




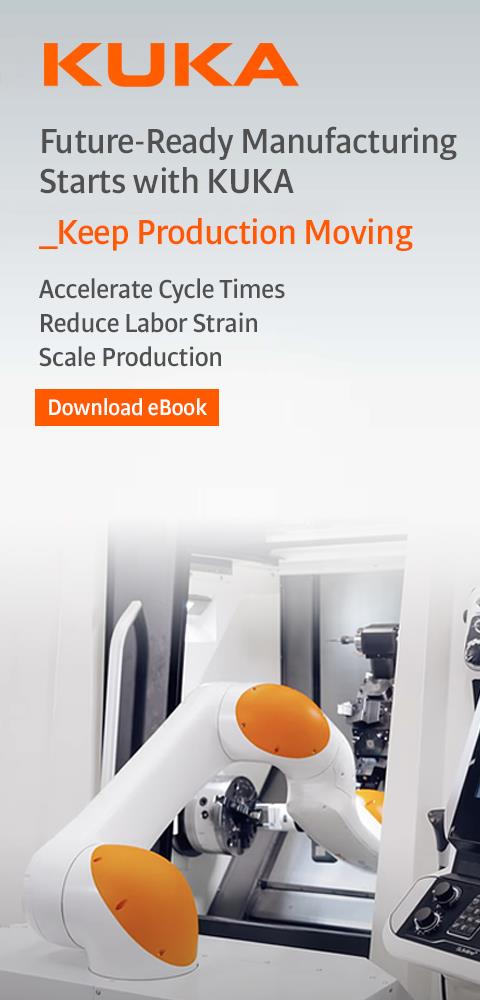
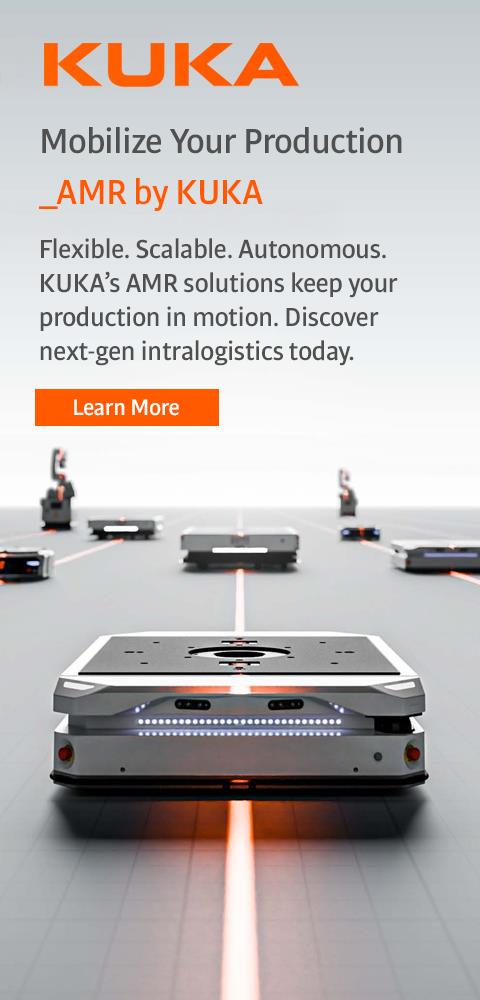
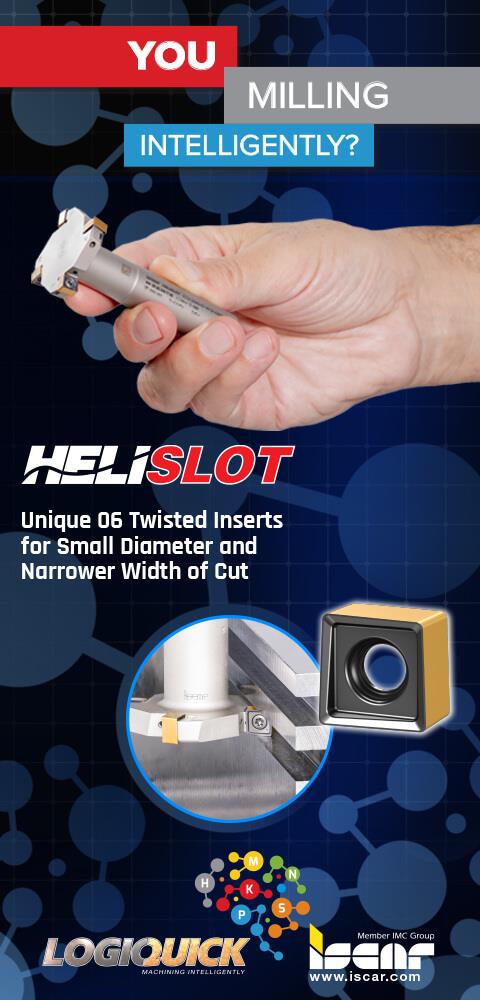
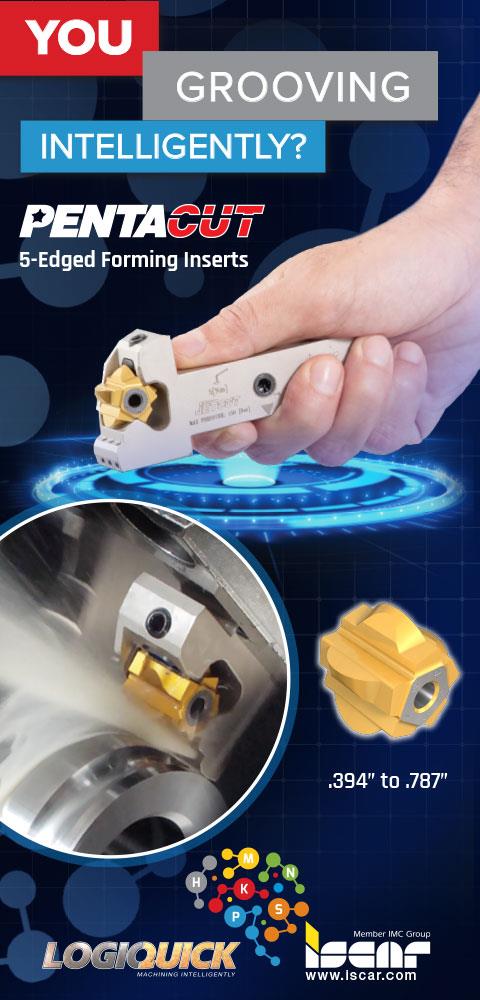
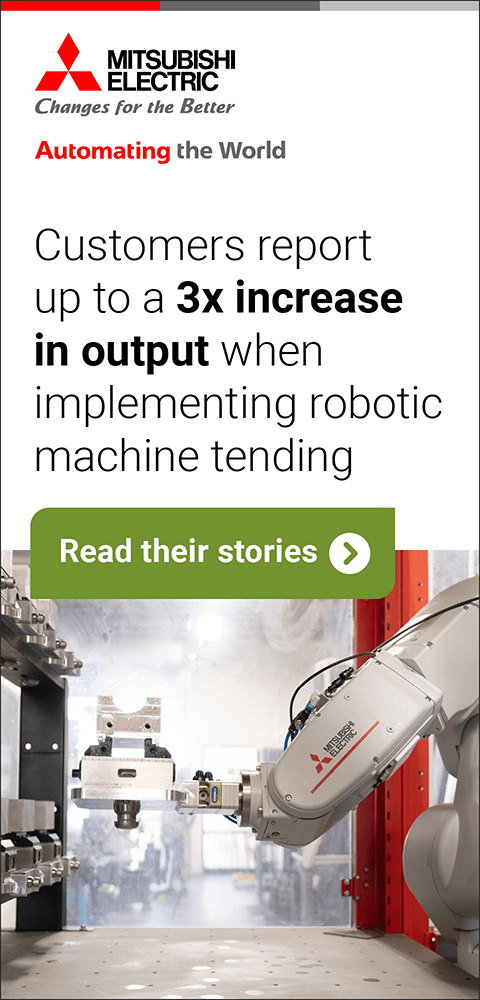
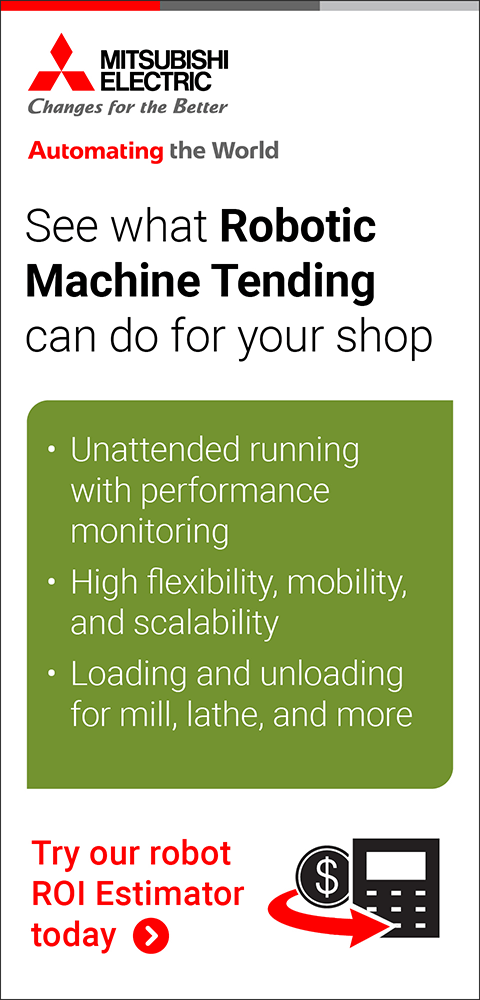
End-to-End Tire Plant Solution
March 1, 2016
Cimcorp, a manufacturer and integrator of turnkey robotic gantry-based order fulfillment and tire-handling solutions, has announced the expansion of its Dream Factory solution to include the handling of raw materials and compound products. "The end-to-end solution includes an optimized layout design that utilizes 50% less floor space than conventional solutions, can be integrated with specialized software systems and generates cost savings of up to 50% in materials handling capital investment by simplifying the material flow," said a company spokesperson.
"The acquisition of Cimcorp by warehouse management and distribution specialist, Muratec, enabled the addition of key upstream components to the Dream Factory solution," said Kai Tuomisaari, Vice President of Sales and Projects, Cimcorp. "Muratec's warehousing and transportation technologies are now fully integrated with Cimcorp's systems, including a user-friendly interface for operators, to provide seamless data access throughout the entire manufacturing process."
The Dream Factory solution is designed for both brownfield and greenfield factory sites, with the original version already implemented around the globe.
In the new Dream Factory, Cimcorp's gantry robot technology and material handling specialty software - a combination of warehouse control software (WCS) and manufacturing execution systems (MES) - provide benefits that include:
- Total control of the manufacturing process at each stage
- Real-time data for production and inventory management, including 100% availability of raw materials, compounds, components, green tires and finished tires at each point in the manufacturing process
- Optimum utilization of the most valuable process machinery, such as building machines and curing presses, to secure crucial increases in production capacity
- Streamlined material flow that allows plant managers to minimize buffering and maximize production efficiency
- Reduced buffer storage and therefore minimized work in process (WIP)
- Minimized capital investment for greenfield sites through optimized layout design
- Efficient use of space and increased capacity within given building constraints in brownfield sites.
For more information contact:
Cimcorp Automation Ltd.
635 South Service Road
Grimsby, Ontario L3M 4E8
CANADA
905-643-9700
sales_na@cimcorp.com
www.cimcorp.com
< back