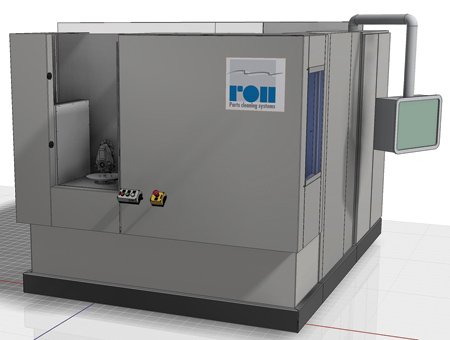
The high-pressure waterjet deburring system FlexJet HD enables efficient deburring and cleaning in one step. In addition to burrs and jamming chips, welding beads as well as layers of paint and scale can also be effectively removed.
With the new high-pressure water jet deburring system FlexJet HD, Karl Roll has developed an efficient solution for deburring and cleaning in one work step. "Burrs and chips can be removed just as effectively as welding beads as well as layers of paint and scale. Individually adapted nozzle systems guarantee a high degree of workpiece flexibility and, at the same time, high precision for reproducible results," said a company spokesperson.
The spokesperson continued, "More stringent requirements for particulate cleanliness result in higher demands on component cleaning and deburring. This applies in particular to machined components such as components for hydraulic and pneumatic systems, housing components, nozzles, components for gears, motors, steering and brakes. Workpieces for medical technology applications can also be affected. In order to achieve the required cleanliness specifications in a stable manner, cleaning the workpieces alone is usually no longer sufficient. This is because burrs and chips not removed during cleaning can become detached in subsequent processes and re-contaminate the component. Reliable deburring of the components is therefore a must in order to meet particulate cleanliness requirements in a stable and economical manner."
Deburring machined components can be a challenge due to areas that are difficult to access, such as internal and intersecting holes, deep and small holes, undercuts and blind holes. Karl Roll GmbH has developed the FlexJet HD series for these tasks. The flexible and efficient high-pressure water jet deburring system enables deburring and cleaning with a water pressure of around 500 bar in one step.
The rotary table integrated in the treatment chamber of the system with pneumatic connections for automatic workpiece clamping devices is designed for components with a diameter of up to 450 mm and a maximum height of 550 mm. The maximum workpiece weight including the clamping device is 100 kg. These dimensions make it possible to handle, for example, an engine block for a four-cylinder engine or several small parts. The waterjet generated in the high-pressure unit with a pressure of up to 500 bar is passed through a four-way nozzle system with automatic nozzle switch.
For precise and reproducible results, the workpiece can be rotated during the process as required and moved along the X-axis. At the same time, the nozzles can be moved along the Y and Z axes. This possibility of very targeted processing not only removes adhering chips from areas that are difficult to access, such as transverse and deep hole bores, but also detaches and removes clamping chips, welding beads and layers of scale. The waterjet can be directed flat for deburring and cleaning larger surfaces. The high kinetic energy also removes stubborn contamination such as sweat residues and silicates.
State-of-the-art control technology is used to position the CNC axes, which are also used in machine tools. The process sequence can be programmed offline using G-code and a teach-in solution via a 15" control panel. There is also the option of programming with a handheld terminal via teach-in. These solutions enable fast programming of the contours to be followed as well as exact positioning in the areas to be deburred without special programming knowledge.
The burrs and chips removed during the deburring and cleaning process are removed by a filter system consisting of a pre-filter and a fine filter. The process water can therefore be circulated without any problem. In addition, a safety filter is integrated in front of the high-pressure pump.
For more information contact:
Karl Roll GmbH & Co. KG
www.karl-roll.de
JCOM
8765 Guion Road, Ste. G
Indianapolis, IN 46268
317-343-4555
sales@jcom-import.com
www.jcom-import.com