
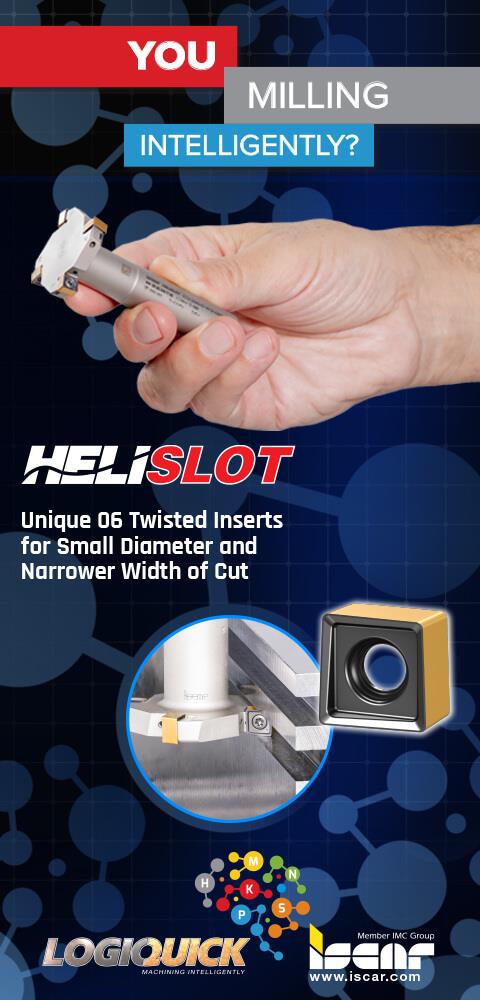
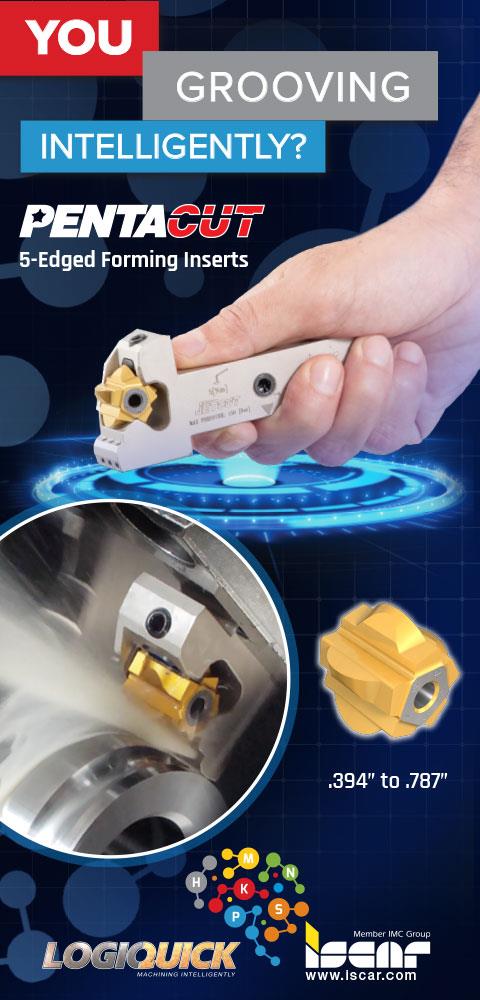
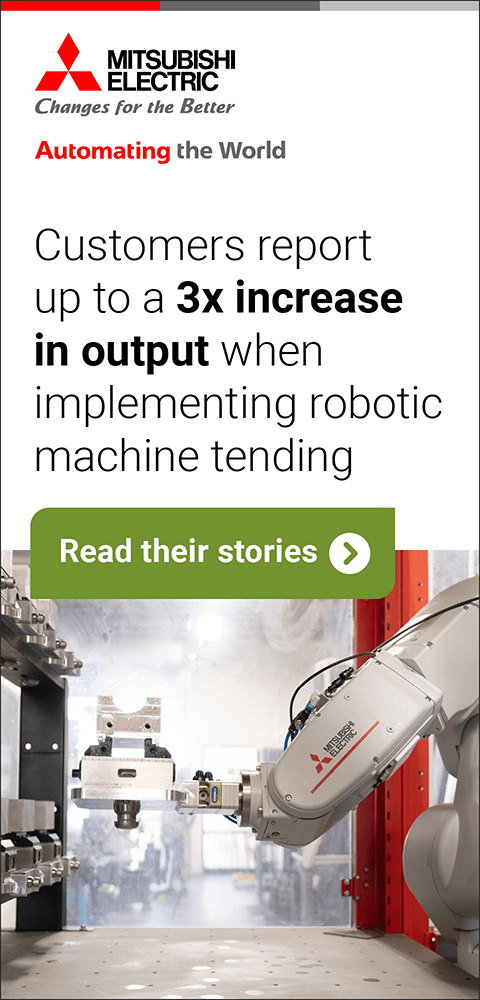
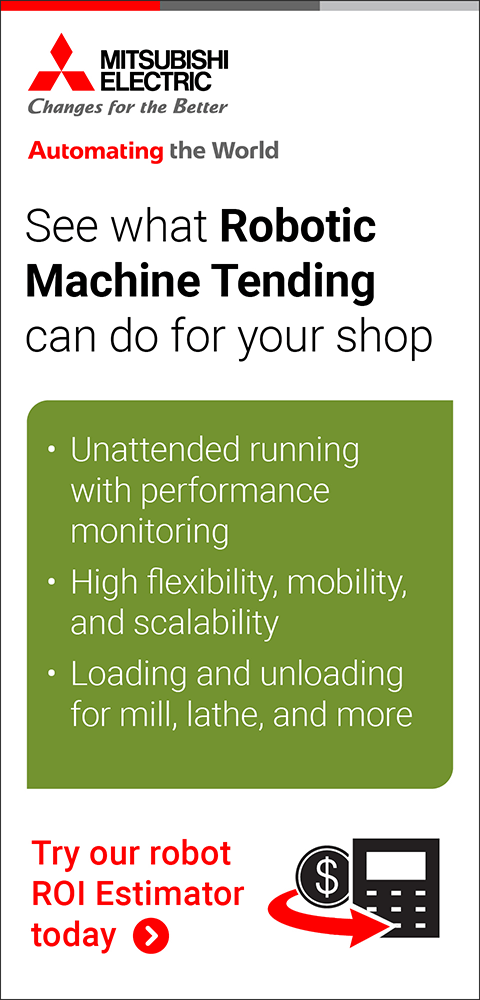




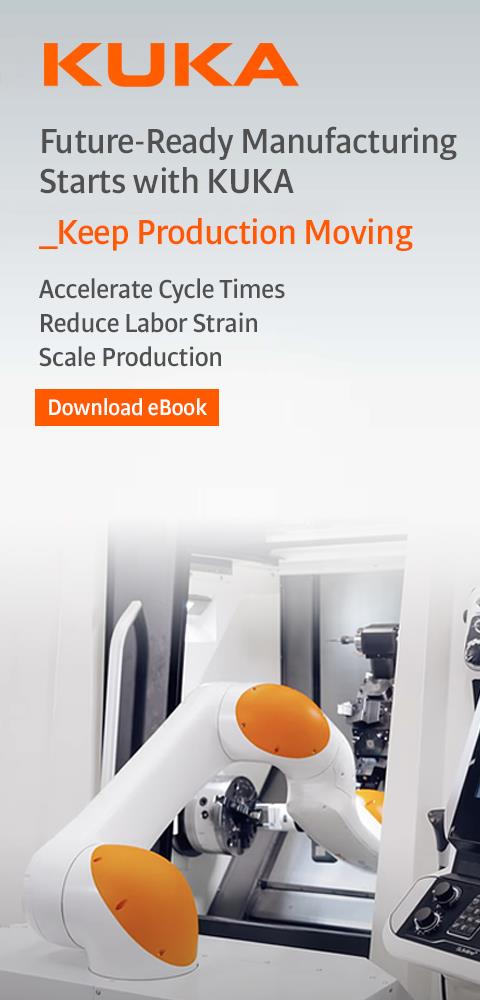
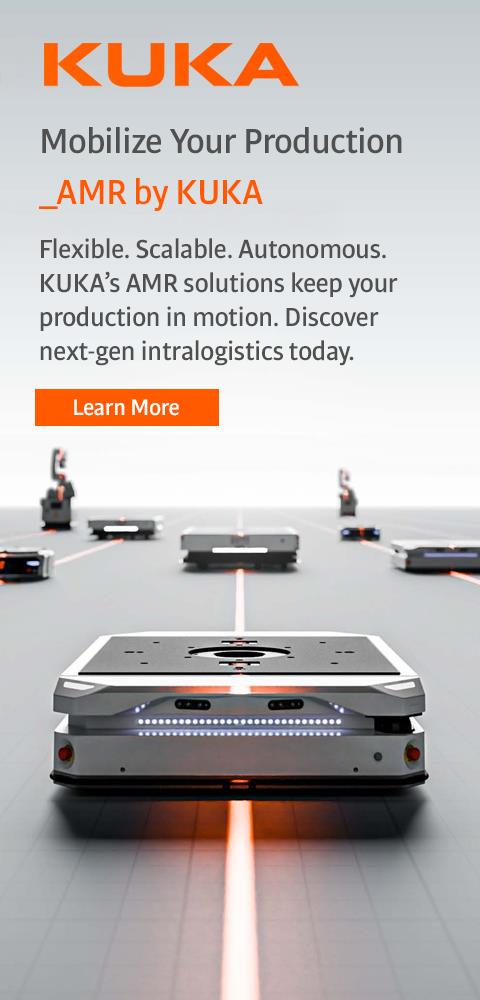
Updated Chip and Scrap Removal Conveyor
March 1, 2016
The MunchMan II from Jorgensen Conveyors is built to manage the long stringy and bird's nest chips generated by high speed turning and milling operations.
The MunchMan II employs a twin-stacked conveyor arrangement at the lower curve and through the incline and chip discharge of the system. The primary and secondary belts run in opposite directions to grab hold of chips, compact them and securely carry them up steep inclines, designed to eliminate the risk of conveyor jams caused by chip balls tumbling back down the conveyor.
Jorgensen's patent pending drive system allows just one gear motor to run both drive shafts. Jorgensen's exclusive UVS Ecologic Conveyor Control with JamManager automatically reverses to clear jams.
"The physical effect of two cleated moving belts compressing and moving the difficult long stringy chips and larger chip volumes is noticeable when compared to traditional single belt conveying systems," said Friedrich Bitterwolf, Director of Engineering.
The MunchMan II can be designed to effectively fit into most of today's CNC lathes and machining centers.
For more information contact:
Jorgensen Conveyors, Inc.
10303 N. Baehr Rd.
Mequon, WI 53092
262-242-3089
info@jorgensenconveyor.com
www.jorgensenconveyors.com
< back