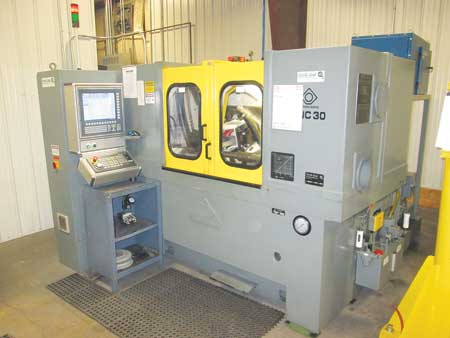
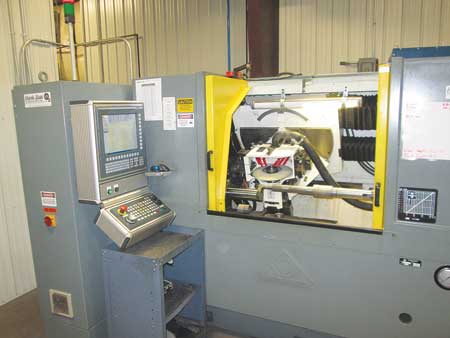
An advanced CNC retrofit package based on NUM technology doubles the accuracy of Klingelnberg SNC 30 hob sharpeners, according to the company.
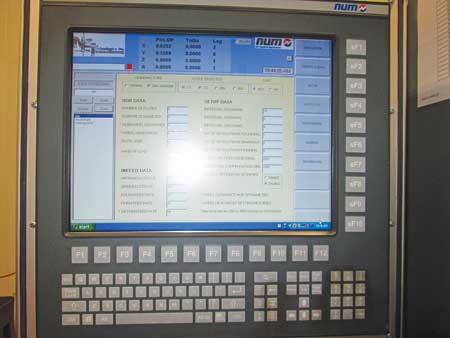
Machine operation is simplified by the 15" flat screen and large function keys of NUM's Flexium control panel.
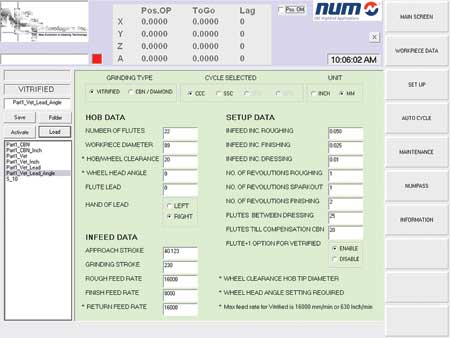
The HMI preserves the familiar look and feel of the SNC 30 by using "fill in the blanks" programming.
In collaboration with NUM, machine tool rebuilder North East Technologies Inc. has developed a CNC retrofit package that brings the performance of early generation hob sharpening equipment up to modern day standards, according to the company. "The system doubles accuracy and can increase the productivity of machines immensely - by margins of 40% or more," said a company spokesperson. "By extending the life of hob sharpening machines and enhancing their performance, the retrofit provides gear manufacturers and tool service companies with a cost-effective alternative to purchasing new equipment."
North East Technologies specializes in servicing and rebuilding hob sharpening equipment. A major part of its business is retrofitting modern control systems to early generation hob sharpeners, such as the SNC 30 and AGW Series machines originally produced by Klingelnberg in the 1980s. To expedite refurbishment, North East Technologies decided to develop a standard high performance CNC retrofit package that could readily be adapted to different machine configurations.
"Most companies that cut gears or service gear cutting tools have at some time used Klingelnberg SNC 30 hob sharpeners," said the spokesperson. "Capable of handling work pieces up to 300 mm (12 inches) in diameter, they can grind helically fluted hobs to a depth of 90 mm (3.5 inches). They are widely regarded as an industry standard - there are hundreds of these machines in the USA alone, many of which have been in continual use for 25 or more years. However, despite still being mechanically sound, most of these machines are showing signs of age. Their motion control hardware is not up to today's standards in terms of speed, accuracy or efficiency, so the machines act as a production bottleneck. And as their original CNC systems become increasingly unreliable, and use obsolete components, rising support costs and downtime eventually renders them ineffective.
"When choosing a control solution provider for the retrofit package, North East Technologies was heavily influenced by its customers, many of whom request NUM's CNC technology for machine upgrades. Most of these customers regard NUM's gear hobbing solution, NUMgear, as the best in the industry, and are aware of the local development resources that can add further functionality from NUM Corporation's headquarters in Naperville."
According to Harry Salverston, President of North East Technologies, "NUMgear provided much of the functionality we needed for our hob resharper retrofit at the outset, making it an ideal platform. And NUM's willingness to partner with us to develop application-specific features we wanted - such as a custom HMI and special machine code - confirmed this choice. NUM effectively acted as an extension to our own engineering resources to help speed development."
The CNC retrofit package content depends on the configuration of the hob sharpener. Basic SNC 30 machines have two CNC axes as standard - one (X) for the wheelhead slide and the other (A) for the workpiece spindle - and can be fitted with a further two optional axes to automate axial (Y) and radial (Z) movement of the wheelhead. At a customer's request, North East Technologies will incorporate these extra axes during the retrofit process. In addition to upgrading the machine's controller to a NUM Flexium 68 CNC system, the retrofit replaces all motors and drives with high performance NUM servomotors and NUMDrive C servo drives. The new servomotors are equipped with high resolution 262,000 pulse/rev encoders (the original motor encoders were 1,000 pulse/rev devices) which in conjunction with the powerful Flexium CNC kernel provide much more accurate control of speed and position.
According to the company, considerable attention has been paid to ensure that the HMI of the CNC retrofit preserves the familiar look and feel of the original SNC 30 operating system. A "fill in the blanks" programming method, backed by custom control macros, means that the machine operator is not presented with unfamiliar CNC nomenclature, and simply enters parameters such as the length of flute and the amount of material to be removed. Each screen is context-sensitive to eliminate ambiguity. For example, selecting a grinding cycle that uses a CBN (cubic boron nitride) wheel opens a folder that only contains options for CDG (conventional deep grinding) and SDG (single flute deep grinding), with dressing disabled. The software also allows the operator to "teach" the machine the relative positions of the X,Y, Z and A axes under manual control, enabling grinding cycles for different hobs to be easily developed.
To maximize flexibility, the application accommodates multiple hob sharpening methods, including removal of stock in one or both directions of wheelhead traverse. For straight fluted hobs, as soon as one flute has been sharpened the workpiece is indexed through to the next flute and sharpening recommences. Utilizing the Flexium CNC system's Dynamic Operator (DynOp) function, the machine builder can create custom axes linkage or compensation in real time at the position loop clock cycle. In the case of sharpening helically fluted hobs, this DynOp feature allows the rotary (A) axis to be transparently synchronized to the X axis, so the grinding wheel accurately follows the helix angle.
"North East Technologies' CNC retrofit provides gear manufacturers with considerable long-term benefits", said Harry Salverston. "Our first SNC 30 upgrade project using the new NUM package involved retrofitting a two-axis machine in 2011. This has operated without problems ever since and has enabled our customer to improve the quality of their gear sharpening process substantially by more than doubling its accuracy, as well as increasing throughput by about 40%. Together with NUM, we have further developed the CNC retrofit package and following recent orders are currently rebuilding three machines, including a 2- to 4-axis conversion."
For more information contact:
Steve Schilling
NUM Corporation
603 East Diehl Road, Suite 115
Naperville, IL 60563
630-505-7722
sales.us@num.com
www.num.com