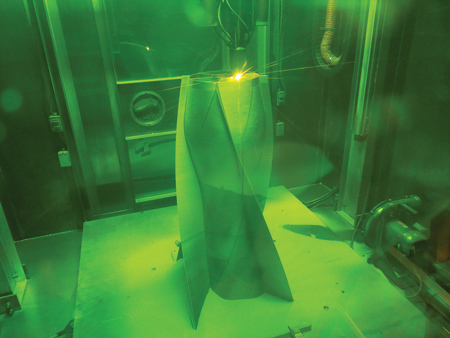
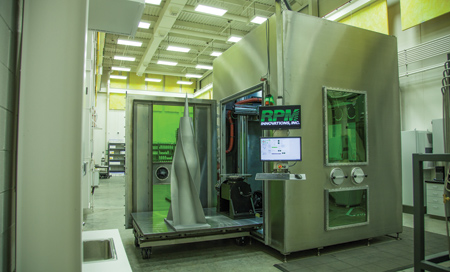
An Inconel 625 rocket (83" tall) being built with laser freeform manufacturing technology (LFMT) on the 557.
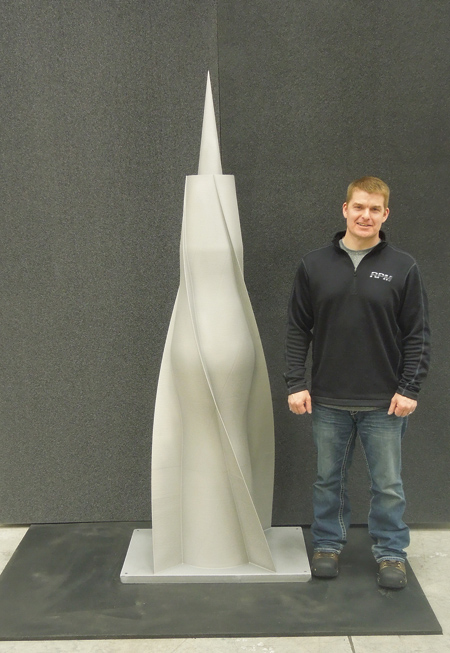
Kory Bockelmann, Quality Manager, RPM Innovations, with the completed rocket. The part took 341 hours of laser deposition time on the 557.
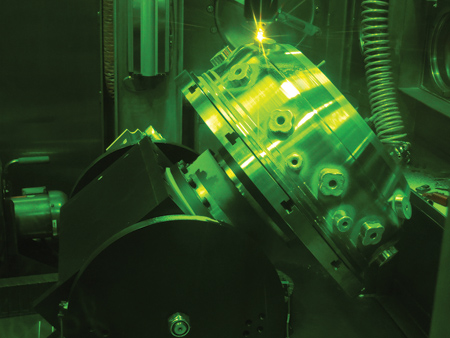
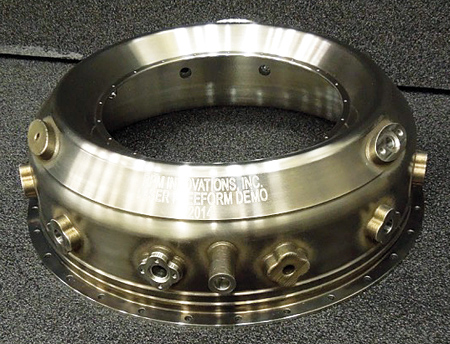
Inconel 718 combustor case (23" O.D.) completely built with laser freeform manufacturing technology (LFMT). The part took 132 hours of laser deposition time. The part was built, heat treated and final machined after heat treat.
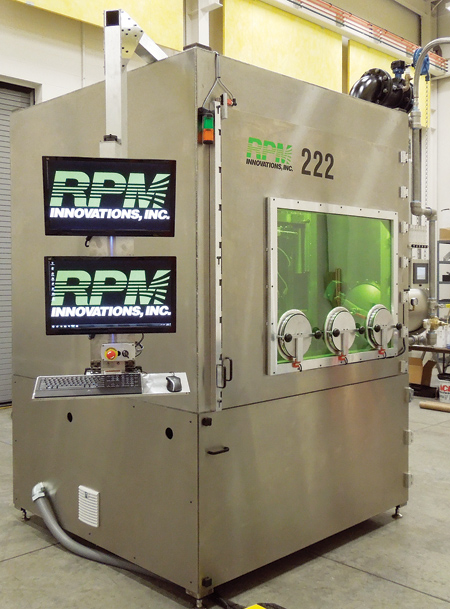
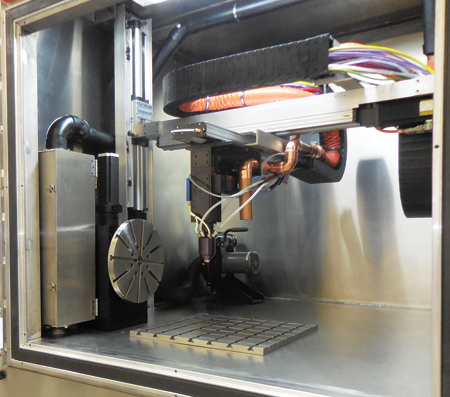
The RPMI 222
RPM Innovations offers its 222 and 557 professional grade systems featuring powder fed laser metal deposition technology.
Laser deposition technology (LDT) is a process in which metal powder is injected into the focused beam of a high-power laser under tightly controlled atmospheric conditions. The focused laser beam melts the surface of the target material and generates a small molten pool of base material. Powder delivered into this same spot is absorbed into the melt pool, thus generating a deposit that may range from 0.005" to 0.040" thick and 0.040" to 0.160" wide. The resulting deposits may then be used to build or repair metal parts for a variety of applications. Suitable industries include aerospace, defense, energy, marine, mining, construction and tooling.
The RPMI 222 system features laser head XYZ travels of 609 mm x 609 mm x 609 mm and a laser build envelope of 0.23 cubic meters. It offers CNC controlled XYZ axes and rotating table. It has a 2 kW IPG fiber laser with chiller. Other features include a large 1,333 mm tall x 1,524 mm wide front access door and a laser-safe viewing window.
The RPMI 557 system features laser head XYZ travels of 1,524 mm x 1,524 x 2,133 mm and a laser build envelope of 4.95 cubic meters. It features 5-axis motion with CNC controlled XYZ axes and a modular heavy-duty tilting/rotating table. It has a 3 kW IPG fiber laser with chiller. Other features include large 2,400 mm tall x 1,700 mm wide front/rear access doors, multiple laser-safe viewing windows, a fume collection system and a heavy-duty servo part shuttle (5,000 kilogram capacity).
Both systems offer the following features and benefits:
- Toolpath generator (TPG) - Import STL files and create tool code (includes layer viewer and simulator)
- Laser deposition machine control software (LDMC) - Load toolpath code and build parts (manual position/activate features; rapid file loader; event logger; variable speed jogger)
- RPMI vision software - View deposition surface, precisely align laser head (movable and sizable crosshair for alignment/laser targeting; customizable zoom, iris and focus)
- Two 600 mm displays, keyboard and mouse on HMI pendant
- Two dual-hopper servo driven powder feeders for continuous operation
- Industrially hardened optics box and vision camera
- Safe and reliable handling of high power levels and back reflection
- Industrially hardened water-cooled 25° four nozzle deposition head
- Industrially hardened water-cooled co-axial deposition head
- Long life nozzles and optics for continuous operation
- Argon atmosphere glove box
- Custom gas purification system
- Oxygen level controlled to less than 5 ppm
- Antechamber (375 mm D x 600 mm L) for passing smaller parts
- Polished stainless steel construction
- Hermetically sealed Class 1 laser enclosure
- Easy to clean and maintain.
For more information contact:
RPM Innovations, Inc.
333 Concourse Drive
Rapid City, SD 57703
605-348-0555
sales@rpm-innovations.com
www.rpm-innovations.com