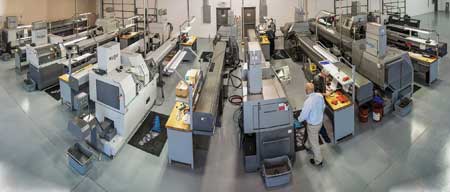
An overview of MK Precision's Swiss Machining Department is shown. MK Precision operates in a 17,000 sq. ft. facility to produce components for the medical, aerospace and defense industries.
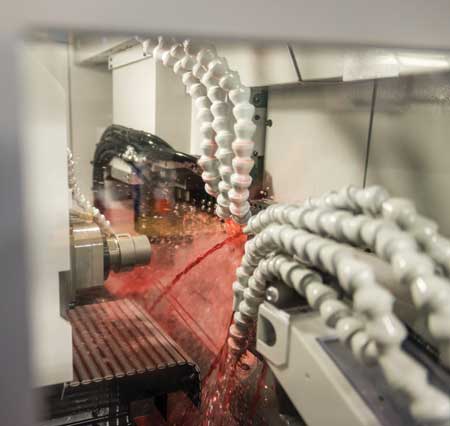
The view inside the latest Citizen-Cincom L20XII machine added at MK Precision is shown. The L20XII is designed for contouring with simultaneous 4-axis control.
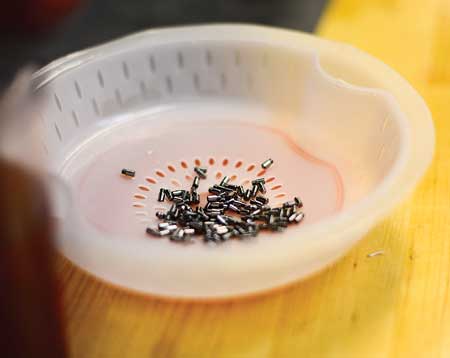
A sample of parts produced on Citizen-Cincom Swiss machines is shown. "For the complex parts MK Precision manufactures, the Citizen-Cincom Swiss machines have given us increased capabilities and superior quality finished products that our customers have come to expect," said Ron Bates, Director of Marketing, MK Precision.
Established in 2005 by Michael Klesh, a CNC machinist/programmer by trade, MK Precision, Warminster, PA, has continually adapted to the ever-changing needs of its clients. "The number-one reason we consider adding new equipment would be for a new component we are manufacturing," said Ron Bates, Director of Marketing, MK Precision. "In the medical and aerospace markets, we work in close tolerances. Parts themselves are getting increasingly tight and complex, and the machines needed to make them are our most important strategic purchase and source of pride when meeting our goals. Without the newest machines and their newfound capabilities, some of the work we do simply would not be possible."
According to Bates, when evaluating the need for new machines, the company's engineering team decides what would be the best fit for current and projected work. "We get all the facts and scenarios kicked around and make a choice in which direction to go," he said.
The company's most recent purchase is the newest technology from Citizen-Cincom, the new L20XII Swiss machine from Precision Machine Tool Solutions in Sinking Spring, PA. The Citizen-Cincom L20XII is designed for contouring with simultaneous 4-axis control. The machine has a full B-axis and is guide bushing and non-guide bushing switchable to 25 mm bar capacity. "The guide bushing to a non-guide bushing set-up can be changed over in about 30 minutes," said Randy L. Heck, President, Precision Machine Tool Solutions. "This is a simple task. The guide bushing feature is ideal for typical Swiss parts which have three times length to diameter ratios. The non-guide bushing feature can machine shorter length parts, generating greater part roundness from any cold drawn material, and it also reduces the overall remnant length, allowing for more parts per bar length."
The rotary tools on the gang tool post feature the additional B-axis live tool head with eight live tools, four front facing and four rear facing, control allowing for the drilling and milling of angled and full contoured features. The B-axis has a full range of 135°, from 0° to 134°. This enables the B-axis to be used for both front spindle and back spindle machining.
"The opposite tool post with the Y2-axis control accommodates up to six rotary or fixed tools and the back tool post, with four rotary and four fixed tools, that provides greater capability and high productivity," said Heck. "A variety of simultaneous machining operations can be performed on the main- and sub-spindles, making it possible to substantially reduce cutting time. Enhanced end face and cross rotary tools offer greater flexibility within the machining of complex shapes."
High-speed spindles with variable RPMs up to 80,000 RPM were also integrated onto MK Precision's existing Citizen-Cincom Swiss machines, further improving capability and productivity.
These new solutions have benefited MK Precision, which works primarily with complex medical assemblies and medical implants for the spine/hips and instrumentation to support the devices. The shop's Swiss machining processes are capable of achieving tolerances within +/- .0001".
Contract manufacturer MK Precision relies on multi-axis machining centers to produce components for the medical, aerospace and defense industries. "We deliver the best medical device products in the fastest time," said Bates. "We use both true 5-axis CNC mills/lathes as well as Swiss style screw machines in various capacities for our work here."
"For the complex parts MK Precision manufactures, the Citizen-Cincom Swiss machines have given us increased capabilities and superior quality finished products that our customers have come to expect," said Bates. "We can run the Citizen-Cincom machines around the clock, and the demand of quality parts from our customers has us always focused on the newest technologies. Our team is constantly rethinking the way we make our parts. Utilizing these new Swiss machines to their fullest potential has paid off in spades and will continue to drive our growth well into the future."
MK Precision manufactures the following medical components:
- Minimally invasive spinal implants and instruments
- Lumbar/thoracic implants
- Vertebral body replacement systems
- Pedicle screw systems
- Polyaxial screws, uniplanar screws, monaxial screws, hooks and rod connectors
- Cervical plate and screw implants
- Implant grade PEEK spacers and screws.
"There is really no room for error," said Michael Klesh, Owner of MK Precision. "When a surgeon is going to take one of our devices and implant them, he cannot miss. He cannot have a bad day. Our guys have to follow that same mold. They have to have the best tools so that they do not miss."
The company also provides the following services:
- Burr-free parts
- Laser marking
- Titanium anodize
- Laser welding
- Chrome plating
- Ultrasonic cleaning
- Passivation
- Electropolishing
- Assembly
- Exotic materials
- PEEK
- Contaminate-free machining
- Full CAD/CAM services.
In addition, the company also makes many different fasteners for use in the aerospace market. "Materials we work with include stainless steel, aluminum, titanium of various grades and PEEK polymer," said Bates.
MK Precision has 30 employees and operates in a 17,000 sq. ft. facility. The company is FDA- and ITAR-registered, and it is certified in IS0 9001:2008 and ISO 13485:2003 Quality Management Systems. "Our experienced engineers, CNC machinists and Quality Control personnel scrutinize each phase of development utilizing the best technologies available," said Bates.
For more information contact:
Ron Bates
Director of Marketing
MK Precision
309 Camars Dr.
Warminster, PA 18974
215-675-4590
rbates@mkprecision.com
www.mkprecision.com
Randy L. Heck
President
Precision Machine Tool Solutions
571 Mountain Home Road
Sinking Spring, PA 19608
610-670-6780
rheck@pmtscnc.com
www.pmtscnc.com