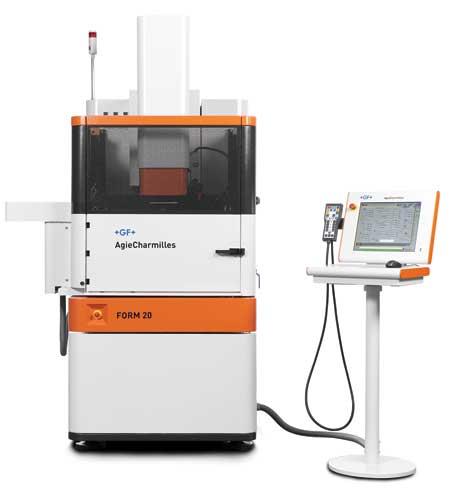
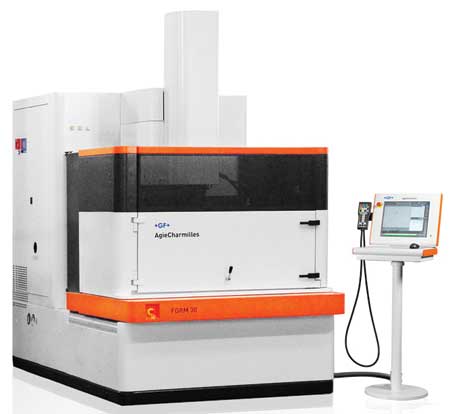
GF Machining Solutions' FORM 20/FORM 30 machines feature a smart module to improve machining efficiency and reduce unproductive time, a new and intuitive HMI and built-in technology to eliminate electrode wear.
The FORM 20 and FORM 30 are compact die-sinking EDM machines with an integrated rotary tool changer with 16 positions for the FORM 20 and 26 positions for the FORM 30. "The compact design means a 940 x 540 mm workplace can be loaded in a machine that consumes a small amount of space. The machine's rigid mechanical concept is designed for reliable and stable operation, due to a cast iron, short C-frame design for static and dynamic rigidity. Linear glass scales on the cross table guarantee positioning accuracy," said a company spokesperson.
They feature a high-power generator, the GF Machining Solutions AC FORM human-machine interface (HMI) and built-in technology to help eliminate electrode wear. "In combination with excellent performance, these features make them a go-to choice for general mold and die and specific industries like aerospace and aeronautics, automotive and information and communications technology," said the spokesperson.
Like all machines in GF Machining Solutions' FORM range, the FORM 20 and FORM 30 feature the ergonomic AC FORM HMI. Developed to streamline the moldmaking process, AC CUT HMI is organized on one menu level where all icons are arranged logically and in chronological order of use and dynamic contextual help is a click away.
Common measuring cycles, from simple measurement of the Z position to complex measurement requiring moving the measuring probe around the workpiece due to the C-axis, are integrated into the numerical control of the FORM 20 and FORM 30. That means the position of the workpiece is plotted so the operator does not need to adjust the workpiece, therefore time to erosion is reduced and the workpiece can be placed into the working area without wasting time on manual alignment.
"The FORM 20 and FORM 30 have onboard intelligence that makes it easy for less experienced machinists to achieve expert results with very little training. Elimination of a steep learning curve means novice machinists can operate the FORM 20 and FORM 30 and expert machinists can be allocated to more demanding tasks," said the spokesperson.
"GF Machining Solutions' own high-end, Intelligent Power Generator (IPG) is at the heart of the FORM 20 and FORM 30. TECFORM ensures that the EDM process is optimized with each pulse to reduce electrode wear and reach the finest finishes.
"The embedded TECFORM module allows the FORM 20 and FORM 30 to achieve the best performance and produce the desired result. Segment-dedicated technology eliminates the need for the operator to adjust the generator's parameters. Spark process control takes a fraction of a second and produces a homogeneous surface finish," said the spokesperson.
GF Machining Solutions' iQ (innovation + quality) technology is standard to the FORM 20 and FORM 30. It is designed to provide low electrode wear due to pulse efficiency and fewer pulses required for effective erosion. "The iQ technology helps ensure wear-free spark erosion, high precision, efficient performance, respect for detail and greater control over the cost of the tool (the electrode)," said the spokesperson.
For more information contact:
Gisbert Ledvon
GF Machining Solutions
560 Bond St.
Lincolnshire, IL 60069-4224
800-CTC-1EDM
gisbert.ledvon@us.gfac.com
www.gfac.com/us