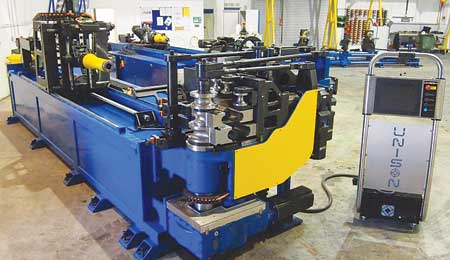
Unison's all-electric bending machine featuring mechanical architecture and control software improvements is designed to reduce tubular part fabrication times.
Horn Machine Tools offers Unison's all-electric bending machine featuring mechanical architecture and control software improvements designed to substantially reduce tubular part fabrication times.
"The redesign reduces the time required for all the intermediate handling and movement of the tooling configuration tasks the machine performs before and after a bend by as much as 40%," said a company spokesperson. "As there might be four or five such auxiliary movements for each bending move, as well as changes of tooling dies, these savings can add up to very large productivity gains - particularly for companies fabricating tubular parts with several bends."
The machine architecture will now be fitted as standard on all of Unison's all-electric bending machines, which are available for tube/pipe diameters from 5/8" to 8.5".
"The reductions in bending cycle times come from two main aspects," said the spokesperson. "The shape and size of all of the machine's auxiliary mechanical axes have been optimized to reduce their mass and inertia. By applying more torque, these axes are also being driven at faster speeds, accelerate and decelerate at faster rates and achieve higher top speeds. This use of higher torque does not increase machine cost, as Unison utilizes the peak output characteristics of its servomotors to deliver the torque for the tiny fractions of time required."
On some of these axes, Unison has also improved the mechanical dynamics by changing the type of gearing mechanism employed. The design of the main bending arm axis of the machine remains as it is, as the speed of the tube bending task itself is almost invariably limited by the characteristics of the material being bent.
"Higher productivity is important for virtually every tube bending machine user, but wherever production is in high volume - such as in the automotive or furniture manufacturing sectors for example - the gains can be very significant," said Unison CEO Alan Pickering.
For more information contact:
Lee Sanchez
Horn Machine Tools
Unison North America
40473 Brickyard Drive
Madera, CA 93638
559-431-4131
sales@hornmachinetools.com
www.hornmachinetools.com