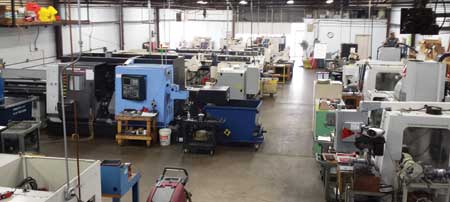
Progressive Turnings' low quantity production department.
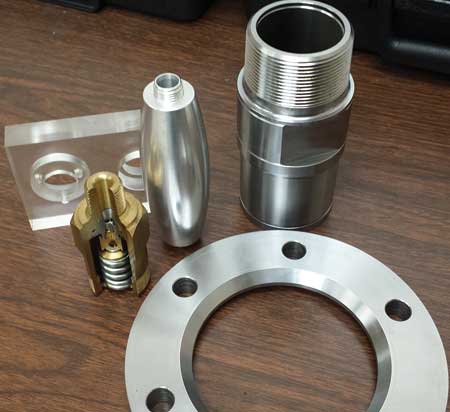
Various parts made of brass, 303 stainless, aluminum, etc. These were machined on the company's Doosan TT1800SY and Doosan LYNX chucking machines.
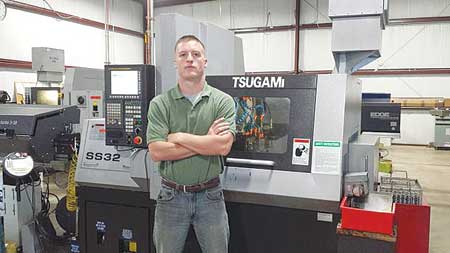
Luke Niels, Plant Manager and third generation employee at Progressive Turnings, with the Tsugami SS32. Niels manages the day to day operations in the plant and is also lead programmer for all the machines (Miyano, Haas, Doosan and Tsugami).
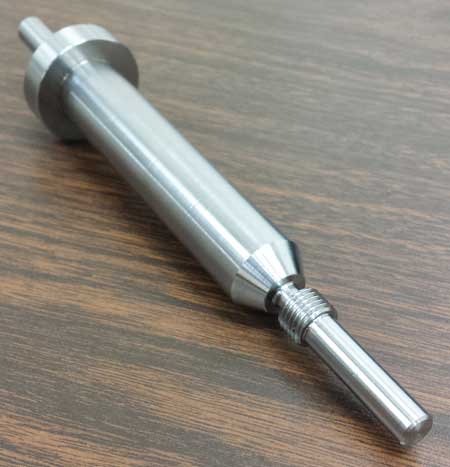
The Tsugami SS32 is used for high quantity production runs of components, such as this 7" long 17-4 SS medical part.
An increase in orders led Progressive Turnings, Inc. to increase production efficiencies, improve lead times and has become a model of a 21st century shop.
"We had a large family of parts for one of our largest customers," said Luke Niels, Plant Manager, Progressive Turnings. "These were parts that we had been running for years, and the amount of part numbers and quantities was steadily rising. The parts took three to five operations each to manufacture. Also, our company focus was changing toward a more efficient 'one operation = complete' theory to coincide with our lean initiative and continual improvement projects."
After consideration, the company decided that in order to manufacture an array of parts, complete with little or no detailing or additional operations, sub-spindle machinery with Y-axis and live tools would be needed.
"We contacted Scott Hauser with Morris Midwest and checked out some Tsugami CNC Swiss-style lathes," said Niels. "When we saw them, we were impressed. First we bought a BE 20 and then SS32s. Now we have four Swiss-style lathes and they have not stopped producing since installation about three years ago. Also in this same time frame we bought a Miyano BND51S for our larger diameter parts. In October of 2012 we purchased a Doosan TT1800SY for parts over 2 inches in diameter. We chose these machines due to their ability to finish complex parts in one operation. They are all multi-axis CNC lathes with live tooling and they are all our busiest machines since they hit the floor. We are currently planning our next two machine purchases."
According to Niels, the solution is working great. "We are running seven days a week, every week on these machines," he said. "Our challenge was definitely solved with the sub-spindle and live tooling technology of these new machines. Our on-time delivery and quality has never been better and we are now able to run more complex jobs with one set-up." The machines all feature high pressure coolant, live tools and spindle speeds of up to 8,000 RPM.
"For more complex machinery, the set-up may take a bit longer, but when you are only doing one set-up as opposed to three to six set-ups, the total shop set-up time is drastically reduced," said Niels. "Also, we are only utilizing one machine rather than several machines to make the same part. In-process time is greatly reduced. We always do in-process inspection and first-piece approval prior to production. If we ran a six-operation part, we would process the part six times. When you only have one set-up, this is only done once. The finished product is superior in one operation. If you want to produce scrap, process and re-process the parts throughout your entire shop several times - this is a good start of producing scrap very inefficiently. We are doing the opposite of this and it is working great for us. We are running a consistent 97% on time and 98% defect-free. We have been implementing many changes with our lean initiative but the sub-spindle machinery is an amazing improvement."
Founded in 1979 by Dave Niels and Larry Niels, Progressive Turnings specializes in precision machining of hydraulic components, aerospace components, medical components and more. Materials used include 300 series stainless steel, aircraft grade aluminum, leaded and non-leaded alloys, plastics, exotic steels and more. The company provides precision machining on CNC lathes and machining centers and utilizes Solidworks and Esprit software. It also provides Production Part Approval Process (PPAP), Statistical Process Control (SPC) and several other types of data collection and statistical quality control methods.
"Our goal is to have our on-time delivery at 100% and be 100% defect-free," said Niels. "We want to be one of the most sophisticated, modern shops in the U.S. Our philosophy is simple: we want to partner with our customers and be an extension of their company by providing them with the best manufactured precision components for their industry."
For more information contact:
Luke Niels, Plant Manager
Progressive Turnings, Inc.
1680 Mountain St.
Aurora, IL 60505
630-898-3072
luke@progressiveturnings.com
www.progressiveturnings.com