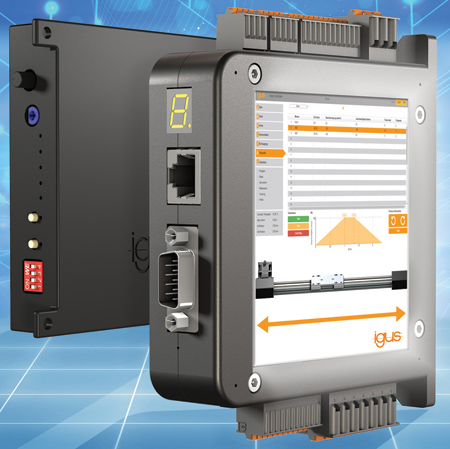
With the D3 and D1 dryve motor control systems, motorized linear and rotational axes can be automated easily without any programming.
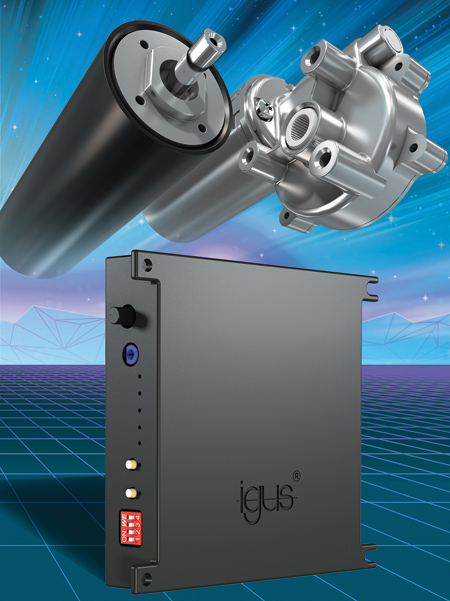
D3 dryve control system for DC motors
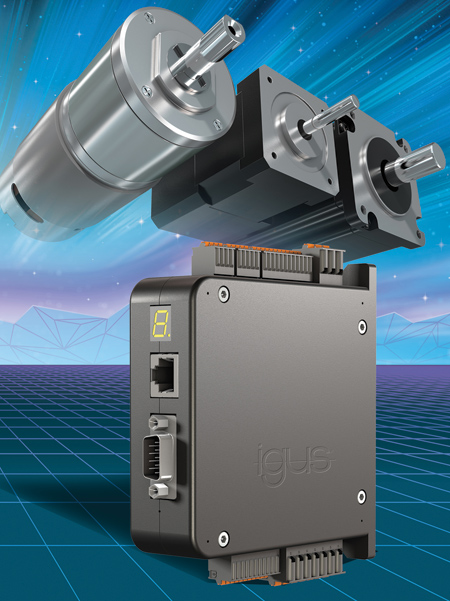
The D1 dryve control system can be used to automate single-axis drives, multi-axis linear robots, delta robots or pick & place applications. It can be used to control stepper motors, DC motors and EC/BLDC motors.
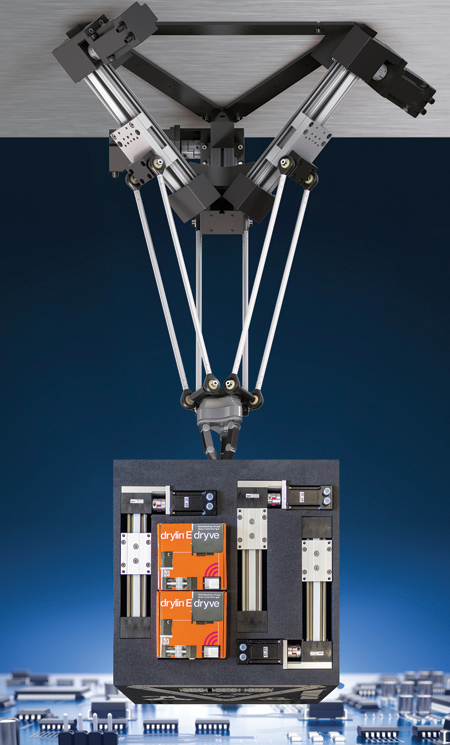
The D1 dryve is used for the delta robot. "Simple tasks can be automated quickly and cost-effectively even without any programming knowledge," said a company spokesperson.
igus has developed two cost-effective control systems designed to help users from all areas of industry to quickly start up their motorized drylin E drive axes.
The D3 dryve controls simple linear or rotations axes with DC motors without any software or a PC. For more complex travels, such as with multi-axis robots or delta robots, igus offers the D1 drive, which is a control system for stepper motors, DC motors of EC/BLDC motors. The motor control system can be modified live or simply operated via a web browser.
Depending on the process, the customer is supplied with the axis or linear robot that will best meet their requirements. With drylin E, users can deploy the already-configured self-lubricated linear or rotational axes, which are ready to install and can be motorized in different installation sizes as a single axis, or a linear robot structure in the case of format and height adjustment systems or pick & place applications.
For easy control and operation of the axes, igus' D3 dryve offers users a motor control system for simple movement, and the D1 dryve, a motor control system for more complex tasks. This allows a variety of tasks to be automated without the need for advanced programming.
D3 dryve: Quickly Set, Directly Automated
The D3 control system was developed to perform simple tasks quickly and cost-effectively. The control system is designed for all standard DC motors. "When developing the D3 dryve, we mainly focused on enabling a simple, user-friendly start-up for anyone," said Rene Erdmann, Head of Business Unit drylin E Drive Technology.
No licenses or software are needed for installation of the control system because all functions have been integrated into the device directly. Simply connect the control system to a 24V power supply and set the operating mode, end-position switch-off and the motor current via DiP switches. The speed can be adjusted with an integrated rotary controller. Current-limiting is done by means of a screwdriver with another controller. Once made, the settings are permanently stored. An LED display indicates the current status of the control system to the user via various colors.
External switching elements such as joysticks can be easily connected to the control system. Private individuals, as well as small and medium-sized enterprises and universities, can use motorized drives for automation without prior programming knowledge.
The D3 dryve control system is used in camera guidance systems, in furniture manufacturing for drawer push-out mechanisms, or for changing the position of monitors. In large industries, the control system is suitable for very simple automation tasks. "Where very simple positioning tasks with a low cycle rate are concerned, or also in the case of railway point-switching mechanisms, the D3 dryve can be used without any problems," Erdmann said.
Where it is necessary to automate more complex tasks for multi-axis linear robots, delta robots or pick & place applications, users can deploy the intuitive D1 dryve motor control system. The control system is suitable for all stepper motors, DC motors and EC/BLDC motors.
igus motors, as well as motors of other manufacturers, can be easily controlled using this control system. The control system can be operated without downloading any software, but via a web browser from a fixed PC or a mobile device such as a smartphone or tablet-all without an internet connection. The user only needs a wireless router if mobile devices are used. A clear interface helps the customer with the correct parameterization and again, as with the D3 dryve, no programming knowledge is needed.
"A motor-operated axis, together with the D1 dryve control system, can be started up in a few minutes due to its user-friendly interface," Erdmann said. "Afterwards, the values can also be changed, or intermediate steps can be added easily via the web browser. A time-consuming transfer of data backwards and forwards is unnecessary, and this saves money once integration has been completed."
D1 dryve: Intuitive Interface for Speedy Set-Up
The user interface of the motor control system is called up via a web browser and IP address. There are seven menu items for the user to alter the settings. Different languages can be selected for the control system, and it can be protected with a password login. Configurations that have already been created can be easily uploaded to the motor control system. As a result, the time needed for the start-up of a delta robot is shortened.
The "motor" menu item is used to load all the settings into the control system after the igus article number has been entered. Where motors of other suppliers are concerned, the user must only amend the settings according to their datasheet. The user can also use the menu to enter the settings for the linear or rotational axis as well as to set the route and feedrate.
The travel profiles, which can be altered live, are mainly what simplify the motor control system at its center. Time-saving automation without transfer or loading processes is therefore possible. Networking with a higher-level control unit such as a PLC is also possible via Ethernet or CANOpen. In addition, an oscilloscope has been integrated into the web face in order to monitor the performance of the motor. It shows live values relating to motor current, speed, actual position and setpoint position.
An advantage of the D1 dryve is the networking capability of the control system. The control system has intentionally been designed to save space. It can be easily mounted on a top-hat (DIN) rail in switch cabinets and controlled via fixed wiring.
Alternatively, the D1 can be connected to a wireless router, after which the system can be controlled wirelessly. The integrated web server does not require any further software on the operating devices, nor does it need additional storage media. This means that users do not incur additional costs.
Another feature of the D1 dryve is the integrated closed loop mode. While in open loop mode, the stepper motor is set so that it safely moves the maximum necessary load but wastes energy when subjected to low load, whereas the closed loop ensures current control that matches the actual performance. The consequence of this energy adaptation is that, due to the current being regulated according to performance (actual load moved), high loads are moved quickly with a lot of energy and low loads are moved slowly with little energy.
In addition, the motor does not consume any energy at a standstill, in contrast to the open loop mode. An additional advantage is that due to efficient current control, there is less heat loss in the motor thus keeping it cooler.
The D1 dryve is already being used for the igus delta robot. The robot is based on three maintenance-free drylin E ZLW toothed belt axes with stepper motors, self-lubricating igubal coupling bars and matching adapter plates. The stepper motors with encoders provide fast handling of up to 1 kg with a precision of ± 0.5 mm.
The delta robot is available in two sizes, with a working space diameter of 360 mm or 660 mm. The complete system can carry up to five kg at low speeds. Three D1 dryve control systems provide quick and easy set-up of the automation solution. One configuration per axis is sufficient. This can be stored and directly transferred to the other two control systems. The delta robot can therefore be started up in just a few minutes.
To give prospective customers an opportunity to test the D1 dryve control system for themselves, igus offers its customers an online simulation at www.igus.com/dryve. Here, the customer can change the values of the control system and experience the effects on a live animated axis. Another service offered is the igus Learning Channel on YouTube. It helps the user with short video clips of the fast and simple installation and parameterization of the D1 and D3 dryves. Both control systems are available from stock within 24 hours.
For more information contact:
igus, Inc.
P.O. Box 14349
East Providence, RI 02914
800-521-2747
sales@igus.com
www.igus.com