
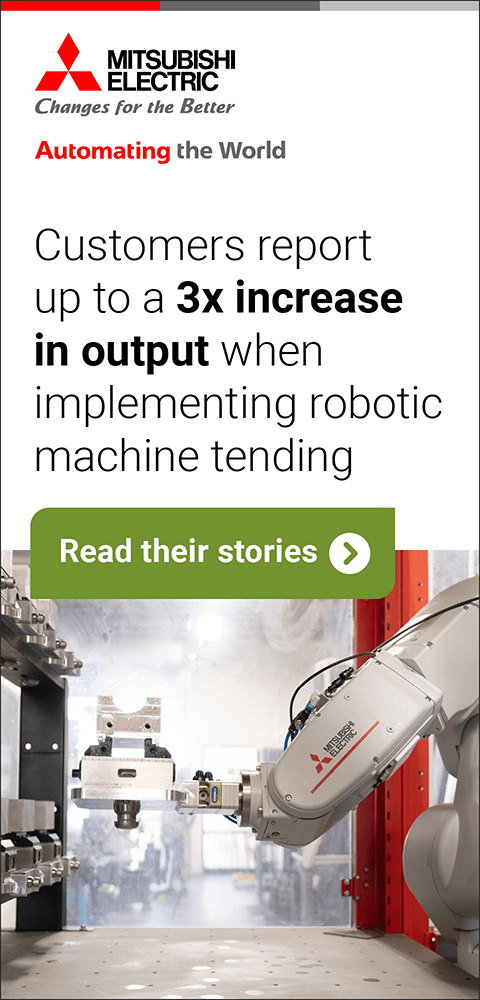
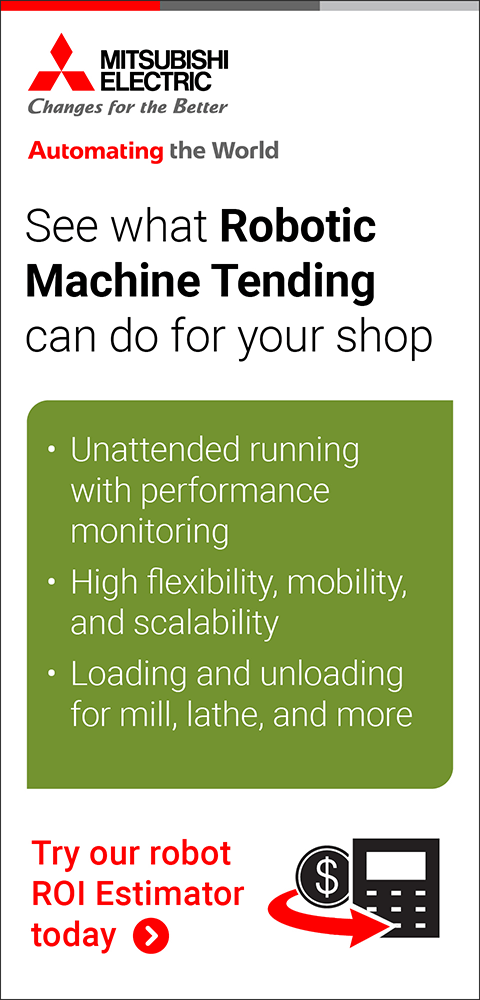




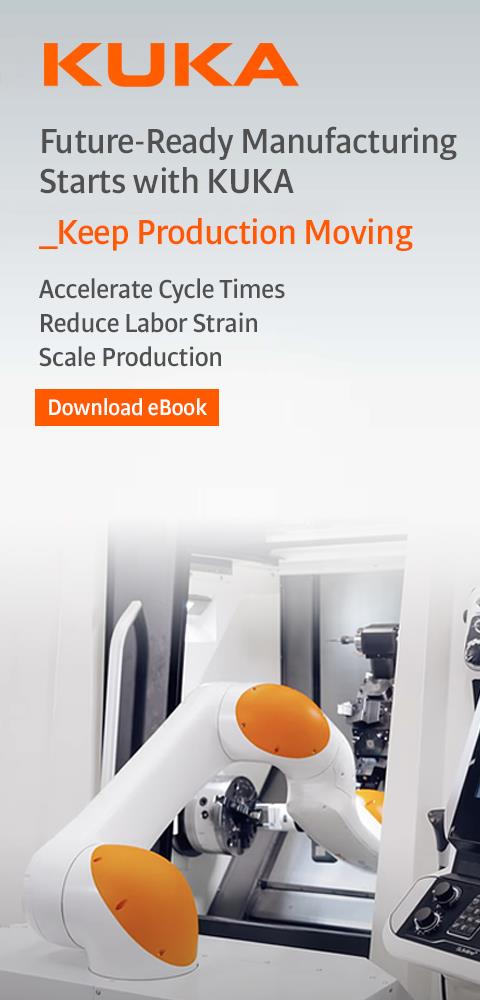
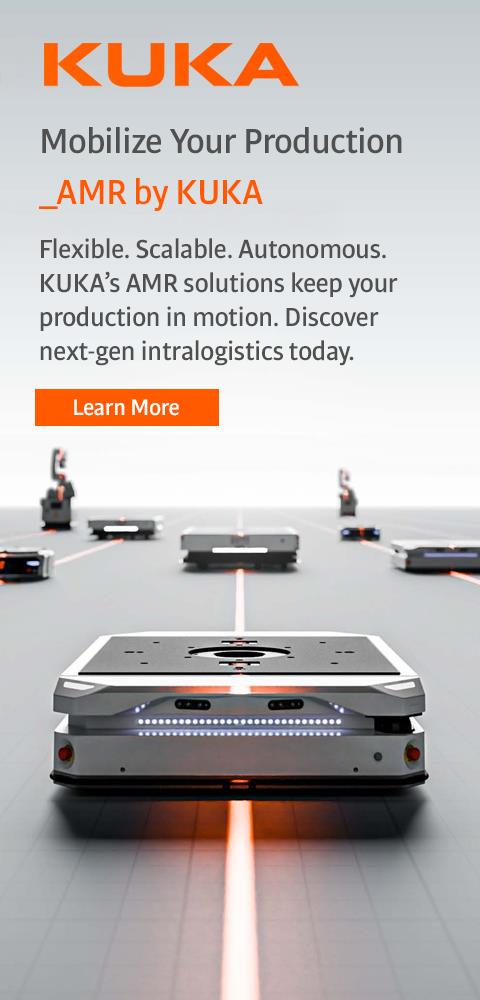
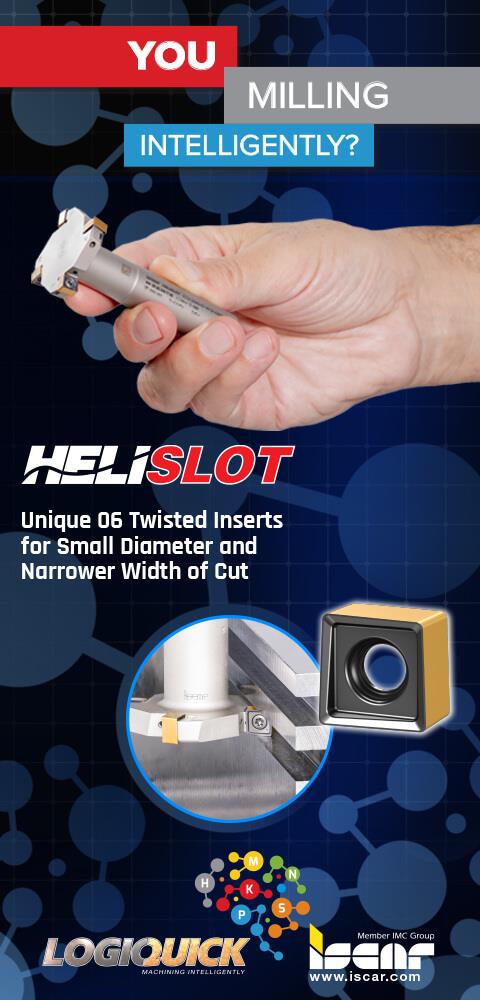
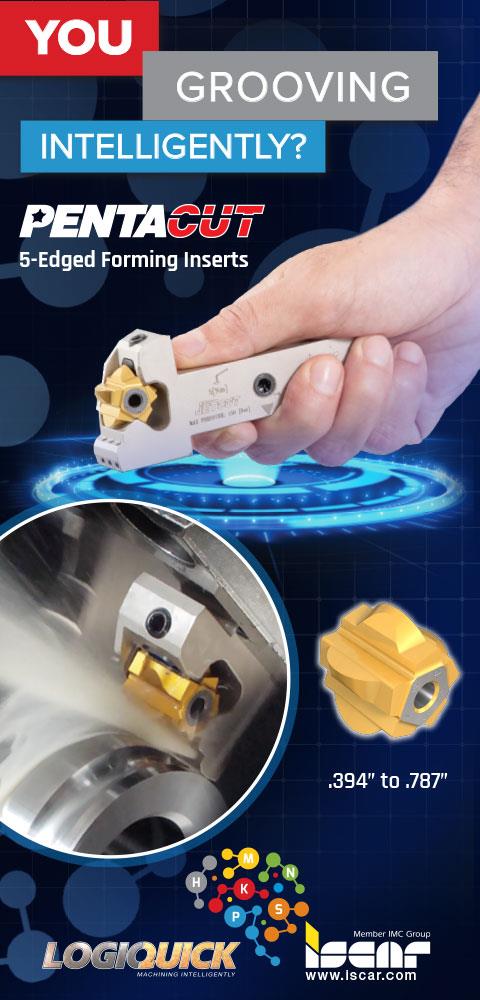
Pinch/Peel Grinding Machine
October 1, 2021
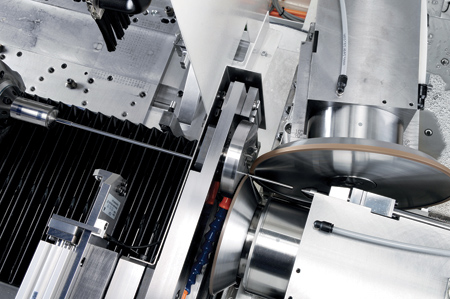
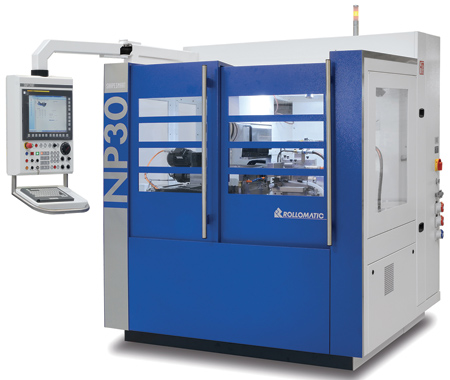
ShapeSmart NP30 pinch and peel grinding machine
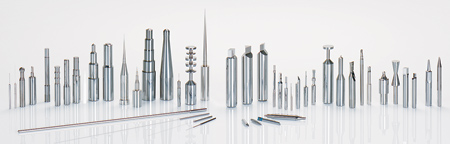
Examples of parts ground with the pinch/peel method by the ShapeSmart NP30 and NP50
Rollomatic has introduced the ShapeSmart NP30 pinch and peel grinding machine, which replaces the original NP3+ model. "Rollomatic is the original inventor of the pinch/peel grinding methodology and stays in the forefront in developing new models and specific processes related to making these types of machines even more productive," said a company spokesperson.
Pinch grinding offers high concentricity, particularly on long and thin parts. The rough and finish grinding are performed in one pass. This innovative way to grind roughing and finishing simultaneously eliminates a separate process and reduces cycle time. The machine utilizes two different grinding wheels running on separate spindles and positioned on independently-controlled CNC linear slides.
New features include:
- Both the finish and the roughing station have a separate direct-drive synchronous spindle motor that provides better stock removal, less induced heat, better surface finish and longer wheel life.
- Redesigned workhead for higher stability during grinding of large parts
- Switch-over of roughing station from 10° to 90° within a few minutes.
Existing features include:
- Mirror surface finishes and near-zero TIR for drill margins can be achieved.
- Repeatable process with tight tolerances and for long-batch production
- Both grinding stations are equipped with super-abrasive wheels with different grit sizes. One wheel carries out the rough grinding, while the other wheel is for finish grinding. The grit sizes and bond compositions are selected to optimize the surface finish to be achieved, and find the right balance between minimal wheel wear and best cycle time.
- A proprietary process that involves multi-pass grinding and pinch finish grinding is used, which has been developed over many years of testing.
- Dimensional tolerances can be maintained over long or short production runs with the help of in-process measurements, and automatic compensation for wheel wear and for changes in ambient temperature.
Typical applications:
- Blank preparation for the industrial, orthopedic and dental cutting tool industry
- Grinding of grip attachments (quick-disconnect) on orthopedic and dental cutting tools
- Core pins for pipettes in the plastic injection molding industry
- Precision punches and cold-forming tools
- Mold components such as gate valve stems, ejector pins, core pins and more
- Weaponry-related parts such as firing pins and more
- Precision pins for the electronic, fiber optic and related industries.
Both grinding spindles are synchronous direct-drive spindles with 19 HP peak each. "The most important feature of a synchronous motor is that it provides constant speed during its operation while the torque curve is highly efficient," said the spokesperson. "The rotational force is not reduced with higher RPMs. Synchronous motors always run at a speed equal to their synchronous speed, as opposed to asynchronous motors (induction motors) which always have a lag and are therefore less efficient."
For more information contact:
Rollomatic Inc.
1295 Armour Boulevard
Mundelein, IL 60060
847-281-8550
solutions@rollomaticusa.com
www.rollomaticusa.com
< back