




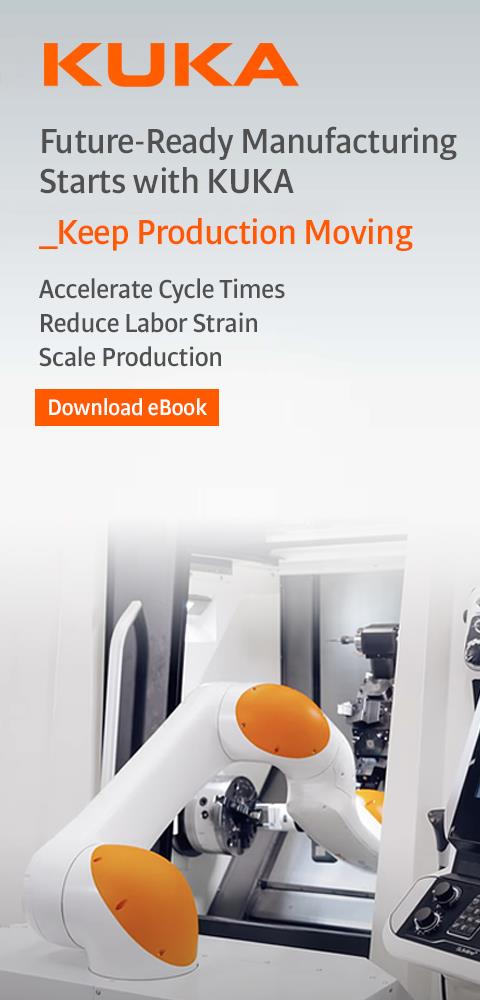
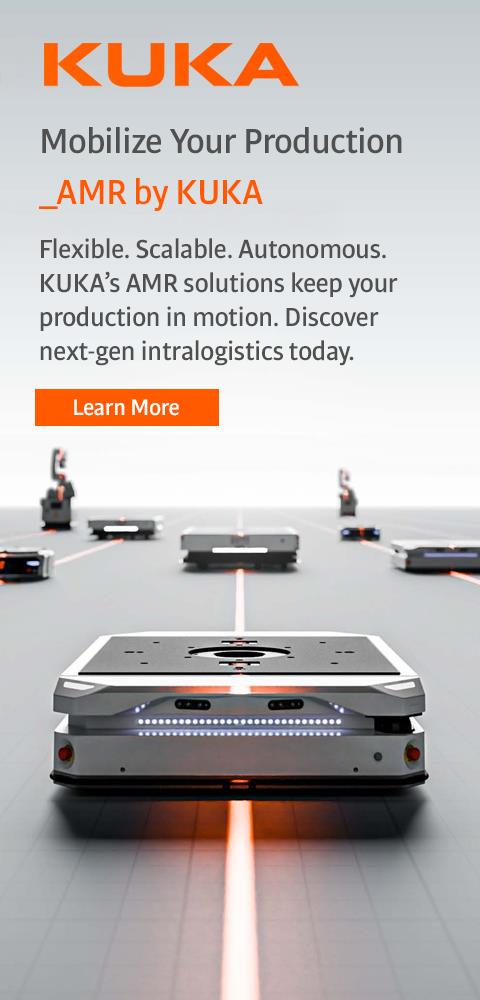
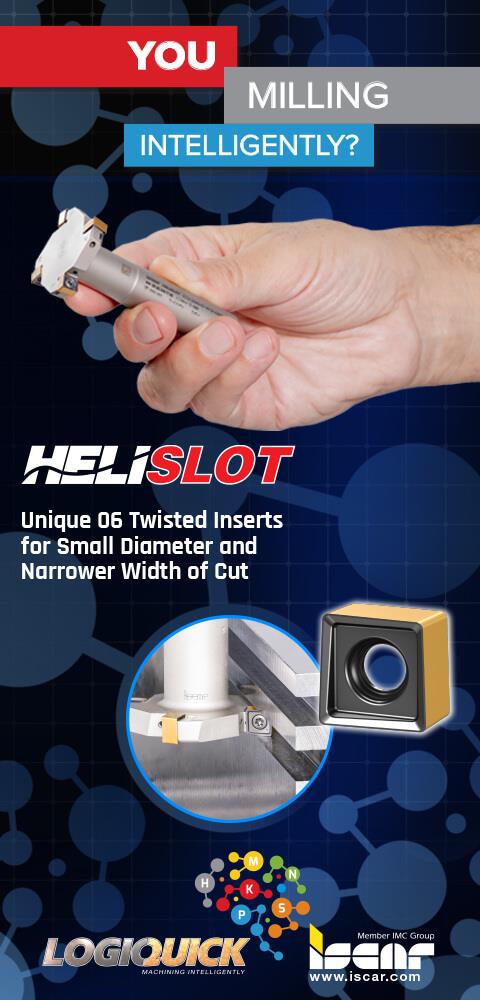
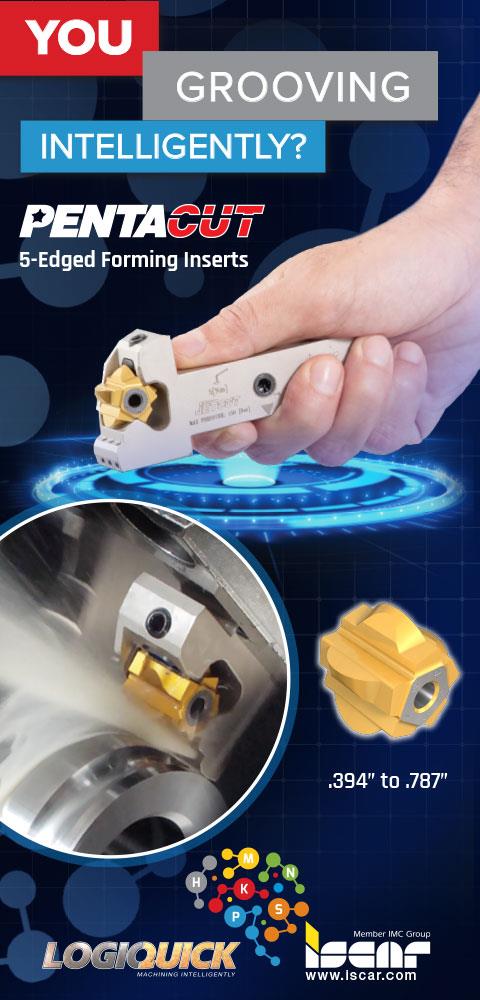
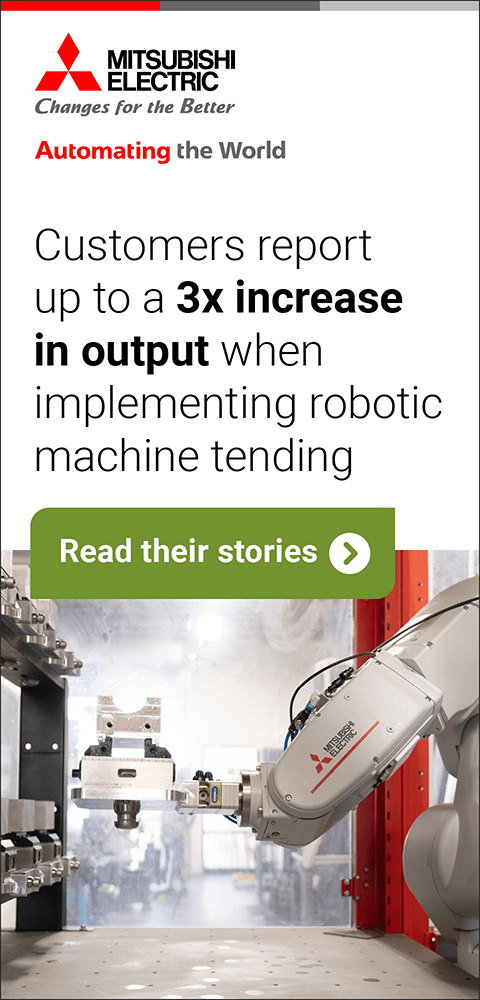
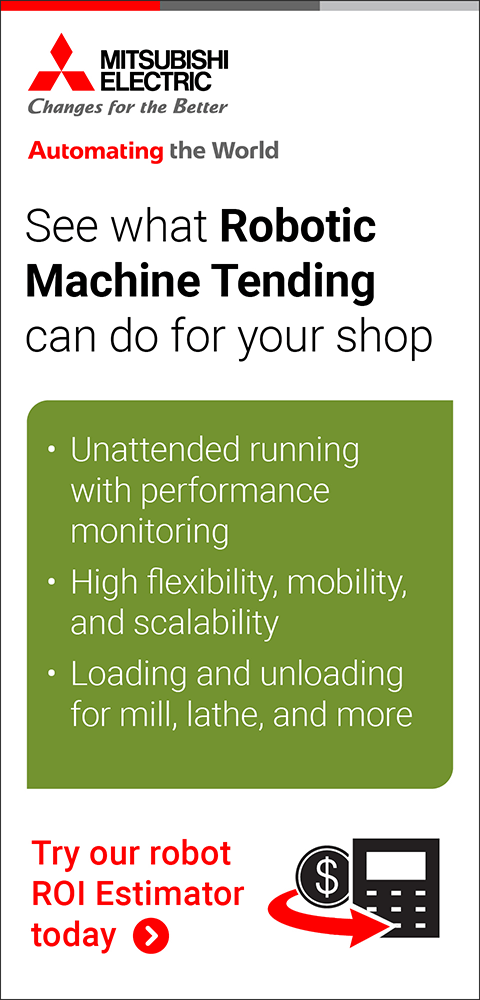
Ultrasonic Scanning of Large Composite Components
September 1, 2021
Olympus' new RollerFORM XL scanner is a wide-coverage and easy-to-implement phased array tool designed to accelerate the inspection of composite components with large surface areas.
"In the aerospace and wind energy industries, critical components such as aircraft wings and wind turbine blades are made with lightweight, durable composite material," said a company spokesperson. "Inspectors use nondestructive testing technology to ensure the integrity of these parts, both before they are assembled and for in-service maintenance. Ultrasonic testing is a standard method, but the parts' extensive surface areas, the attenuative nature of composite and the complicated operation of some ultrasonic testing equipment can cause problems. The new RollerFORM XL scanner is an innovative and easy-to-use phased array wheel probe that helps resolve these issues."
Based on the original RollerFORM scanner design, the RollerFORM XL scanner's tire with integrated phased array probe provides a beam coverage that is twice as wide. Scanning large parts is more efficient and the data's accuracy is improved since the wider beam coverage also increases the probability of detection.
"Light and easy to operate, the RollerFORM XL scanner takes minimal effort to set up and inspect compared with immersion-based testing," said the spokesperson. "Strong, reliable signals are obtained without a couplant pumping system due to the scanner's innovative tire. Interface reflections are minimized because the tire is filled with liquid and the material has an acoustic impedance that closely matches water. This similarity enables the ultrasound beam energy to transmit efficiently into the part."
Beam penetration is optimized in attenuative composite materials because of the RollerFORM XL scanner's optional low-frequency, large-elevation phased array probe. Inspectors can easily integrate this new wider model into existing wheel probe procedures. The RollerFORM XL scanner also has an encoder, an indexing button and a start acquisition button to facilitate complete scans of large wings or blades.
For more information contact:
Olympus Scientific Solutions Americas
48 Woerd. Ave.
Waltham, MA 02453
781-419-3900
www.olympus-ims.com
< back