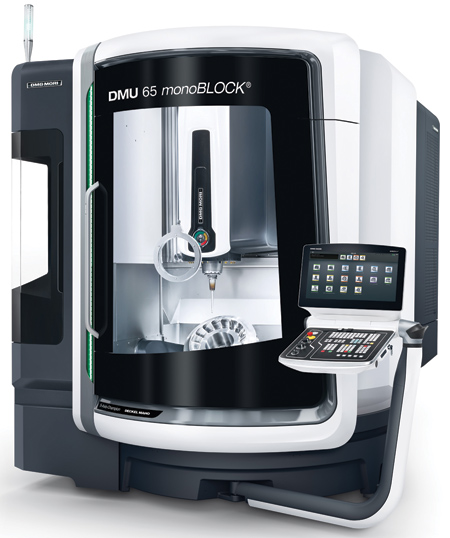
DMG MORI's DMU 65 monoBLOCK is designed for all fields of industry.
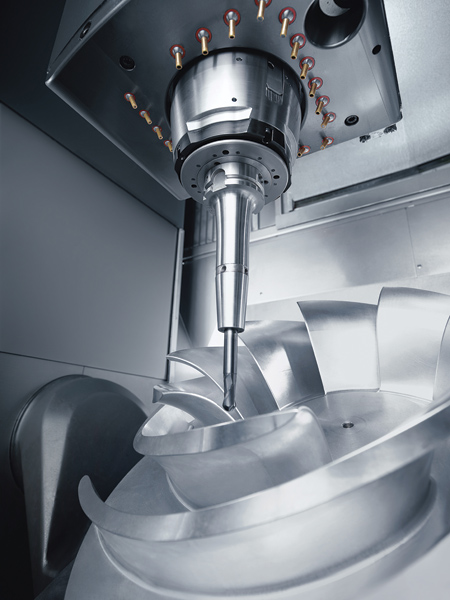
In addition to the standard NC swivel rotary table for workpieces up to 1,323 lbs., the portfolio includes swivel rotary tables with tandem drives in the A-axis for workpieces of up to 2,205 lbs. or with direct drives in the A and C axes for high dynamics and accuracy, as well as the 3-axis version for workpieces up to 6,614 lbs.
DMG MORI's 5-axis DMU 65 monoBLOCK with dynamic NC swivel rotary table offers milling technology from roughing to finishing.
The DMU 65 monoBLOCK features an increase in dynamics and the 1.77" wide roller guides maximize process stability. The DMU 65 monoBLOCK provides three-point support for short start-up times. It features a compact 80.73 sq. ft. footprint.
Despite the small space requirement, the DMU 65 monoBLOCK has a spacious machining compartment. With axis paths of 28.94" x 25.59" x 22.05" in X, Y and Z, the entire NC swivel rotary table surface can be traversed, allowing the workpieces to be machined in one pass. Oversize workpieces of up to 33.07" diameter and weighing up to 2,205 lbs. can be loaded on the NC swivel rotary table.
The operator has access to the DMU 65 monoBLOCK machining compartment through a 51.56" wide door opening, and the 31.5" table height allows an ergonomic body position while working. Furthermore, given the heavy weight of the workpieces, the standard design allows for unrestricted workpiece loading by crane from above.
The machine features simple and comfortable operation and loading of the 30, 60, 90, 120 or 180 position tool. Since the loading station is located in the front area of the machine, the operator can always work in a normal work environment. During make-ready, the control panel can be swung directly towards the tool loading station. The fast sword-type tool changer reduces the chip-to-chip time to 4.9 seconds.
The steep slants of the machining compartment allow the swarf to drop unrestricted, and the stainless steel lining of the machining compartment helps ensure a long operating life. A wide centrally arranged chip conveyor permits fast chip removal towards the rear of the machine.
In addition to the design details, the DMU 65 monoBLOCK offers multiple options of its modular system. These include, among others, modular equipment configurations for the motor spindles. The extensive modular spindle system, starting with a spindle speed of 10,000 RPM (at torque of 82 Nm) in the standard version, offers further application-oriented options with 14,000 RPM (130 Nm), 18,000 RPM (130 Nm) and 24,000 RPM (100 Nm), as well as a sturdy spindle with 10,000 RPM and a 200 Nm torque.
In addition to the standard NC swivel rotary table for workpieces of up to 1,323 lbs., the portfolio includes swivel rotary tables with tandem drives in A-axis for workpieces of up to 2,205 lbs. or with direct drives in A and C axes for highest dynamics and accuracy, as well as the 3-axis version for workpieces of up to 6,613 lbs.
The universal modular system of the DMU 65 monoBLOCK is complemented by production packages, including an internal coolant supply of up to 1,160 psi, as well as a space-saving chip conveyor towards the rear of the machine. These features allow space-optimized placement of the machine on the shop floor. Control offering include CELOS from DMG MORI with a 21.5" ERGOline control with Operate 4.5 on Siemens 840D solutionline or Heidenhain TNC 640.
For more information contact:
DMG MORI - Americas Headquarters
2400 Huntington Blvd.
Hoffman Estates, IL 60192
847-593-5400
Service hotline: 855-DMG-MORI (364-6674)
www.us.dmgmori.com