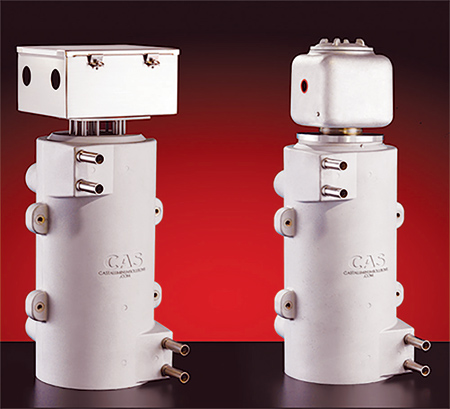
The CAST-X 4000 from Cast Aluminum Solutions. The unit features dual 1-inch O.D. (2.5 cm) flow-path tubes, and is capable of heating liquids or gases.
Cast Aluminum Solutions (CAS), provider of circulation heaters for the paints, coatings, adhesives and solvents markets, has launched the new CAST-X 4000 Circulation Heater.
The no-contact design (also called indirect heating) means the fluid being heated never touches the heating elements. It stays in a clean flow-path tube. This is an important safety feature, especially for flammable fluids. The CAST-X 4000's design also reduces contamination. Fluids stay in the flow-path tube and do not contact other components in the heater.
The CAST-X 4000 was designed specifically for high-throughput processes, such as paint manufacturing, mixing of adhesives and coatings and final application of these chemistries by the various end-users (large manufacturing facilities).
Available with several volt, watt and circuitry options, they can be customized to fit any fluid processor or end-user. For applications involving hazardous liquids, the CAST-X 4000 can be equipped with an explosion-resistant housing.
The CAST-X 4000 features dual 1-inch O.D. stainless steel, spiraled wound tubes (through which the liquids flow), cast into an aluminum mass, which also contains the heating elements. Delivering up to 60 kilowatts of power, the CAST-X 4000 supports liquid flowrates up to 36 gallons per minute. To accommodate high-pressure applications, the CAST-X 4000 is available with Inconel flow-path tubes. Electro-polished tubes and passivated tubes are also available.
"The CAST-X 4000 follows the design of our smaller CAST-X heaters, a no-contact, small-footprint design, reliable and self-draining, requiring very little maintenance. It has the capacity to meet the needs of large-volume fluid processors," said Eric Hostert, Director of Engineering at CAS.
For more information contact:
Jeffrey Awe, Marketing Director
Cast Aluminum Solutions
1310 Kingsland Drive
Batavia, IL 60510
630-879-2696
jawe@castaluminumsolutions.com
www.castalumimumsolutions.com