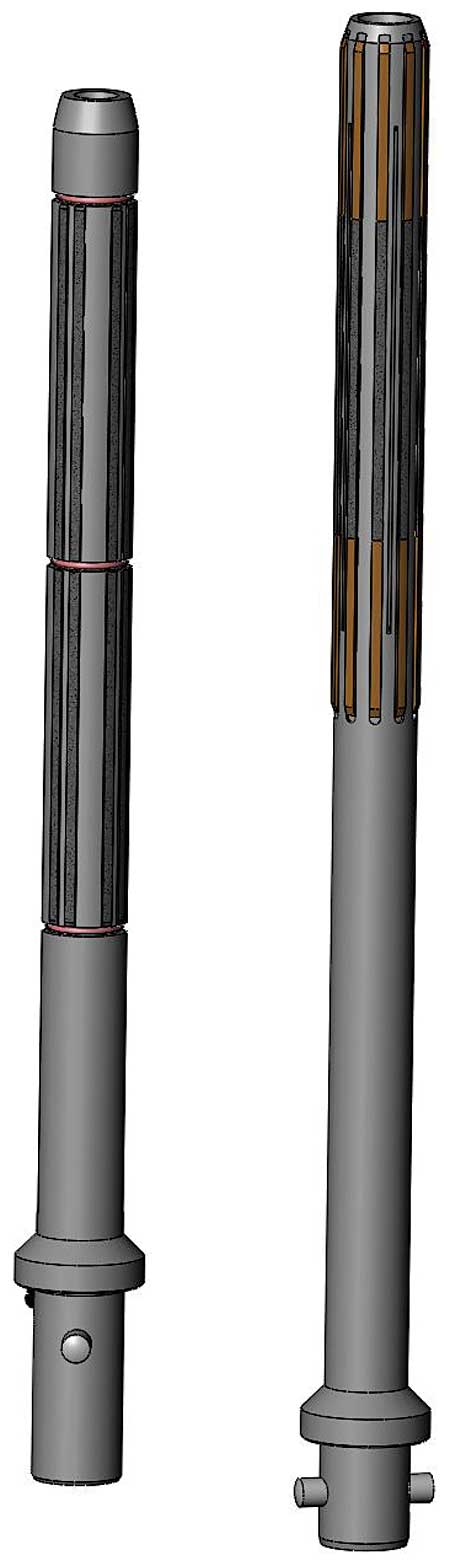
Stroke hone tool (left) used in the roughing station and diamond sizing tool (right) used in finish station of Nagel ECO 40 for a hydraulic valve body.
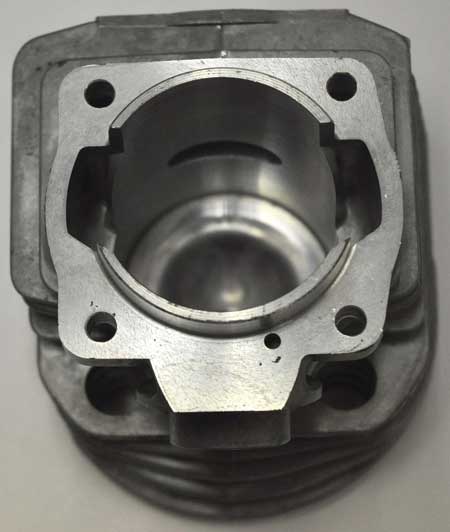
Given the fact that a diamond sizing tool has to travel few inches to get good cutting action, blind or near blind bores should be finished by stroke honing process. Blind bore example shown is a string trimmer engine cylinder.
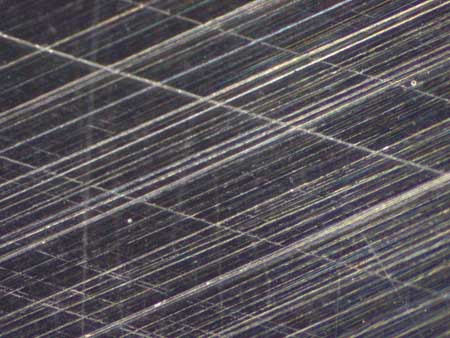
Cross hatch finish
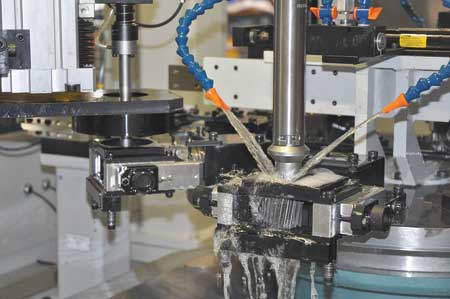
Hardened gear honed by a Nagel ECO 40 hone.
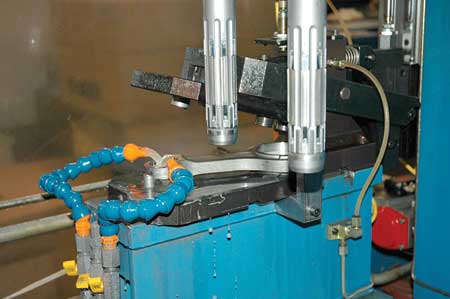
Connecting rod being diamond sized in the ECO 40 hone.
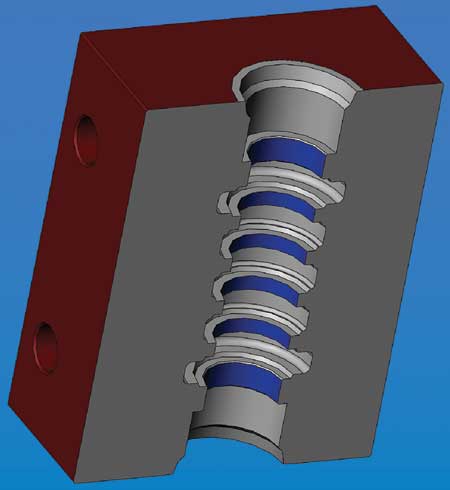
Section of a hydraulic valve body
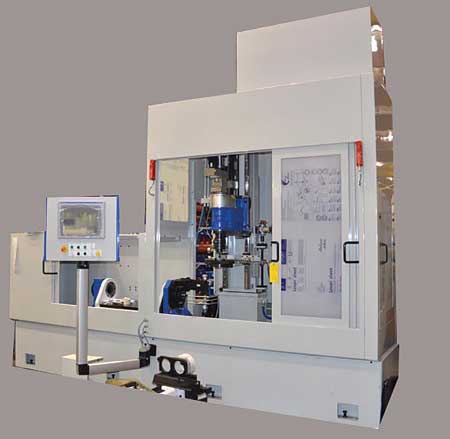
The Nagel ECO 180 features stroke honing and diamond sizing capabilities.
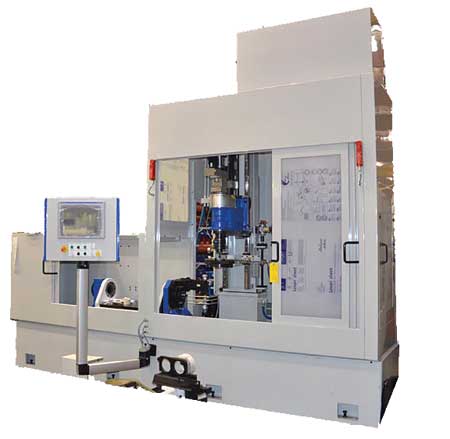
Honing operations can be grouped into two categories: conventional stroke honing and single pass honing / diamond sizing.
In conventional stroke honing, the honing tool is collapsed when it enters the bore and then expands inside the bore at a controlled rate - rapidly until it reaches the wall and then more slowly once the contact is made. The tool oscillates while rotating to remove stock. An air gauge built inside the tool head measures the bore size in-process and stops the honing process once the set target is reached.
Diamond sizing, on the other hand, has a fixed reamer, and the rotating tool plunges while removing all the stock. Stock removal is typically distributed among multiple tools and final size is dependent upon the tool diameter.
"It is important to select the most suitable process for a given part," said a Nagel Precision spokesperson. "Unfortunately, it is quite common to see manufacturing process engineers pick a wrong process for their application. In a number of instances this has resulted in procuring the proper type of expensive machinery after the project launch and making a running change. This is both expensive and very stressful."
Nagel Precision suggests the following general guidelines, which include specific part features and print requirements, that would be suitable for one stroke honing or diamond sizing, or both in some instances.
- Blind bore: Given the fact that a diamond sizing tool has to travel few inches to get good cutting action, blind or near blind bores should be finished by stroke honing process.
- Surface lay: Often bearing surfaces specify a cross hatch pattern, which is a function of stroking and rotation speeds, while the seal manufacturers recommend no lead surfaces, which is obtained by briefly stopping the stroking at the end of the cycle. The cross hatch pattern helps in maintaining the hydrodynamic lubrication layer in bearings and the no lead finish required by seals arrests the leak path, thus enhancing the sealing capability. Diamond sizing by virtue of rotating while plunging in always creates a spiral finish that is desired neither by bearings nor seals. When a particular lay is required, stroke honing is the preferred method of honing.
- Through bores made of hardened material (>55 Hrc): While it is possible to use either process on hard parts, it is recommended to stroke hone such parts.
"In one case, an automotive OEM manufacturing high volumes of pinion gears was exploring the possibility of diamond sizing, as the process is generally quicker than conventional stroke honing," said the spokesperson. "The customer produced stroke honed parts with an existing Nagel hone, and also procured diamond sized parts to same surface finish, roundness accuracy and size tolerances from a Tier 1 supplier of gears. The only visible difference was in the lay. The stroke honed part had a 45° cross hatch and the diamond sized part had a spiral lay. Both part types were then sent for accelerated wear testing. The diamond sized gears failed upon reaching 60% of the minimum required time while the stroke honed gear did not fail even after reaching 110% of the required minimum time.
"It was determined that cross hatch was one of the contributing factors for failures, but did not fully explain such large disparity. Upon analyzing the gears under a scanning electron microscope, micro cracks were found in the diamond sized hard gear, which explained the quick failure. As mentioned earlier, the diameter and taper of the mandrel is fixed. If the incoming bore size is on the lower end of the tolerance, the rougher mandrel has to remove that extra stock in the same amount of time, given that the feedrate is constant. This aggressive stock removal of the hard part was deemed to have produced micro cracks in the part. However, in the case of stroke honing, the cutting rate was constant and produced a surface of better integrity."
- Thin through bore: Components such as latches, torque converter discs, etc. that are generally under 2 mm thick - whether hard or soft - are better suited for single pass honing. Fixturing the thin part in stroke honing presents a challenge and better quality is obtained by diamond sizing them.
- Components made of soft material (<35 Hrc) and having through bores: These type components, such as automotive powder forged or wrought connecting rods, are soft and typically require both crank and pin bores to be honed. While either process can hone the connecting rod, the single pass diamond sizing process offers a notable advantage. Diamond sizing being relatively quick - about twice as fast as stroke honing - provides the opportunity for significant equipment cost reduction when dealing with high volumes. When there are no crosshatch requirements, diamond sizing is a good process for soft through bores with low length to diameter ratio.
In some automotive connecting rods and marine connecting rods, rough and semi finish honing operations are performed on a diamond sizing station and finishing is done on a stroke honing station. This approach affords the advantage of both processes - the speed of a diamond sizing process and the ability to impart lay with the stroke honing process.
- Through bore with interrupted lands: A hydraulic valve body has one of the most stringent requirements for size and surface finish. Typically they call for cylindricity and size tolerance of less than 0.002 mm. They are usually made of cast iron or some soft metal. This is one of the most challenging applications to hone. Given it has multiple lands, size control between land to land is a challenge for conventional stroke hone. But, the high L:D ratio makes it impossible for the diamond sizing operation to correct the straightness, as it will follow the existing banana shape of the bore. Applications like this would benefit from a rough pass with a stroke honing operation that can short stroke at problem areas to remove more stock and correct the straightness and a finish pass with diamond sizing system to get the diameters of the lands under control.
"Going back and forth from single pass honing to stroke honing process as in a low volume job shop environment poses a challenge," said the spokesperson. "In the past it would have necessitated two different types of equipment. Also, the two previous scenarios described for a hydraulic valve body and connecting rod would have required both types of machines - driving up the cost of the component. Manufacturing engineers typically have had to choose whether to buy a conventional stroke honing machine or a single-pass diamond sizing machine, and then make do when parts suited for the other type of process materialized.
"As an alternative, Nagel is offering the ECO series 40, 80 and 180 honing systems that switch from conventional stroke honing mode to single-pass, diamond sizing mode at the press of a button. It means that within one system the operator has control over the honing technique and the ability to choose the best option for the particular project. In a multiple spindle setting when processing a hydraulic valve body the rougher can be run in stroke honing mode and finisher in diamond sizing mode. When processing a connecting rod, the same machine can switch the rougher to diamond sizing and finisher to stroke honing with a push of a button. This offers immense flexibility for tightly toleranced parts."
Article supplied by Nagel Precision, Inc.
For more information contact:
Nagel Precision, Inc.
288 Dino Drive
Ann Arbor, MI 48103
734-426-5650
info@nagelusa.com
www.nagelusa.com