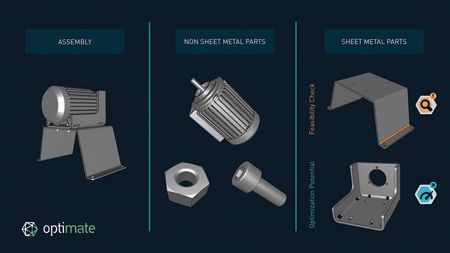
Assemblies with up to 25 individual parts can now be checked for feasibility and optimization potential in an automated and AI-based way in the app platform.
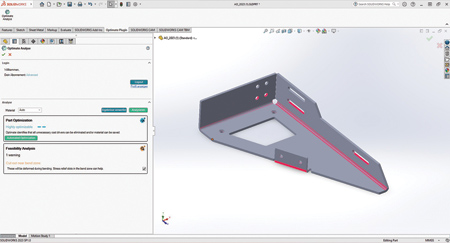
The TRUMPF start-up is looking for more test users from the sheet metal processing industry for its new SolidWorks CAD plug-in.
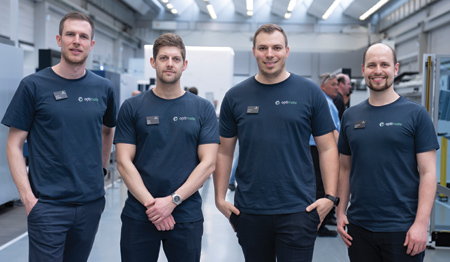
Optimate's sales team (l-r) CEO and co-founder Jonas Steiling, Sales Manager Miles Barke, Sales Manager Patrick Klein, CSO Sebastian Beger
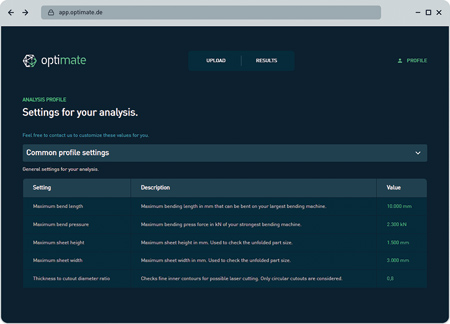
Personal analysis profile in the Optimate App: The maximum bend length, maximum bend pressure, existing tool pairings and individual minimum flange lengths are used for the feasibility analysis.
Optimate, the TRUMPF spin-off, is announcing two extensive upgrades to its cloud-based software solution for analyzing and optimizing sheet metal parts. In response to increasing user demand, assemblies with up to 25 individual parts can now also be analyzed. Moreover, a new CAD plug-in for SolidWorks makes design optimization more user-friendly.
Optimate's digital service includes two main functions: Feasibility Analysis and Part Optimization. Both have been given a user-friendly upgrade with the new features.
"Sheet metal processing companies in particular will be pleased with the option to check assemblies for feasibility. In our app, job shoppers can identify defective parts in advance and adapt them as required before they reach the bending machine," said CEO Jonas Steiling. "We have now extended this analysis to include assemblies."
In addition to the analysis of single parts, assemblies with up to 25 individual parts can now also be checked for feasibility and optimization potential. To this end, the assembly uploaded to the app is being dissolved into its individual parts and examined under a digital microscope.
"For single sheet metal parts, our service already works entirely automatically," said Sales Director Sebastian Beger. "For the comprehensive analysis and optimization of assemblies, it is currently still a hybrid process: following the initial analysis with our tool, we take another look at the assemblies ourselves and offer personal consulting. In the future, we will fully automate the entire process. The AI-based solution's database will help ensure that the new assembly analysis function will also be available in a fully automated form in the long term."
In our app, the user is given tips as to whether and how the individual parts of an assembly can be manufactured reliably and possibly more cost-effectively," said Steiling, explaining the function. "However, in the case of assemblies, consultation with the design department has been required in most cases so far. The new function does things differently: if, for example, the minimum flange length of a sheet metal part is not met, it also impacts the underlying assembly-and this is precisely what the app detects. The analyzed individual parts can then be adjusted with just one click and the corrected CAD data conveniently downloaded."
A spokesperson said, "Optimate holds decades of sheet metal design knowledge for sheet metal processing in digital form at the ready. In the future, this valuable knowledge will also be stored for entire assemblies. The new feature for dissolving assemblies can already be used. In perspective, the analysis in the app platform should work in an automated and AI-based way for the redesign of assemblies."
Optimate is also offering a beta version of its SolidWorks CAD plug-in for trial customers. With the plug-in, designers benefit from an improved workflow because they can test and optimize their parts for feasibility directly in the system without having to export the CAD data and upload it to the app. Since users best understand the application case, they can now view the design proposals directly in the CAD system and check them for suitability. The final decision to adapt or optimize a part is up to the designer. There are also plans to continuously advance the CAD plug-in and integrate it into CAD programs from other providers.
Also new is the full customization of all analysis-relevant settings for the part analysis. Machine data can be customized and viewed on the user profile in the App. For example, the maximum bend length, maximum bend pressure, existing tool pairings or individual minimum flange lengths are stored and used for the feasibility analysis.
For more information contact:
Optimate
info@optimate.de
www.optimate.de