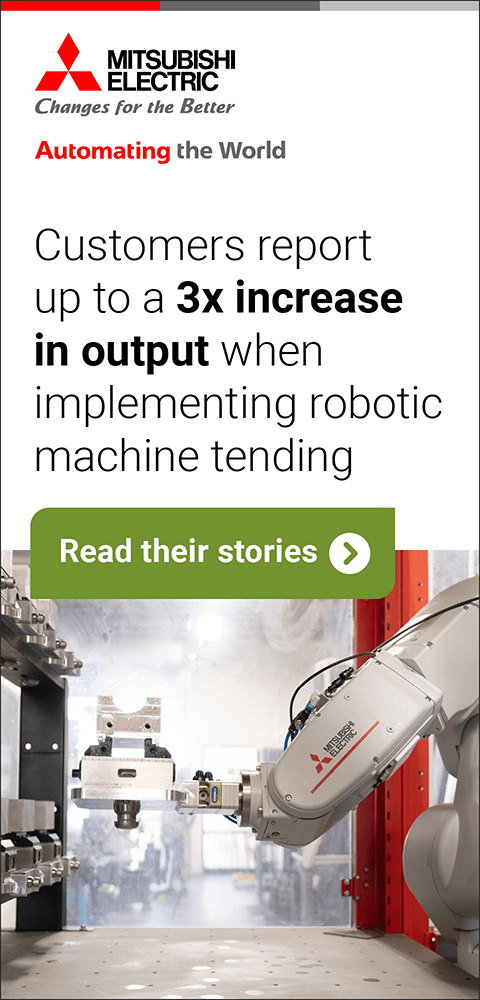
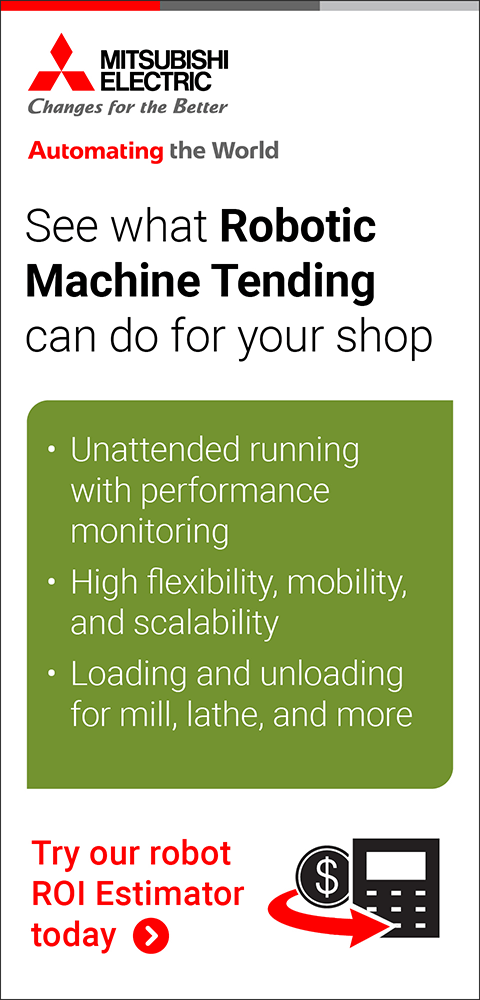




Electrochemical Machining Without Stray Machining Attack
November 1, 2015
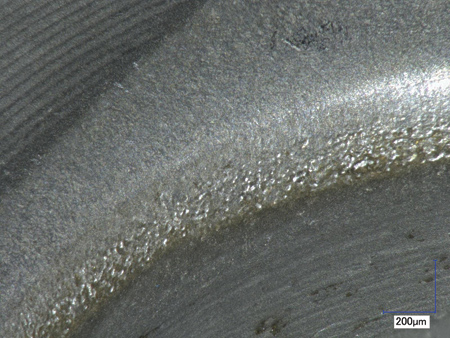
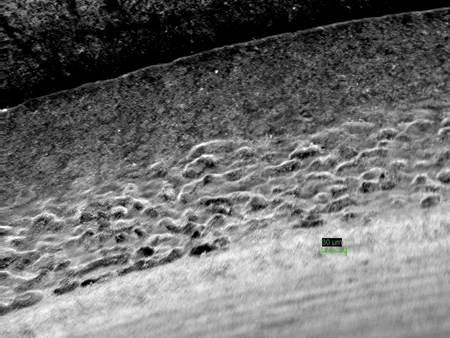
Standard ECM Technology
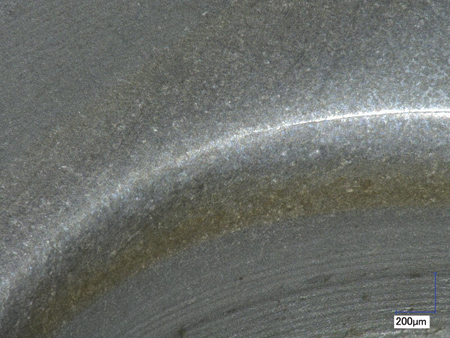
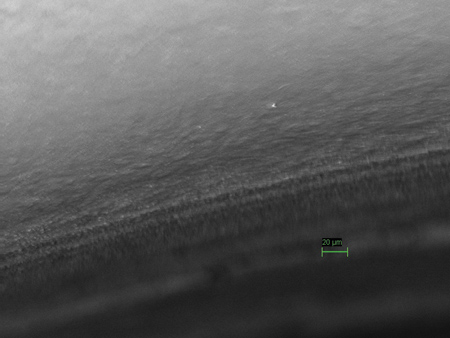
EXTRUDE HONE EVO Technology
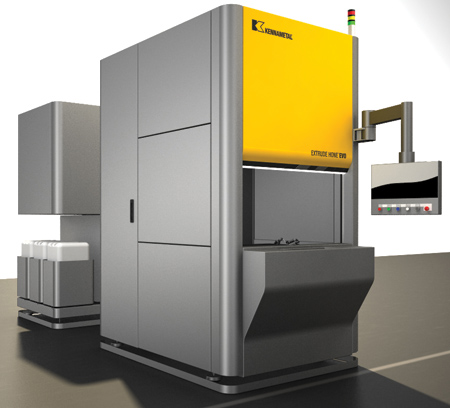
Manufacturers and quality professionals requiring high-precision components such as automotive fuel systems and powertrains are under constant pressure to deliver the utmost quality efficiently. Consequently, Kennametal Precision Surface Solutions is announcing Extrude Hone EVO, featuring proprietary generator technology delivering from 3 kW to 100 kW power depending on machine configuration. "Additionally, EVO delivers another exclusive added value: electrochemical machining without stray machining attack," said Bruno Boutantin, Kennametal Precision Surface Solutions Global Marketing Manager. "Customers will enjoy the highest surface finish quality for improved component performance."
ECM Explained
ECM is used in contouring, radiusing, polishing, deburring and flow tuning applications. Essentially, ECM is a subtractive method that works on the principle of anodic metal dissolution. Each part to be machined requires a cathode (-) for selective material removal on the workpiece (+). The cutting speed is equal to the DC current applied to the part. The lack of contact between the tool (-) and the workpiece (+) is important. An electrolyte solution (NaCl or NaNO3 in water or glycol base) handles charge transfer in the working gap. The resulting electron current releases metal ions from the workpiece. The amount of material removed is defined by Faraday's Law (equivalent to current x cycle time). Using the electrolyte, the removed material is flushed out of the gap as a hydroxide. This must be captured by an adequate filter system to maintain constant electrolyte conditions. There will be a constant gap, resulting in proper tooling and cathode life. The shape of the tool cathode determines the shape of the material removal. ECM's main benefits of this process are:
- Targeted material removal in precise locations
- No mechanical or thermal stress
- Process stability
- High productivity.
EXTRUDE HONE EVO is available in various standard layouts: single or dual cell, or even in multi-cell configurations due to the system's modular design and construction. It is designed to be easy to configure and easy to integrate into modern production lines. For customers looking for specific machining operations, the machine integrates an interface for Dynamic ECM.
EVO provides for online monitoring and control of all relevant parameters. The online feature is also designed to be beneficial in delivering remote process demonstrations.
For more information contact:
Kennametal Inc.
1600 Technology Way
P.O. Box 231
Latrobe, PA 15650
724-539-5000
www.kennametal.com
< back