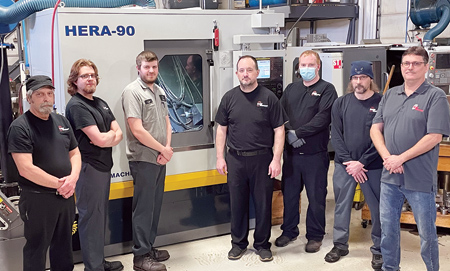
(l-r) Kevin Geloge, William Abke, Kyle Dobbs, Richard Conger, Patrick Greer, Tim Hoban and Lon Parker
"We saw market growth potential by adding hobbing ability for small-diameter parts and for long-shaft hobbing, meaning parts over 500 mm long," said Terry Roach, Sales Manager for Gear Master, recalling the challenge for the job shop's growth in 2019. Gear Master's next step for growth appeared to be in smaller parts and longer parts, and the company found an ideal solution that solved both needs. This machine, a Helios Hera 90-W horizontal CNC gear hobbing machine, provided a complete installed package within a few months. "It provides ability to hob small diameter parts, capacity for part lengths up to 600 mm, high-speed carbide hobbing, domestic support in the Midwest and a price that ensured a profitable platform for the future," said Roach.
Gear Master specializes in precision gear and spline manufacturing. Since its start in 1997, the company has built a wide range of CNC machining capabilities that include dedicated grinding and hobbing platforms. Gear Master serves the aerospace, defense, medical and industrial sectors with work for flagship programs such as the Boeing 787 Dreamliner, the Lockheed Martin C-130, JASSM Missile, a Stryker surgical drill, various Caterpillar and Allison Transmission projects and electric vehicles. The following applications showcase how the new Hera 90-W from Helios Gear Products has improved Gear Master's ability to serve its customers.
A 32 DP, 26-tooth, 303 stainless steel spur gear requires AGMA Q9 quality. This part-which is used in a surgical device-requires highly productive hobbing to be profitable for a job shop. This was a challenge before because a mid-20th century hobber limited the application to only two pieces per cycle due to the machine's lack of rigidity. Today, Gear Master manufactures these parts four pieces per cycle using high-speed hobbing on the Hera 90-W. Consequently, the shop's productivity has greatly increased.
Gear Master has found Helios to be a reliable partner to support demanding applications. For example, to satisfy a quick-delivery Dana Corp. prototype job for the electric vehicle market, a small-diameter tool was required. Helios delivered a carbide hob with arbor tooling in under four weeks, enabling Gear Master to exceed customer expectations. Helios provides ongoing technical support with applications engineering, cutting tools, abrasive tools and industry training. "This holistic approach from a machine's install throughout its entire life ensures manufacturers like Gear Master can compete at their top level every day of the week," said Jason Spitzer, Regional Sales Manager for Helios Gear Products.
In another application, a 1.95 module, 19-tooth, 32° helical gear needed to be cut on a long-shaft part for an Olympic transportation vehicle. Gear Master was challenged by losing 18% of their production due to quality issues from chatter and lead error. The job shop was also constrained by the application's target cycle time that maxed out the incumbent CNC hobbing platform, forcing the application to use an aggressive feedrate. By moving the application to the Hera 90-W, Gear Master was able to overcome the application's challenges: The same workholding strategy is used, but the new machine inherently removes chatter and improves lead error by offering a more rigid platform. Furthermore, the new machine offers hobbing speeds up to 6,000 RPM, which Gear Master uses to optimize the application by increasing speed and decreasing feed. Consequently, today the parts meet quality with a minimized fallout rate, thus saving the job shop on scrap parts.
"Our operators are very pleased with the ease of programming on the machine and with the high repeatability of the machine," said Lon Parker, Operations Manager for Gear Master.
For more information contact:
Gear Master Inc.
7481 Research Drive
Almont, MI 48003
810-798-9254
www.gearmaster.us
Helios Gear Products, LLC
635 Schneider Dr.
South Elgin, IL 60177
847-931-4121
sales@heliosgearproducts.com
www.heliosgearproducts.com