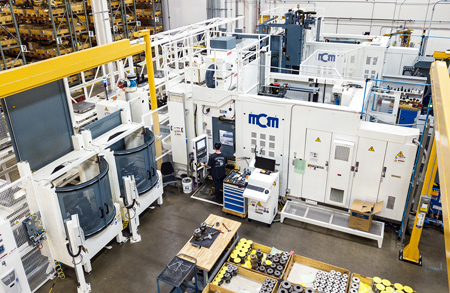
Left hand view of FMS, showing the two load/unload stations and the first Clock 1200 HMC.
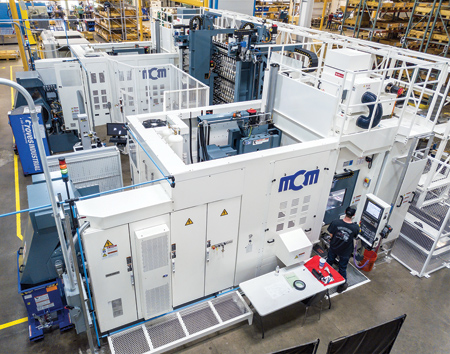
Right hand view of FMS, showing the recently installed second Clock 1200 HMC with all 24 pallet storage locations installed.
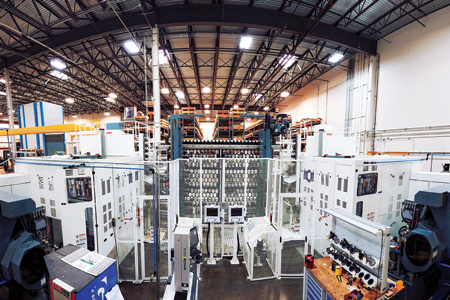
Shown are both tool magazines connected and positioned between the two machines so the tooling can be shared.
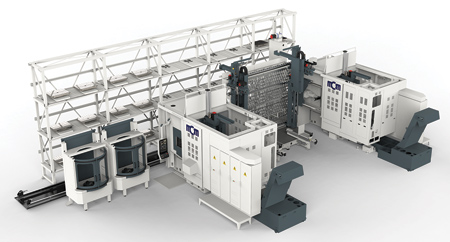
The original design showing the cell to Samson (note: this shows pallets stacked three high, but the actual cell is stacked two high).
SAMSON Controls Inc. needed to quickly produce high quality parts with exacting tolerances. A flexible manufacturing system (FMS) was necessary in order to meet the company's high mix, low volume manufacturing requirements.
A Unique Challenge
SAMSON develops and manufactures control equipment for industrial processes. The products are tailor made for the specific requirements of each application, and range from rugged, self-operated regulators to highly specialized control valves. They are manufactured in all common sizes in both standard materials and exotic alloys and are equipped with various actuators.
The pressure bearing components, including valve bodies and bonnets, are produced as castings and/or forgings. They are generally precision machined completely in one to two milling operations, although SAMSON also performs turning, grinding and polishing for some applications.
Due to the high variability requirements of the product range, SAMSON needed a solution that could quickly and reliably maintain flexibility in regards to tools, fixtures and production while maintaining high tolerances.
"We have produced control valves throughout our 100+ year history," said SAMSON Controls COO James Evans. "We knew we would implement an FMS utilizing horizontal machining centers (HMC) to meet our present requirement. However, our volume was not sufficient to implement the system in one step. We believe in steady growth, so we needed to partner with a machine tool manufacturer that was proven over time, had stable designs and controlled the entire stack-including pallet pool, machine, tool changer and software-and one that we could count on for the next decade."
An Up Close Look
Evans and his team met with many companies, and eventually hit on a solution through AMS Automation, Inc., a local representative for various European, Japanese and Taiwanese machine tool builders.
"Based on SAMSON's cell requirements, I knew that MCM could not only meet their requirements but exceed them as well," said Mark Danielewicz, VP and Sales Engineering Manager, AMS Automation. "MCM manufactures extremely accurate and powerful machines that are designed from the ground up to be run in unattended environments, so they have thought of every potential issue and addressed these areas with incredible detail."
Danielewicz arranged a trip to Italy so the SAMSON team could see some MCM FMS cells in action.
"One customer had eight different MCM FMS systems across multiple facilities, with some dating back to the 1990s and still running, along with new MCM FMS systems being installed," said Danielewicz. "The cell that was most like what SAMSON required was running like clockwork, with no operators standing at the controls. Operators were either loading pallet load/unload stations or changing inserts for various tools and adding them back into the cell, all while the machines were running production. This cell was installed around 20 years ago."
One customer, who has seven, separate five-machine cells, said that the MCM machines are very good, but it is the SUPERVISOR Software system that really sets MCM apart. It enables the customer to review a large amount of data to enable them to better schedule, prepare and optimize production and manufacturing. Plus, all this data is available for everyone in the company to see remotely and in real time. This provides a more efficient process when making last minute modifications to their ever-changing production schedule. This software also enables the customer to generate a plethora of potential reports and data to show the machine(s) output metrics and their production.
"Another item that led Samson to select MCM was the fact that MCM provides and manufactures the 'entire' FMS system, whereas most other manufacturers will rely upon third-party vendors for the palletization system," said Danielewicz. "The entire MCM system is constantly monitoring all aspects of the cell."
Evans added: "Seeing MCM in action was impressive. We saw several installations with a large number of machines that were 20 to 25 years old and still running on original spindles. Reliability is important."
The FMS Solution
One of SAMSON's main requirements was the ability to manage a large number of different codes with small to medium volumes. The FMS solution developed in cooperation with MCM consists of two MCM CLOCK 1200 4-axis machining centers equipped with 399 tools with individual micro chips, managed by an HSK 100 electro-spindle, along with variable bearing preload, direct measurement system on all axes, CNC FANUC 31 iSeries B5, 24 pallets 630 mm x 630 mm (24.8" x 24.8") and two loading/unloading stations.
The machines can share both tools and pallets independently. Therefore jFMX, MCM's exclusive supervision software, can send the working mission, part program, fixtures and tools to the machine immediately available, without having to wait for the resources to become ready for use-thus increasing the productivity of the system by raising the percentage of load capacity.
The machines are also equipped with the jNodeFR hardware unit with the JFRX application. This system collects all the data coming from the sensors present on the machine, performing on-site analysis and aggregation for predictive maintenance purposes.
CLOCK 1200 Technical Features
Machining center features include:
- Strokes: X-axis 1,200 mm (47.24"); Y-axis 850 mm (33.46"); Z-axis 850 mm (33.46")
- Rapid feeds on X and Z axes: 75,000 mm/min. (2,952.7 IPM)
- Rapid feeds on Y-axis: 60,000 mm/min. (2,362.2 IPM)
- Linear axes measuring system (XYZ): pressurized HEIDENHAIN optical scale
- HSK-A100 electro-spindle max. speed: 10,000 RPM
- Continuous power (S1): 50 kW (67 HP); max. power (S2-25% t=2 min.) 60 kW (80.4 HP)
- Front bearing: 110 mm (4.33 in)
- Continuous torque (S1): 300 Nm (221.2 ft-lbs.); max. torque (S2-25% t=2 min) 487 Nm (359.1 ft-lbs.)
- Variable pre-loading bearings
- Tack-type mirror tool magazine
- Tool magazine total capacity (for two machines): 399
- Max. tool length: 500 mm (19.6")
- Max. tool diameter: 340 mm (13.3")
- Continuous rotary table
- Positions: 3,600,000
- Positions: 2
- Pallet size: 630 mm x 630 mm (24.8" x 24.8")
- Pallet storage places: 20 on two levels
- Pallet tables (total for two machines): 24
- Pallet size: 630 mm x 630 mm (24.8" x 24.8")
Included options:
- Automatic washing of the workpiece controlled by an M-function
- Tool taper washing with coolant at high pressure and compressed air for drying
- Inductive sensor for thermal compensation on electro-spindle
- Tool power monitor surveying system of the power absorbed by the spindle
- High pressure (65 bar, 945 PSI) coolant through the tool center, high efficiency management of the high pressure with continuous adjustment between 10 bars (145 PSI) and 65 bars (945 PSI).
- FANUC 31iB5-06 package for orbital turning
- Buffer for quick tool regeneration (rack type), side rack type buffer (for eight tools) located near the changer arm
- Oil separator for the exceeding oil eventually present on coolant system
- High precision radiofrequency probe for dimension measuring, research of the zero-piece, etc. assembled on HSK-A100 taper; signal transmission through a radio waves system
- Automatic tool presence control, carried out using a laser photocell and positioned outside the work area, next to the tool manipulator
- Exhauster filter complete with high efficiency filter DOP 99.99 % (absolute filter).
Steady, Stable Growth
SAMSON began with a single machine, and added a second machine 18 months later.
"The first machine worked as we expected," said Evans. "The system was reliable, accurate and improved our throughput. The planning software increased our productivity due to the flexibility afforded by 200 tools and 10 flexible pallets."
Evans pointed out that MCM utilizes cutting-edge technology while also maintaining compatibility across multiple generations of machine. "This allows us to grow our FMS line over time without backward compatibility concerns," he said. "The software and hardware are maintained under one roof, which makes service less of a concern. There is one point of contact for any issue. Also, there is one point of contact for any changes that we request that could add productivity to our shop floor."
Having two systems working together is furthering the productivity gains they already saw. "We are further optimizing our tooling," said Evans. "We can increase the number of duplicate tools to ensure operators only need to change inserts once per shift. We can share expensive, highly engineered tools between both systems so we do not need to carry these in our inventory."
Evans concluded: "We are still learning, but we have already reduced average lead times by more than one week while producing 20% more per machine."
SAMSON Controls is a wholly owned subsidiary of SAMSON AG, which was founded in 1907 and headquartered in Germany. SAMSON Controls USA, founded in 1992, is the North American manufacturing headquarters for SAMSON.
SAMSON capabilities include precision machining, grinding, coatings, injection molding as well as electronics manufacturing. Products are produced and assembled in-house.
For more information contact:
SAMSON Controls, Inc. (USA)
4111 Cedar Blvd.
Baytown, TX 77523
281-383-3677
contact-us@samsongroup.com
www.samsoncontrols.com
MCM USA
215 Fifth Ave.
Chardon, OH 44024
440-286-2148
service.usa@mcmspa.it
www.mcmspa.it
SOUTHWEST
AMS Automation, Inc.
7308 W Little York Road
Houston, TX 77040
713-460-8881
office@amsautomation.net
www.amsautomation.net