


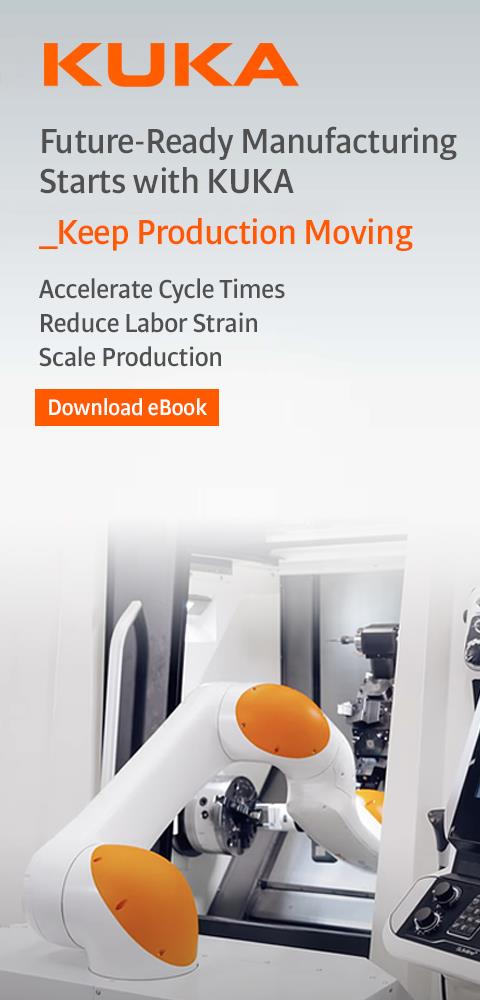
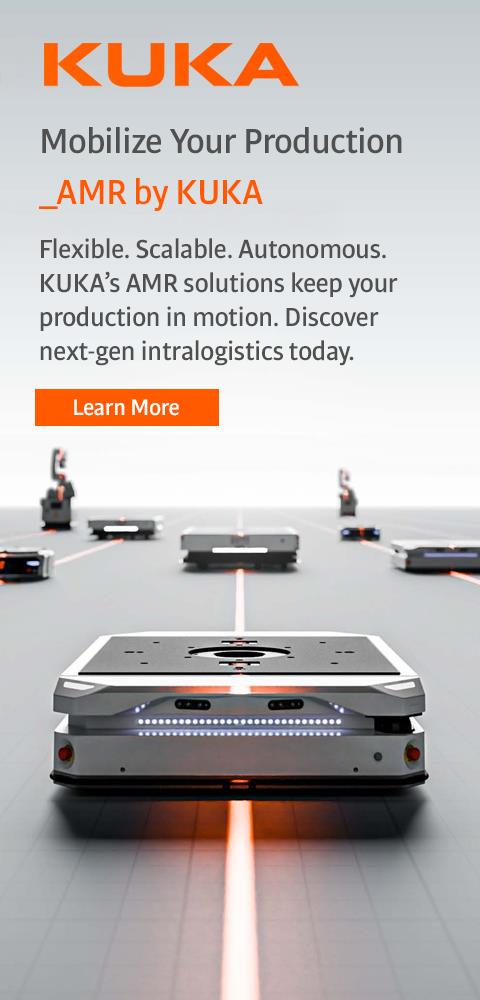
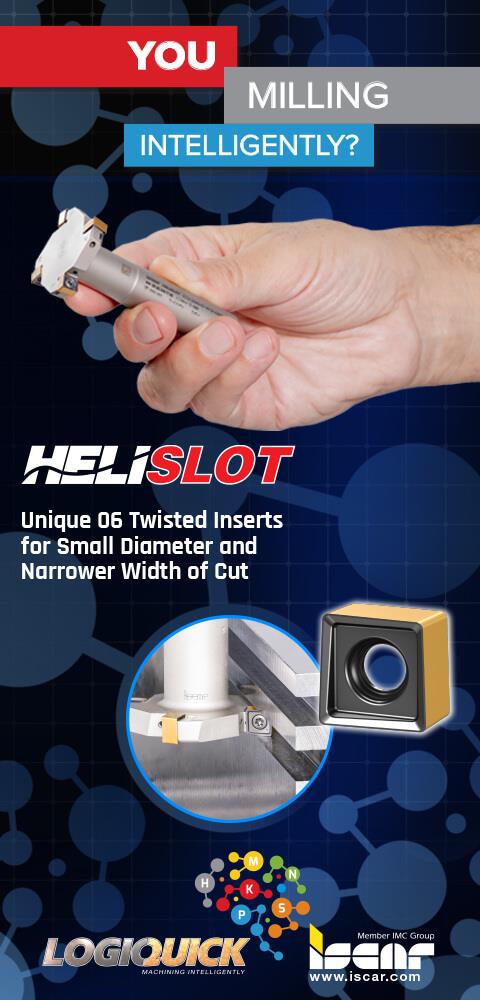
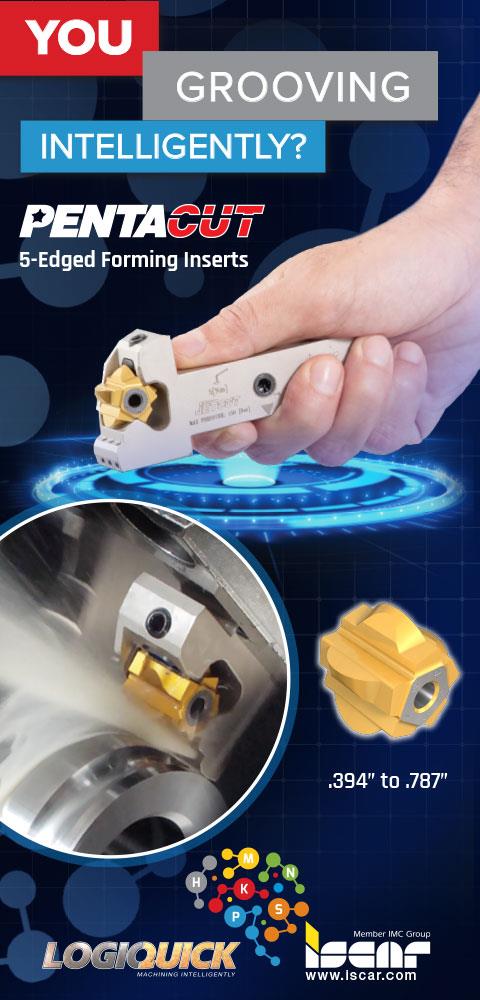
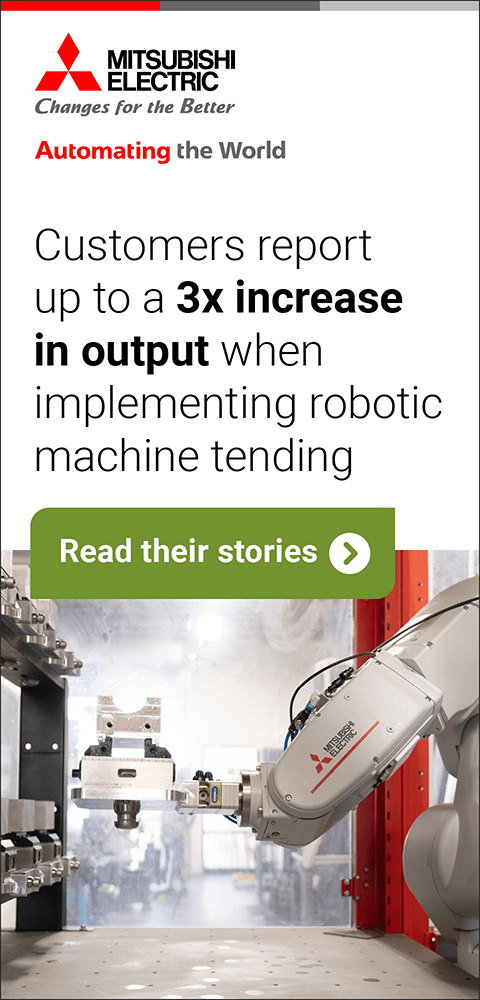
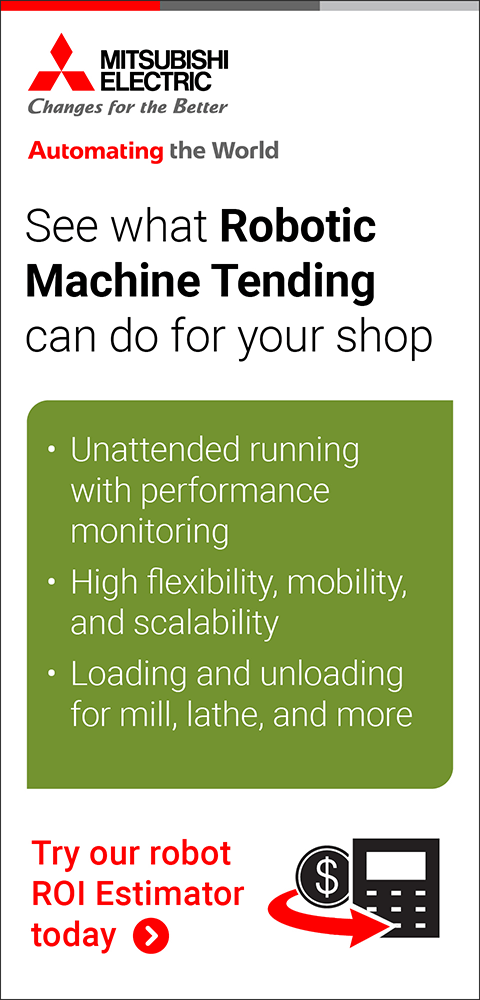


Rotary Clamp Bore Face Grinder
June 1, 2015
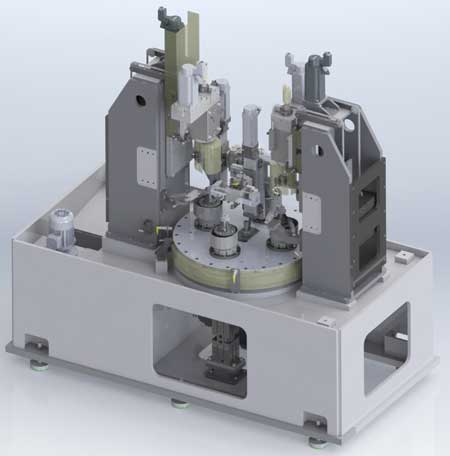
Nagel 2SPV C4 clamp bore face grinder (guarding removed)
"The new Nagel 2SPV 4C clamp bore face grinder differs from conventional grinding operations," said a Nagel Precision spokesperson. "The accuracy of ordinary grinding operations depends on rigid fixturing as well as the accuracy of the grinding wheel's position relative to the part, whereas 2SPV 4C utilizes free cutting vitrified / CBN cup wheels and the tool self dresses and conforms to the contours of the part. This automatically compensates for inaccuracies in the machine."
During this operation, the part is clamped on the internal or outer diameter and rotated in a direction opposite to that of the cup wheel at a high surface speed. To prevent variations in flatness or axial runout when finishing flat surfaces, the cup wheel tool substantially overlaps the surface of the part during machining. The machine can quickly remove as little as a few microns of stock up to a few hundred microns. In process gauging accurately controls the part thickness. The servo rotary table enables part handling and face grinding to occur simultaneously, increasing output.
"The new rotary indexer can index in under a second, eliminating the need for an expensive and time consuming engaging and disengaging mechanism to reduce overall cycle time," said the spokesperson. "With cycle times of 6 seconds per part for stock removal up to 0.1 mm per face, the new Nagel 2SPV C4 matches the productivity of a double disk grinder.
"Gear manufacturing has significantly improved by utilizing this process. The conventional process to finish these gears - grinding them with a double disc after heat treatment - yields an axial runout of approximately 40 um, while cup wheel finishing reduces the runout to less than 10 microns.
"Heat treat to mirror finish with excellent bore / O.D. to face perpendicularity is now a possibility in just one machine. Multiple sensors incorporated into the machine constantly monitor the process and support lights-out manufacturing."
For more information contact:
Nagel Precision, Inc.
288 Dino Drive
Ann Arbor, MI 48103
734-426-5650
info@nagelusa.com
www.nagelusa.com
< back