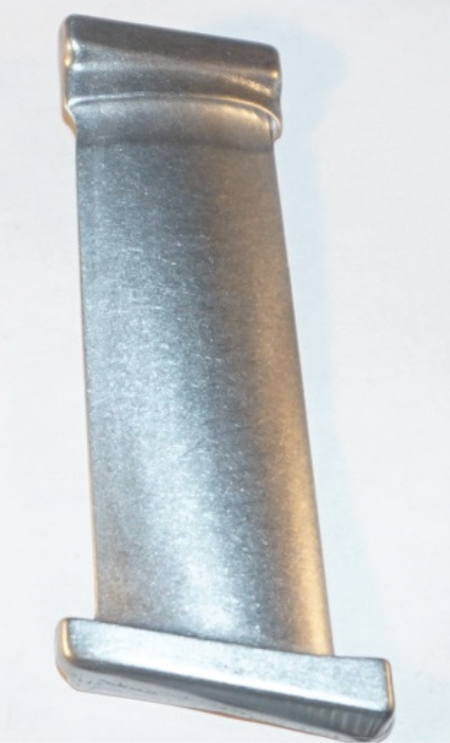
An aerospace compressor blade that was centrifugal disc finished from surface Ra of 57 to 8
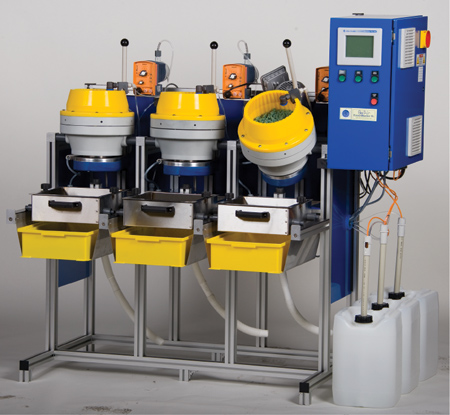
Bel Air's centrifugal disc finisher FMSL model
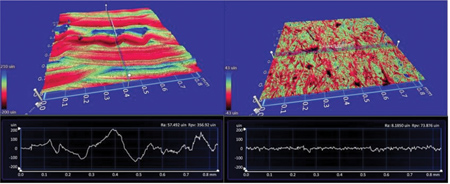
An aerospace compressor blade that was centrifugal disc finished from surface Ra of 57 to 8
In order to help manufacturers increase throughput, decrease cost and increase quality of metal parts, Bel Air has developed Centrifugal Disc Finishers. These machines are designed to both polish and deburr a wide range of materials including brass, copper, steel, stainless steel, aluminum, kovar, titanium and more.
"They have been proven effective by eliminating 80% of handwork and producing over five times the output of normal hand deburring operations," said a company spokesperson. "They have also been able to drastically reduce surface RA in metal parts across aerospace, automotive, medical and other industries."
The Centrifugal Disc Finisher comes in sizes ranging from 4 to 60 liters and most models come with a mobile frame, suitable for cellular and JIT production. A variety of additional features are available, including integrated ultrasonic cleaners, on-board media storage, a direct compound feed system and parts separation options.
The Centrifugal Disc Finisher works by using a bowl-shaped finishing chamber comprised of a fixed upper bowl and spinning bottom disc. The disc rotates both the media and parts within the chamber, forcing the mass to the stationary outside wall. This mass of part(s) and media then folds back to the center. This process is repeated, creating a 3D toroidal action similar to a vibratory bowl finisher. However, this action is tighter and produces 10x the G force of a vibratory bowl finisher. While this is happening, water and finishing compounds are added into the mix to keep the media and parts clean.
Bel Air models have a North/South gap allowing for the easy adjustment of the gap system. Process effluent-which contains the broken down parts of media, small amounts of part materials and water mixed with compounds-flows through the gap, wearing it down. Bel Air's adjustable gap system allows the gap to be closed as it wears down, extending the machine's service life.
For more information contact:
Bel Air Finishing Supply, Inc.
101 Circuit Drive
North Kingston, RI 02852
401-667-7902
info@belairfinishing.com
www.belairfinishing.com