
Small-Diameter, High-Feed Endmill
November 1, 2015
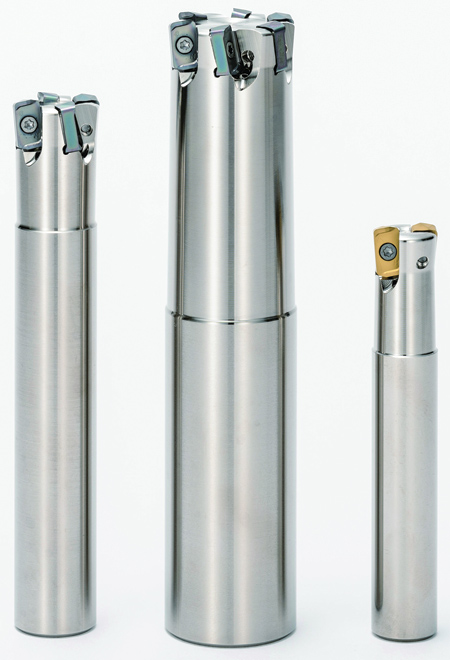
The MFH-Mini is available in cutting diameters ranging from 0.625" to 1.250".
Kyocera Precision Tools, Inc. has introduced the MFH Mini, a small-diameter, high-feed endmill for processing metal parts.
Development Background
A high-feed endmill is a cutting tool utilized to rough-cut the surface of metal across a broad area. The insert requires high cutting capability that allows for quicker and more stable processing of the workpiece. Kyocera reports that to meet these needs, it developed the MFH-Raptor, a high-efficiency, high-feed cutter, in 2014. After its introduction, to support higher-precision cutting technology required for processing molds, Kyocera developed the small-diameter, high-feed MFH Mini endmill.
The MFH Mini
The MFH Mini is a small-diameter, high-feed endmill for rough processing consisting of a newly developed insert and dedicated holder. "The insert features a design that reduces impact on the insert when making initial contact with the workpiece, thus achieving smooth cutting with low resistance," said a company spokesperson. "As a result, the product reduces chattering and enables increased feedrates. In addition, the MFH Mini exhibits high chip evacuation due to the design of the newly developed chipbreaker."
This product is available with both a CVD and PVD coated insert. Utilizing an insert with the suitable coating based on work material characteristics enables the endmill to deliver optimal wear and fracture resistance.
New Product Features
- Low resistance: "Designed specifically for small-diameter, high-feed endmills, the insert enables smooth cutting with low resistance by applying a uniquely-shaped edge developed to cushion initial shock at the moment of workpiece contact - the onset of cutting. The new insert also improves chip evacuation problems that typically occur when slotting and pocketing and improves stability, contributing to high-efficiency processing," said the spokesperson.
- New insert reduced cutting resistance: "The new low-resistance insert reduces cutting resistance and chattering. This enables high-efficiency, high-feed processing for applications including small machines (BT30/BT40) with increased feedrates. The MFH Mini also delivers high economic efficiency through its double-sided, four-edge negative insert," said the spokesperson.
- Applicable to multiple types of processing and work materials: The newly developed LOGU insert with the GM chipbreaker is suited for face milling, shouldering, contouring, slotting, pocketing, ramping and helical milling required for mold processing and other applications. "Moreover, the insert material exhibits increased wear- and fracture-resistance when the company's unique CVD / PVD coating is applied to the insert's high-toughness, cemented carbide base material," said the spokesperson. This enables the processing of various materials ranging from general and mold steels to traditionally difficult-to-cut materials such as Ni-based heat-resistant alloys.
For more information contact:
Kyocera Precision Tools, Inc.
102 Industrial Park Road
Hendersonville, NC 28792
800-823-7284
cuttingtools@kyocera.com
www.kyoceraprecisiontools.com
< back