


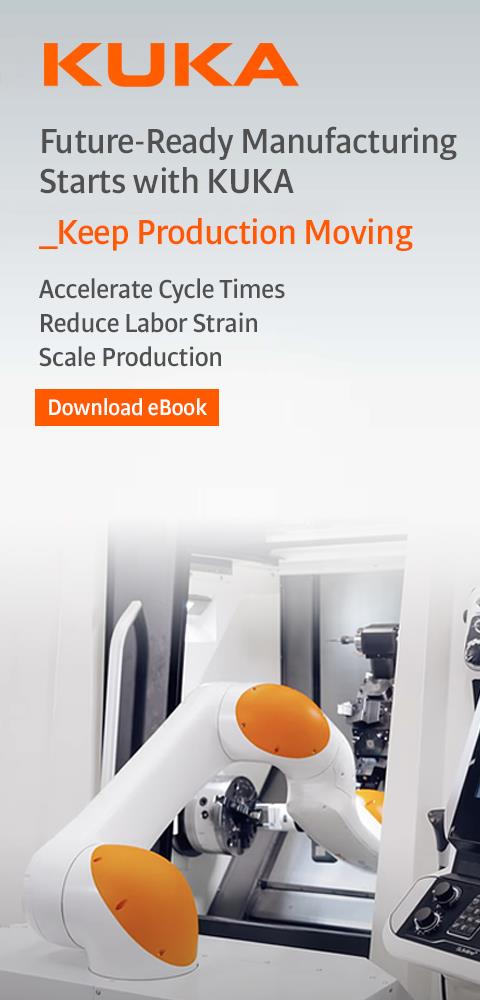
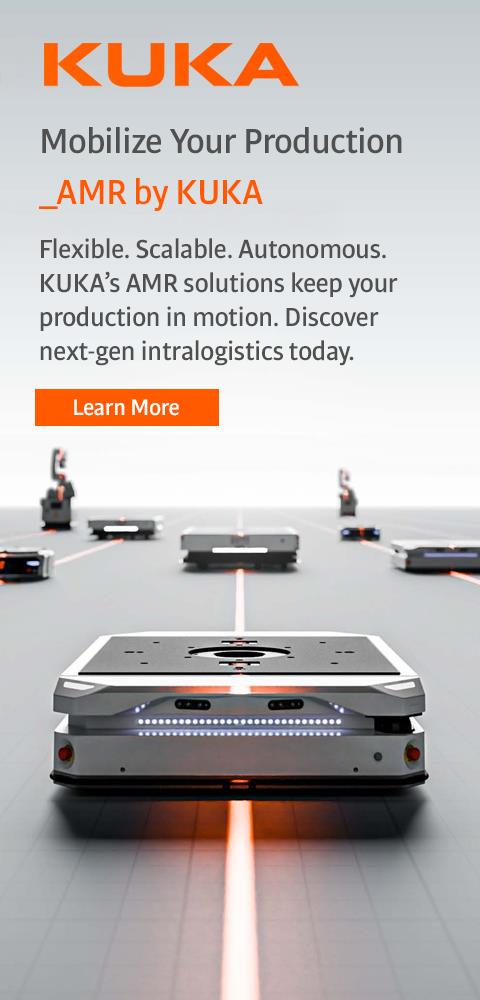
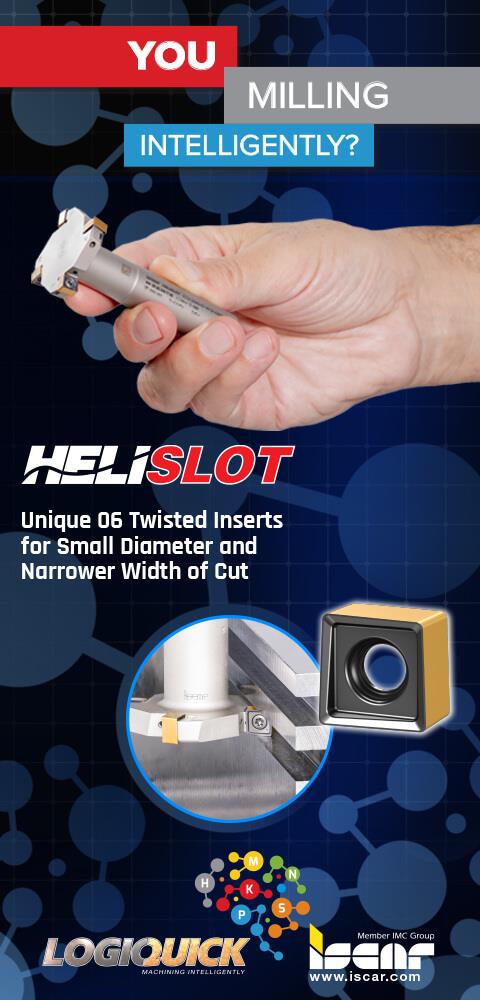
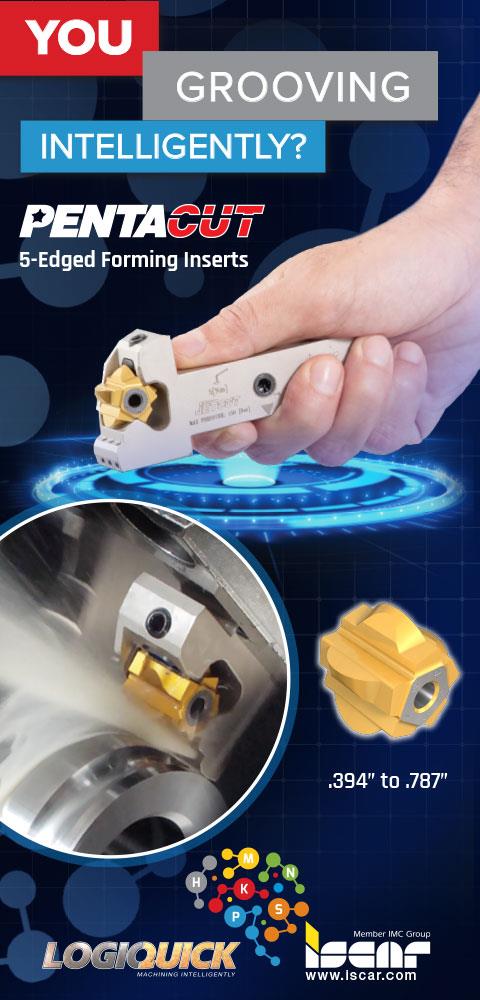
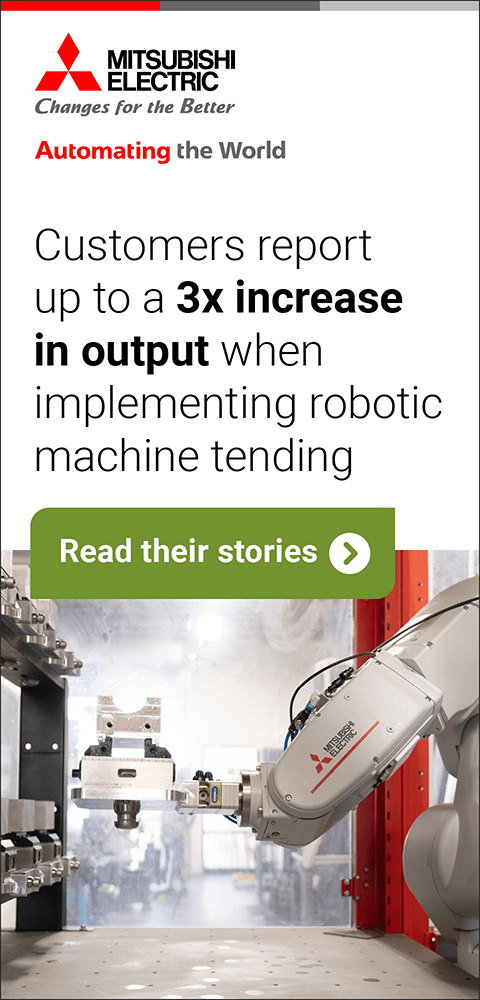
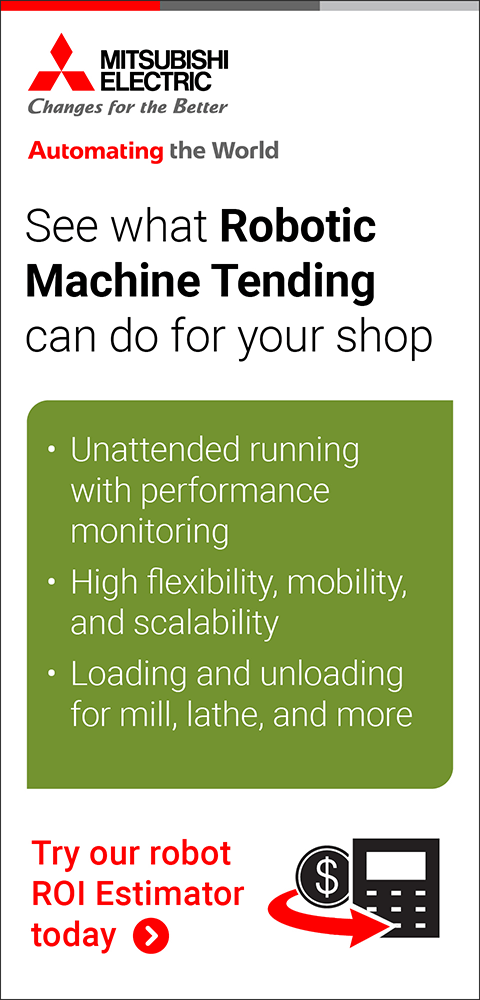


Decoding Algorithms for Barcode Readers
March 1, 2016
Microscan has announced the availability of improved X-Mode 4.0 decoding algorithms with its newly released MicroHAWK barcode reader platform.
Microscan's X-Mode products feature decode algorithms for enhanced symbol location, analysis and reconstruction right out of the box. X-Mode algorithms are engineered to decode any symbol (1-D linear, 2-D or direct part mark) regardless of condition. Advanced pixel analysis and logic render damaged, distorted, poorly printed or skewed symbols readable using image processing to prevent data loss. For codes marked directly on parts, like dot peen marks on highly-reflective metal surfaces or inkjet codes printed on cardboard, X-Mode automatically enhances symbol appearance to gather critical symbol data and interpret codes in both static and dynamic applications. X-Mode offers omnidirectional decoding of any symbol, increasing the range of mounting angles that can be used to position a barcode reader within a piece of equipment or on a manufacturing line. When symbol quality, mark contrast, substrate integrity or read direction cannot be predicted, X-Mode algorithms are designed to safeguard the efficiency of operations and read every code.
With the release of its MicroHAWK platform, including three new barcode imagers and the WebLink browser-based set-up interface, Microscan has re-engineered and improved X-Mode functionality in X-Mode 4.0. This update adds new capabilities for solving specific decoding issues gathered through field data from customer barcode reading applications. With poor print consistency and permanence of inkjet on labels a persistent obstacle, X-Mode 4.0 now addresses incomplete and obscured Code 39 and Code 128 linear symbols through a new Damaged Mode. Damaged Mode fills in white gaps in a symbol's bar elements caused by low ink or damage, thereby rendering complete, connected bars for decoding. Damaged Mode can also accommodate high-density, out-of-focus symbols for camera-based imagers that have inadequate resolution, or are mounted at variable or improper distances for the target code type.
In addition to Damaged Mode, X-Mode 4.0 includes Train and Optimize modes available as tools in the WebLink User Interface. From WebLink, users can click on the Train button to command a MicroHAWK barcode reader to search for the ideal combination of decoding parameters for the target symbol. Train Mode accesses an image characterization library of known code types and their optimal decoding parameters to apply parameters from similar symbols to the target symbol to boost reading power. Train Mode also enhances decoding for Data Matrix symbols with limited quiet zone (the required blank space surrounding the code) and adds support for challenging QR Codes like those marked or printed on noisy backgrounds. The Optimize button in WebLink is used to increase decode speeds by limiting processes run by the barcode reader to only those processes needed to read the target symbol. Other general improvements include enhanced decoding for direct part marks with obscured or incomplete code edges, increased tolerance of lighting variations (including speckled light reflected inside the symbol) for Data Matrix symbols, and improved detection of the clock or L-pattern of rotated or obscured Data Matrix symbols. With a 5-megapixel QSXGA sensor option available for all new MicroHAWK barcode reader models, X-Mode 4.0 also offers support for 5 MP barcode imaging.
For more information contact:
Microscan
700 SW 39th Street, Ste. 100
Renton, WA 98057
800-762-1149 / 425-226-5700
info@microscan.com
www.microscan.com
< back