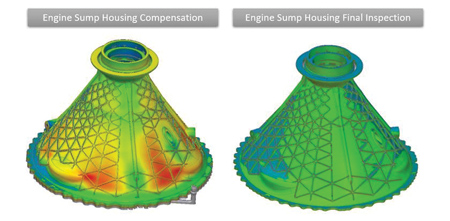
Using simulation-based compensation software reduced deformation by about 60% on the GE Catalyst sump housing.
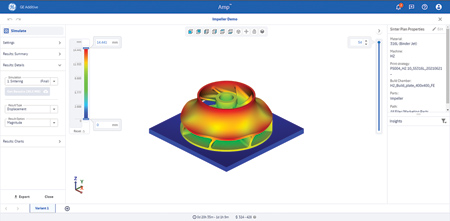
v
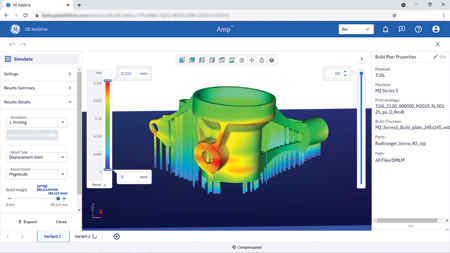
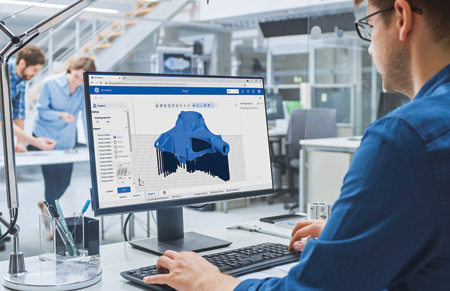
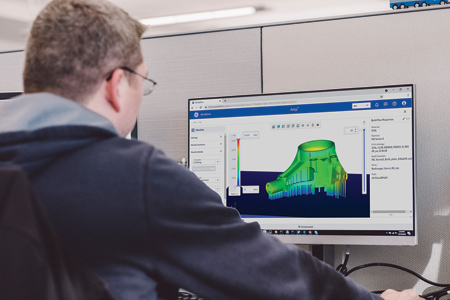
GE Additive offers its Amp Cloud-based process management software platform, and has announced limited release of the first two modules, Print Model and Simulation & Compensation, for Concept Laser M2 machine users, with wider release planned for the second quarter of 2022.
Getting to Production and Industrialization Faster
Developed and designed exclusively for GE Additive machine customers, Amp integrates tools for engineers to manage, process and manufacture metal additive parts on one integrated platform. From development to print production, Amp offers a flexible, streamlined workflow so manufacturers can improve part production and reduce trial and error needed to develop print-ready parts.
Amp breaks down the silos between CAD, build prep, simulation, compensation and inspection data to help improve part production. With centralized data, users can access tools that simulate how the manufacturing process unfolds in real time and see the estimates for cost and time for a part throughout the process. Amp uses a single database that supports seamless data transition between one task and another.
"Calculations for these tasks all depend heavily on the material and the additive machine being used," said a company spokesperson. "To produce an accurate simulation, today the problem faced by users is that they must enter information about the build, ranging from laser power and speed to powder size and distribution. Amp solves this problem by closely tying Amp to GE Additive's own laser printers, initially the Concept Laser M2, then the M Line and Binder Jet solutions and eventually other laser and EBM systems. This way, Amp starts with precise information about printer parameters and capabilities."
By combining this with GE's knowledge of material properties, Amp can offer "recipes" that have been pre-populated with all the parameters they need to print their part.
"Amp will enable engineers to move through design and development faster. It will help them solve big problems, take on larger parts and make it easier to apply additive manufacturing (AM) to a broader range of parts," said the spokesperson.
Print Model Module
Amp's Print Model module is designed to enhance the AM effectiveness of GE Machines, starting with Concept Laser M2 Series 5 through a secure, intuitive tool that reduces design iterations and speeds up the time to print a good part, according to the design intent.
Benefits of Print Model include:
- Automate manual tasks: Based on real-world best practices, it simplifies the development process of printing parts. Examples: automated orientation, support generation, nesting, labeling, slicing and scan path generation.
- Process tasks in the background: Cloud-based architecture allows the continuation of design work even when process intensive tasks are running in the background.
- Track pedigree: Tracks the relationships captured between various inputs and provides history of printed parts.
- Leverage CAD model: Clean data, no need for STL, no healing.
- Single data-centric process: No saving out to other software tools, no learning separate interfaces, everything in one place.
- Capture known fail points: Notification of potential failure points flagged before print.
Simulation & Compensation Module
"The typical 1:1 compensation method used lacks precision and results in too much trial and error," said the spokesperson. "Traditional simulation tools require many input variables that additive engineers might not have access to and make the process more complex than it needs to be."
Amp's Simulation & Compensation module adds predictive capability to GE Additive machines, starting with the Concept Laser M2, and builds by anticipating distortions, residual stresses, recoater interference and defects prior to manufacturing, and applying corrections before launching production, reducing the lengthy and expensive trial and error process.
Benefits of the Amp Simulation & Compensation Module include:
- Easily add simulation to the additive process: The module has been specifically created for design/manufacturing engineers and reduces barriers for non-simulation experts.
- A unified user experience: A seamless flow in one environment from Build Preparation to Simulation & Compensation. All interactions are saved for future needs
- Saves time: Users are able to digitally iterate until their design intent is achieved. Reduce manual processes and wasted resources from trial builds.
- Reduces costs associated with material and manpower: Users are able to get more parts through development and into production. Maximize number of previously impossible applications to print.
For more information contact:
GE Additive
www.ge.com/additve