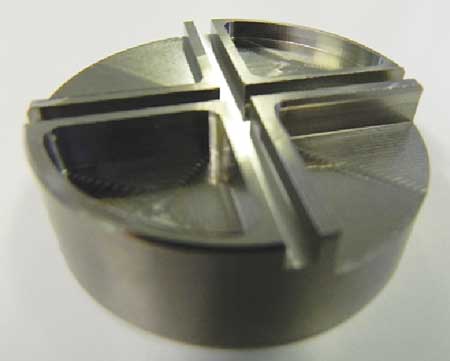
CrazyMill Cool for milling slots, pockets and ribs.

CrazyMill Cool offers integrated cooling in a small diameter range (from 0.3 to 6 mm).
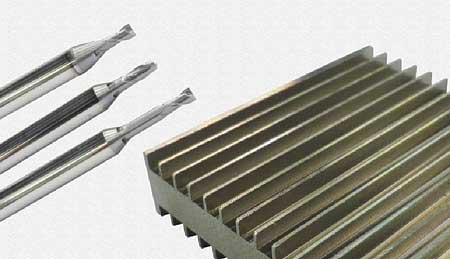
Three versions of CrazyMill Cool are available for different milling depths.
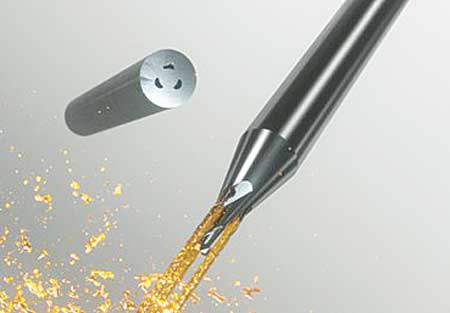
Machining stainless steels can be a challenge. One reason is that the tool becomes extremely hot due to the poor heat conductivity of the material and thus wears and can be damaged quickly. Other machining factors include efficiency and surface quality. To meet these challenges, Mikron Tool SA Agno has developed CrazyMill Cool, a solid carbide endmill with through coolant capability, in diameters from 0.3 mm to 4 mm (0.02" to 0.15"). "Slot or pocket milling into solid material and contour milling are its strengths," said a company spokesperson. "The tool combines roughing and finishing while providing high efficiency, long tool life and improved surface quality."
The mill is comprised of a newly developed micro granulate carbide designed to provide hardness as well as toughness. According to the company, a robust cutting body, a radial relief and a specific cutting edge preparation produce high cutting edge quality and stability. Also important for tool life is the coating, which is specifically designed for hard to cut metals. "With a low friction coefficient and a reduced affinity with steel, build up at the cutting edges is avoided," said the spokesperson. "Furthermore, the coating has a high oxidation resistance and heat hardness. This helps to maintain the temperature in the green range and 'burning' of the cutting edges is avoided, which in turn enhances tool life and surface quality."
Generally, dry machining is not possible with stainless steels. "Due to the poor heat conductivity of the material, the tool would become extremely hot and the cutting edges burn out," said the spokesperson. "The use of a coolant is a must. Mikron's microcutter has three to four internal coolant channels that go through the shaft and carry coolant along the diameter to the cutting edges. The result is a targeted and massive cooling effect where it is needed: at the cutting edges - and this in every machining position. Simultaneously, chips are continuously flushed away from the milling area. In relation to the small diameters of the milling cutters, the cooling channels are rather large. The friction heat is substantially absorbed and removed by the coolant. No special requirements are necessary for filtering and coolant pressure. These tools can also be used profitably on conventional machines.
"Up until now, an infeed of 0.1 - 0.2 x D was recommended to mill a channel into solid material. The CrazyMill Cool is able to achieved depths of 1 - 1.3 x D directly."
"With up to five times faster cutting speed and a comparable feed, the efficiency of the milling cutter is improved by a factor of 10 to 20," said Markus Schnyder, Mikron Tool International. "Additionally, even though the cut goes into solid material, the CrazyMill Cool features Rz values two to three times better than what can be expected from conventional cutters."
A complete inventory of small, standardized milling cutters will be available for applications in industry segments such as watch-making, medicinal and surgical technologies. A first series of small, cylindrical cutters in diameters of 0.3 mm to 4 mm (0.02" to 0.16") has been launched. A short version for maximum depths of 1.5 x D, a medium version for 3 x D and a long version for 5 x D are available. All of these have a cutting head of 1.5 x D.
For more information contact:
Mikron Corp. Monroe
200 Main Street
Monroe, CT 06468
203-261-3100
mmo@mikron.com
www.mikron.com