


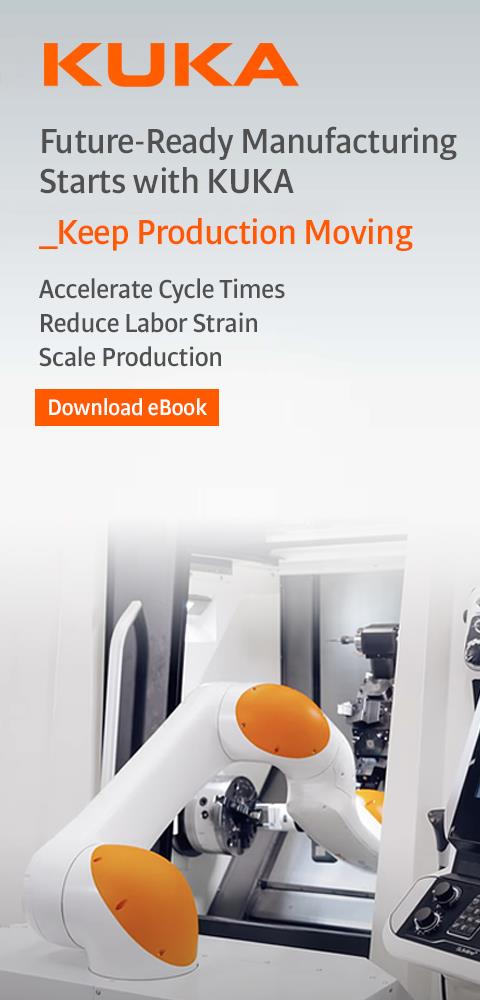
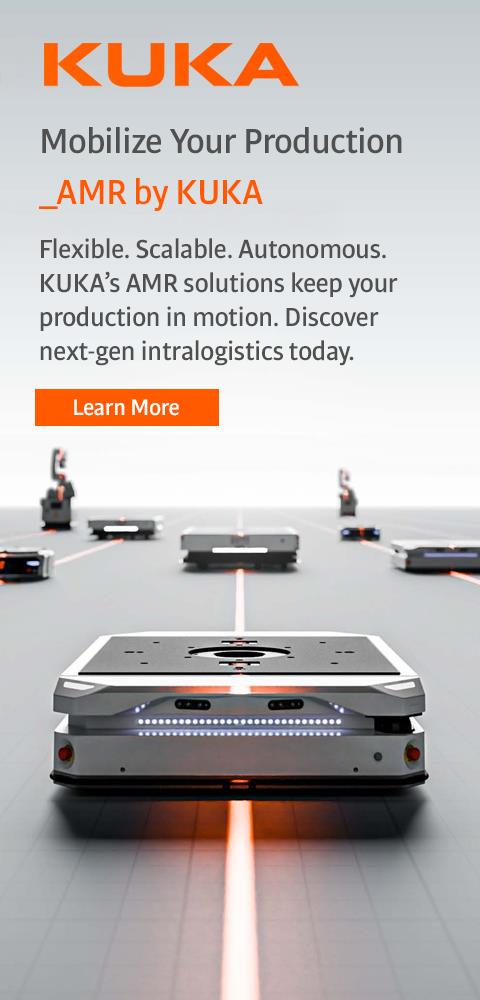
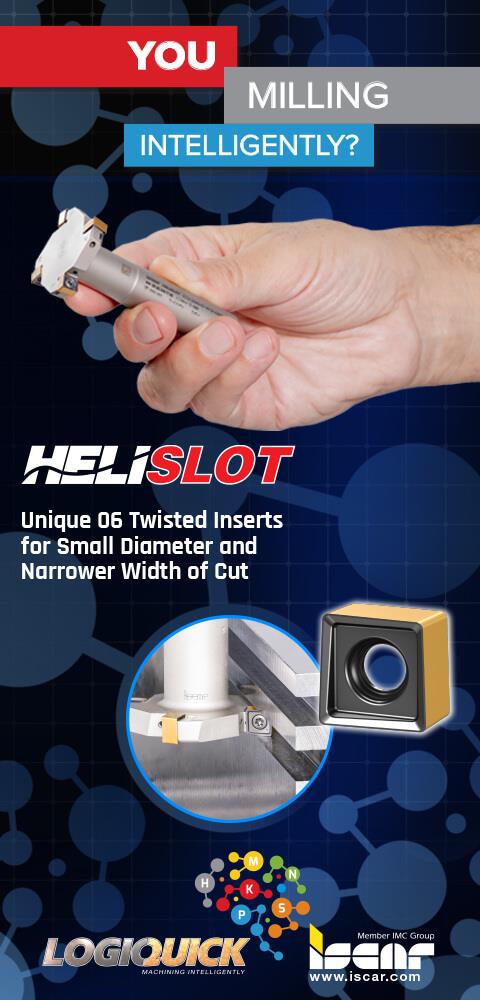
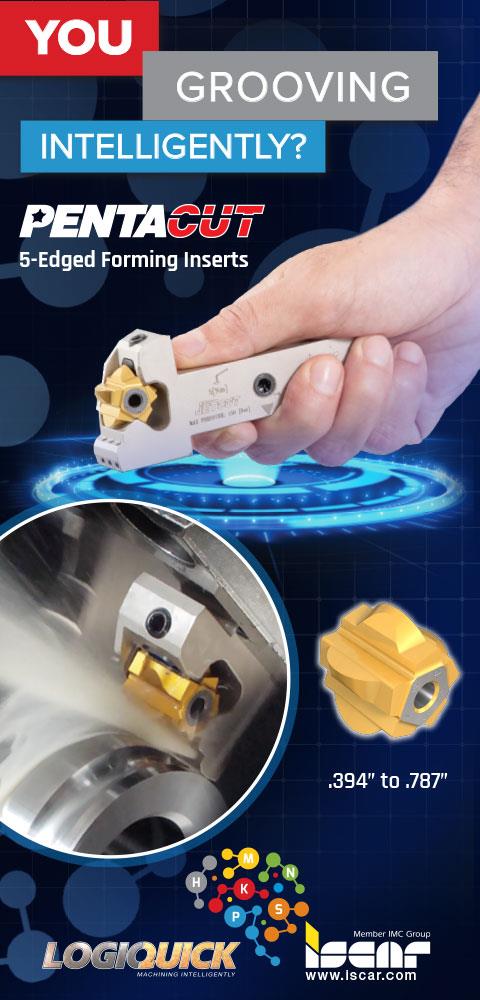
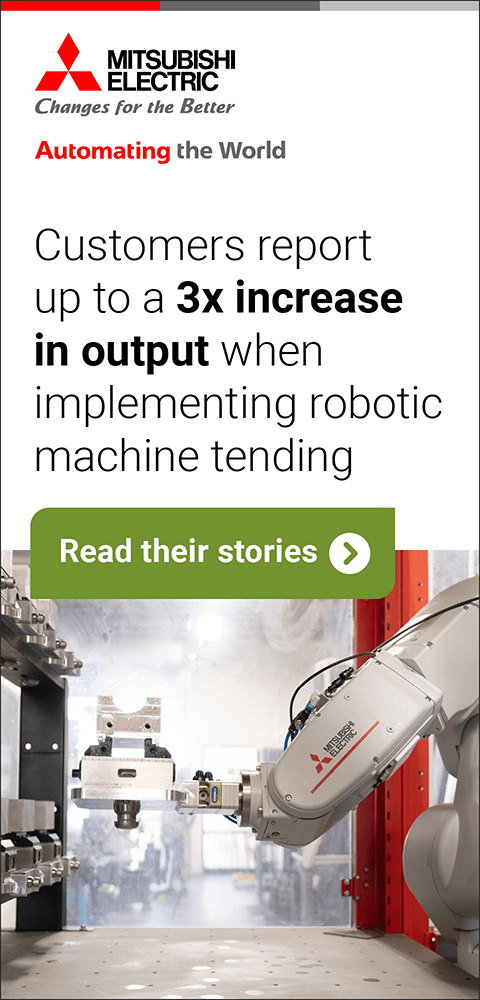
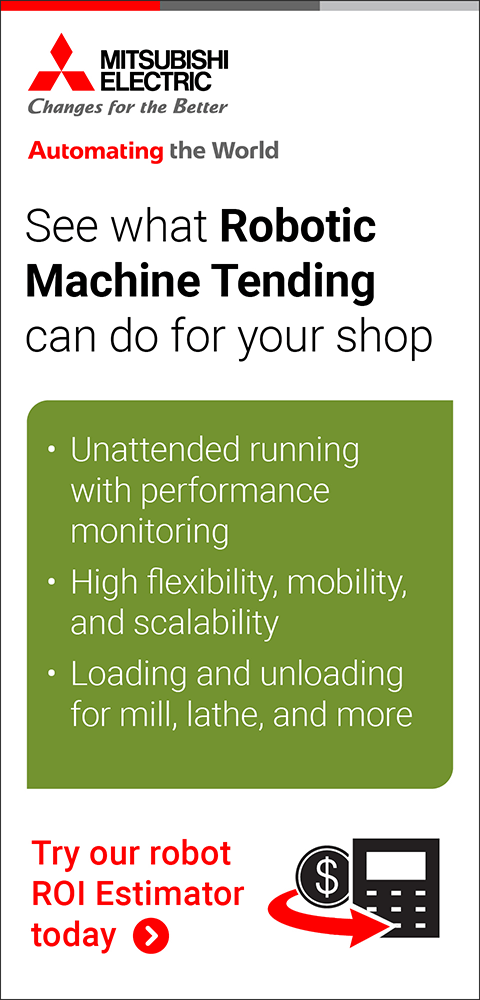


Double Disc Grinding Process for High Performance Engineered Thermoplastic Strip Material
June 1, 2017
Glebar has developed a double disc grinding process on its DD-7 Double Disc Grinder for materials suppliers and manufacturers of high performance composites that expedites the grinding of composite strips used as low friction, bearing elements in various industries from aerospace to automotive - leading to reduced production costs and enhanced quality.
A recent case study for a major supplier of sealing solutions demonstrates how the automated DD-7 was able to cut the grinding rate down nearly four times versus the previous manual method utilized by the customer.
The main challenge was to achieve the tight flatness tolerances required in a continuous spool-to-spool process by double side grinding the strip at a fast throughput rate. This process was facilitated by the use of a tractor and two 10" grinding wheels with material feeding and extraction using spool assemblies. A unique grinding wheel configuration allowed the material to be rapidly removed while maintaining a thickness tolerance on a product that is engineered to be wear resistant by nature.
The company reported the results of the case study are as follows:
Feedrate: 6 meters per minute (19 feet per minute)
Grind: 25 mm strip 2.9 down to 2.42
Material removal: 0.25 mm per side (0.010" per side)
Tolerance: +/-0.025 mm (+/-0.001")
"The double disc grinding development process for composite strips can be an arduous task. Prior to using the DD-7, one of the largest challenges our customers had with grinding this type of material and shape was the limitations of belt sanding machines which require multiple passes on each side, requiring operator handling and take up a lot of floor space," said Robert Gleason, VP of Engineering for Glebar Company. "By utilizing the DD-7's tractor infeed extractor coupled with spool feeding and collection systems, the ability for continuous feeding, grinding and extracting the material without operator intervention was possible." The machine also had to be built, assessed and tested to accept the CE mark. Several standards including the EU Machinery Directive and EMC directive insured that the DD-7 is in conformity with CE standards.
For more information contact:
Glebar Company
565 East Crescent Ave
Ramsey, NJ 07446
800-235-5122 / 201-337-1500
www.glebar.com
< back