
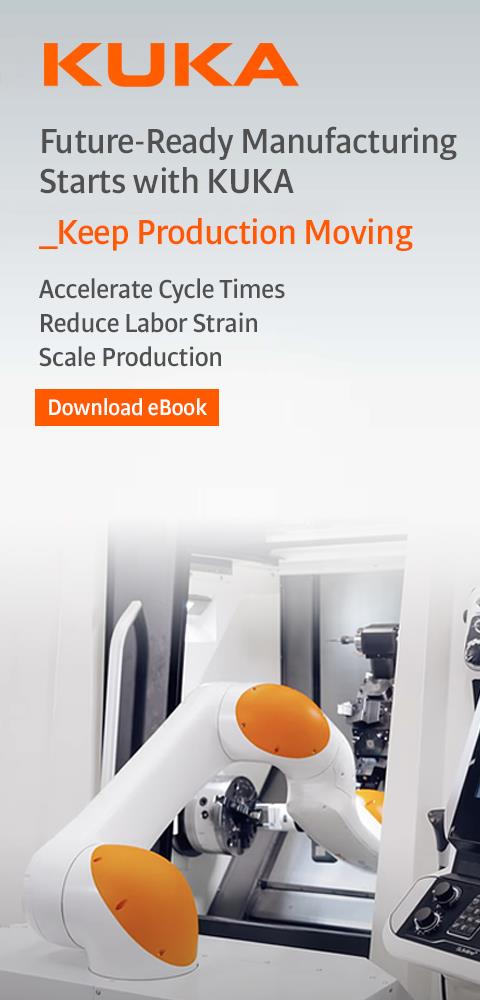
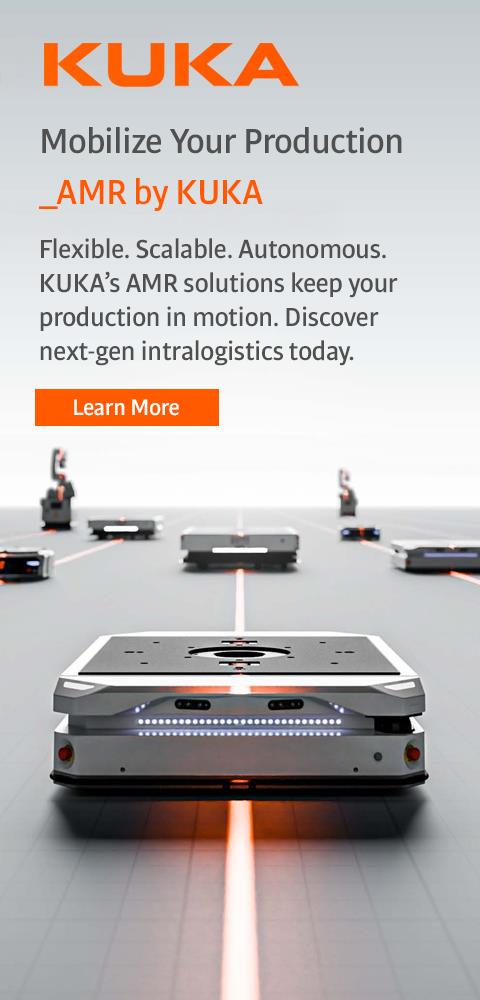
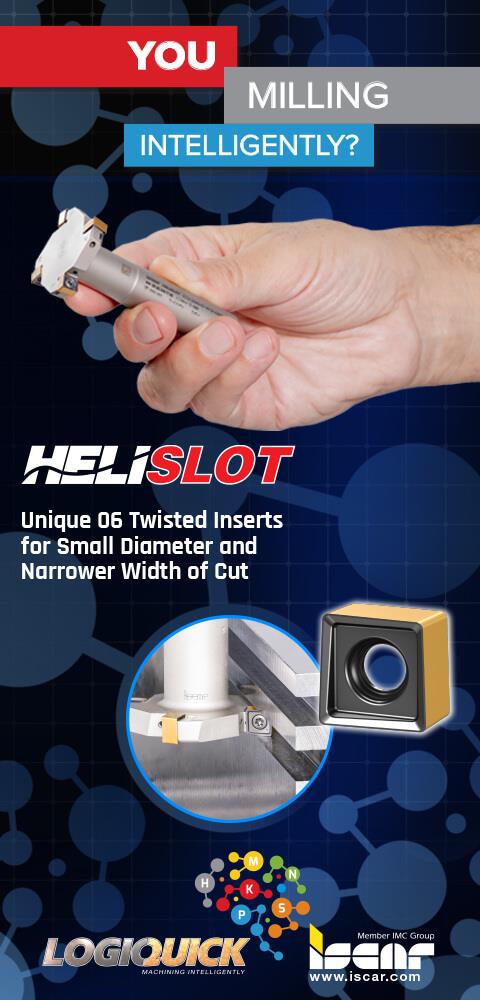
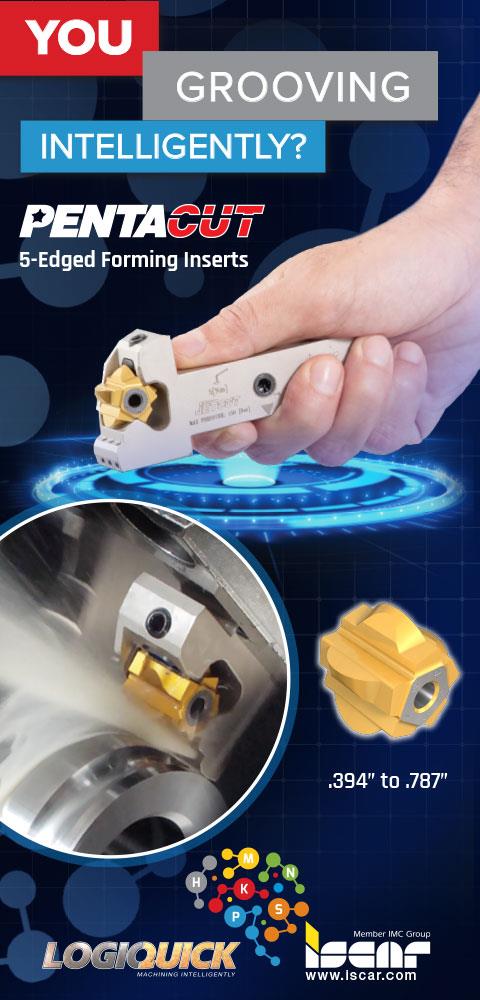
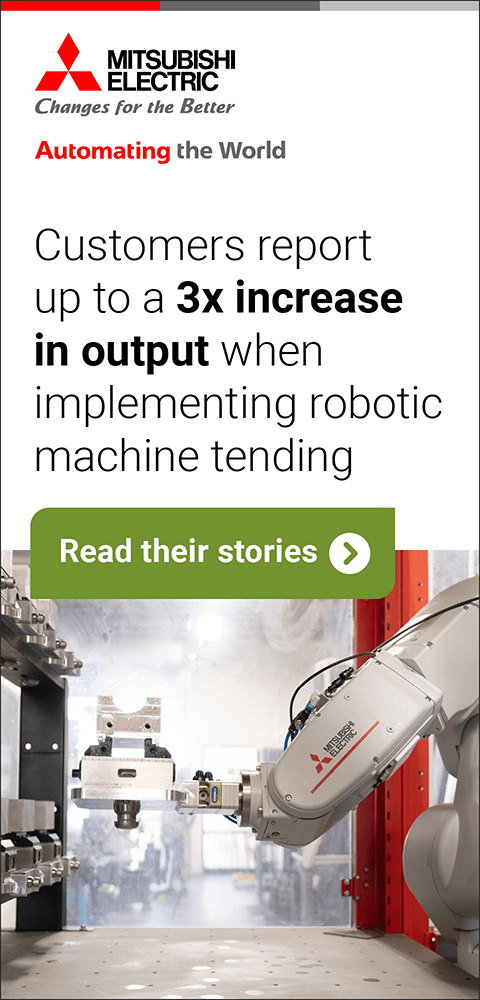
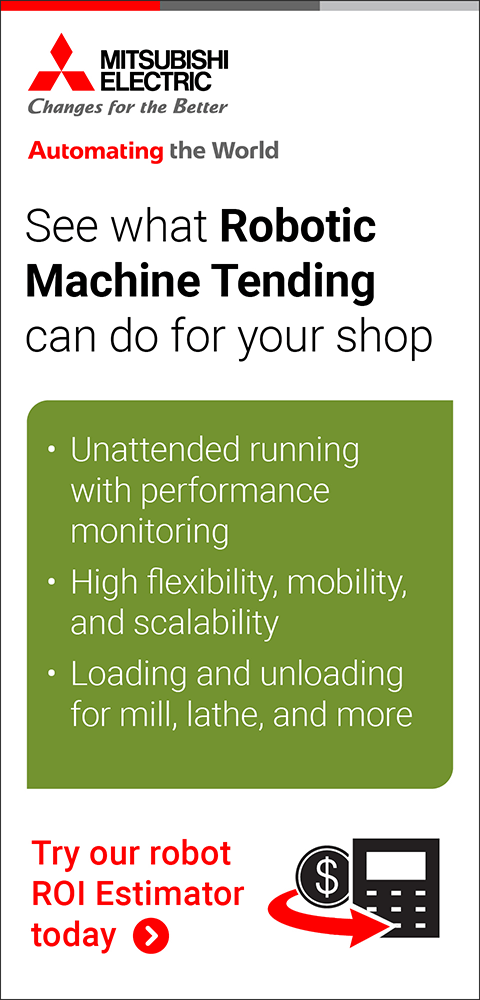




Flap Disc with X3 Technology
November 1, 2015
Weiler Corporation's Tiger X flap disc features a new X3 technology that combines a triple split coat grain anchoring system, dual flap design and engineered abrasive cloth backing with intermixed ceramic alumina and zirconia alumina materials. This combination is designed to create a faster grind rate while increasing life.
"The triple split coat material serves as an advanced grain anchoring system to ensure consistent cut rate throughout the life of the disc without the need to apply more pressure, providing maximum aggression. The resulting decrease in worker fatigue allows for enhanced worker safety and comfort. The ceramic and zirconia alumina material blend allows for higher initial cut rates and consistent grinding, increasing productivity. These benefits, combined with an overall longer life cycle, decrease consumable costs as compared to other flap discs on the market. X3 technology also allows for greater versatility due to the reduced need to switch discs when changing applications," said a company spokesperson.
Tiger X will replace Tiger phenolic-backed flap discs in 4-1/2", 5" (angled style) and 7" sizes.
For more information contact:
Weiler Corporation
One Weiler Dr.
Cresco, PA 18326
800-835-9999 / 570-595-7495
info@weilercorp.com
www.weilercorp.com/tigerx
< back