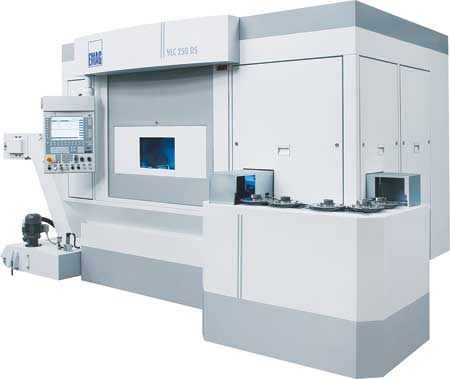
VLC 250 DS: Hard turning and grinding on a single machine.
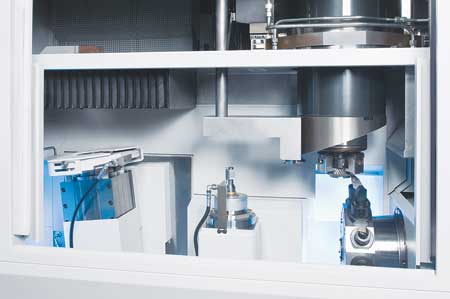
Generously proportioned maintenance and service openings are designed for ease of access from both front and rear.
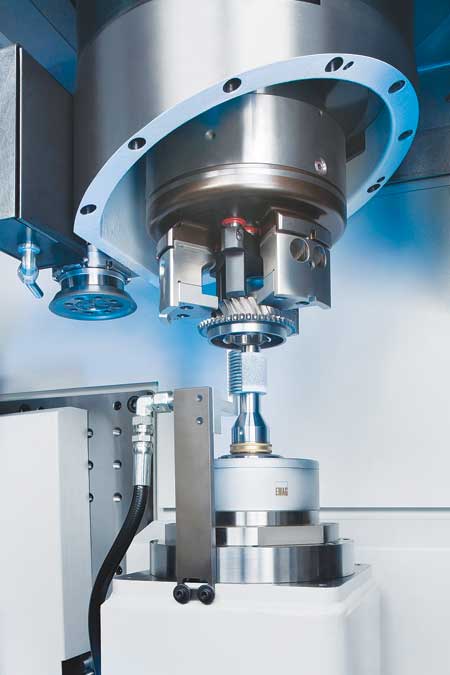
An internal grinding spindle and separate dressing attachment on a VLC 250 DS.
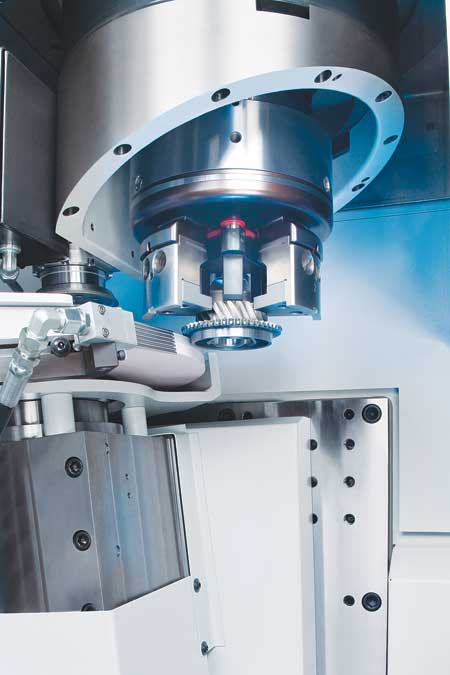
Machining area of the VLC 250 DS: Multi-functional application of a combined turning and grinding machine with external grinding wheel, internal grinding wheel and disc-type turret for twelve turning tools.
According to EMAG the advantages of combining the hard turning and grinding processes include process consolidation, improved component quality and greater flexibility. This combination provides the benefit of shortened cycle times. Throughput, transport times and storage periods can be drastically reduced where all the hard fine-machining operations can be carried out on a single machine.
An important factor for combination machines is ensuring safe machining with an unhindered flow of the turning and grinding chips. The VLC 250 DS, with its vertical work spindle and tools positioned below the workpiece, is designed for optimal chip flow conditions. The vibration dampening properties of the MINERALIT polymer concrete machine base create a mechanically sturdy machine module. The design of the work spindle, which forms an integral part of a quill that carries out its Z-axis movement on a high-precision, hydrostatic guideway also contributes to the vibration damping effect.
The tooling systems are firmly anchored in the machine base and provide a stable environment for the demanding turning and grinding operations. "This is important for time-saving hard pre-turning work and for achieving the best surface finish with a hard finish-turning or grinding operation," said a company spokesperson. Number and design of the stationary tooling systems can be chosen to suit the individual machining requirement and continuous monitoring of the machine's temperature ensures thermal stability. The operating temperature is reached and maintained within strict limits of the ambient temperature by a powerful cooling unit. The pick-up technique employed on the VLC 250 DS turning and grinding center allows the machine to load itself.
The VLC 250 DS is designed for handling complex manufacturing processes, whether turning at high chip removal rates or a gentler grinding operation. The machine covers a wide range of applications and complete-machining in a single set-up in order to eliminate reclamping errors. Measuring operations can also be included. The measuring probe is located between the machining area and pick-up station, where it is safe from chips and coolant. Since the workpiece remains clamped during the gauging process, intermediate measurements can also be taken.
The manufacture of gearwheels is a typical example of combination machining. The end face is hard finish-turned while bore and cone are pre-turned and then finish-ground. For this purpose the machine is equipped with two grinding spindles, where one spindle machines the bores and the other carries out the external grinding work. As the amount to be ground is only a few hundredths of a millimeter, the grinding wheels need only be designed for finishing operations.
The company reported the following features for the VLC 250 DS:
- Vertical hard turning and finish-grinding on a single machine and in one set-up.
- All sectors of the workpiece that can be turned with process integrity are hard finish-turned, and only those that demand high quality requirements and process integrity are ground after hard pre-turning.
- As the grinding process need only remove nominal material, the wear on the grinding wheel is minimal and requires it to be straightened infrequently, and then only by a fraction.
- The grinding wheel specification can be set to a "finishing quality," as only a very small allowance needs to be removed. This produces process-capable surface finishes in the Rz < 1.2 um range.
- Unlike hard turning processes, the grinding operation will generate scroll-free surfaces on the same machine.
- The problem of rear end faces being difficult to reach with a grinding wheel is solved with hard turning.
- The cross-operational machine design provides easy maintenance and service access.
Technical Data
- Chuck diameter: 250 / 315 mm
- Swing diameter: 350 mm
- Travel in X, max.: 1,600 mm
- Travel in Z: 300 mm
- Travel in Y: (optional) +/- 100 mm
- Rapid traverse speed, X: 60 m/min
- Rapid traverse speed, Z/Y: 30 m/min
For more information contact:
Peter Loetzner
EMAG LLC
38800 Grand River Avenue
Farmington Hills, MI 48335
248-477-7440
info@usa.emag.com
www.emag.com
Southwest
AR
Ken Pope
EMAG LLC
256-642-6842
kpope@emag.com
www.emag.com
TX, OK, LA
Ric Lorilla
EMAG LLC
248-595-1530
rlorilla@emag.com
Southeast
VA, NC, SC, GA, FL
David Fitzgerald
EMAG LLC
248-595-1117
TN, AL, MS
Ken Pope
EMAG LLC
256-642-6842
kpope@emag.com
www.emag.com
Northeast
PA, NY
Kirk Stewart
EMAG LLC
248-996-4703
kstewart@emag.com
ME, NH, VT, MA, RI, CT, NJ, DE, MD
Jonathan Chomicz
EMAG LLC
248-497-8526
jchomicz@emag.com
WV
Ken Pope
EMAG LLC
256-642-6842
kpope@emag.com
www.emag.com
Midwest
IN, OH
Kirk Stewart
EMAG LLC
248-996-4703
kstewart@emag.com
MI
Geoff Fuller
EMAG LLC
248-632-2021
gfuller@emag.com
ND, MN, WI, SD, NE, KS, IA, MO, IL
Bill Konetski
EMAG LLC
612-804-0857
bkonetski@emag.com
KY
Ken Pope
EMAG LLC
256-642-6842
kpope@emag.com
www.emag.com
West
Arnie Sugiyama
Caltec International
19801 Hamilton Ave
Torrance, CA 90502
310-527-4110
arnie@caltecusa.com