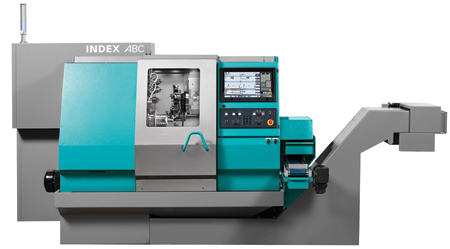
Revised production lathe ABC: more speed and flexibility in production
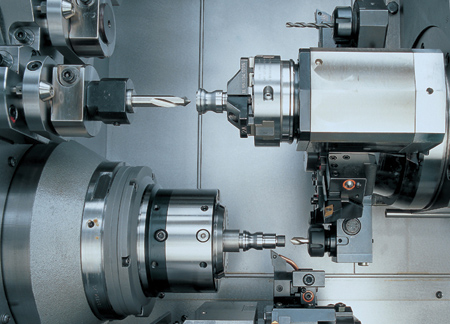
High performance density: up to three tools can be used simultaneously on a small footprint.

Besides the traditional VDI25 toolholders, the upper turret now can accommodate W-serrated holders. One station is reserved for the synchronous spindle.
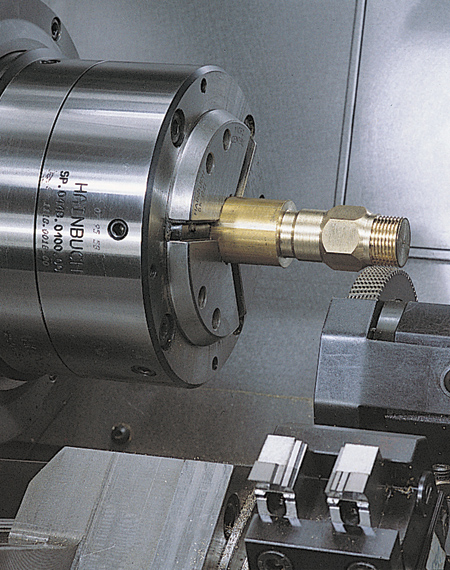
The thread milling and polygon turning unit produces hexagon bar in a fraction of a second.
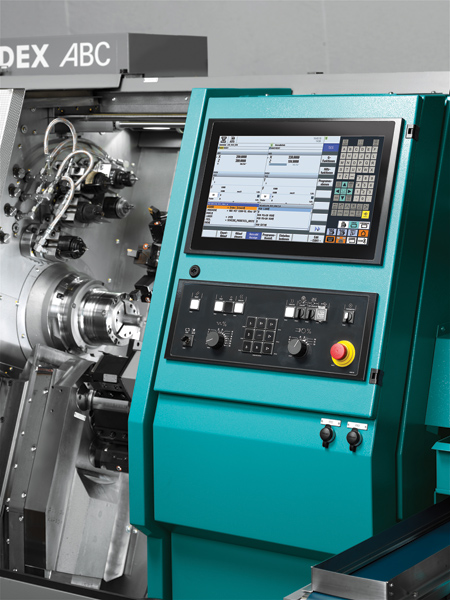
The lathe features future-oriented operation using the INDEX C200 sl control generation based on the Siemens Sinumerik 840D sl (solution line) and has an 18.5" touch-sensitive wide-screen monitor. The latest capacitive touch technology allows even an operation with gloves. In addition, the control panel can also be used for Virtual Machine (VM) developed by INDEX.
The INDEX CNC lathe ABC revision has retained the essential features of its predecessor but is significantly more productive with performance-enhancing modifications - especially on the drive and control side. The lathe has two tool turrets, of which the upper carries the synchronous spindle for rear end machining.
Main Spindle with 65 mm Bar Capacity
A major modification of the new ABC was made to the main spindle. It has a bar capacity of up to 65 mm and is driven by a synchronous motor instead of the previous asynchronous motor. This makes it more efficient and faster. Its maximum speed is 6,000 RPM, providing 27 kW of power (40% DC) and 145 Nm of torque (40% DC). Air cooling has been retained, since the switch to liquid cooling would have required an additional cooler and thus more space.
Upward Compatibility for Toolholders
The developers also thought about existing ABC users in terms of tool carriers and toolholder systems. As a result, their arrangement in the work area and the equipment of the tool carriers are the same. Only the possibilities of the upper turret have been extended: besides the traditional VDI25 toolholders, it can now also accommodate W-serrated holders. Developed by INDEX, these tool mountings enable high change accuracy during set-up and are frequently used for angled tools (e.g., drills).
The user now has the choice of using the W-serrated mountings supplied with the new machine. But there is no need to do away with the existing VDI toolholders, because they can still be used on upper turret. INDEX has also retained the dovetail mountings in the lower turret. This allows the user to use even tooling systems that come from the ABC's predecessors, the INDEX cam-controlled machines.
Three Tools Engaged Simultaneously
The upper turret - equipped with a tool drive (max. speed 6,000 RPM, power 4.3 kW; torque 7.5 Nm at 25% DC) and accommodating seven tools as well as a synchronous spindle - is used mainly for I.D. machining. The lower turret with its six stations is mainly used for O.D. machining. All tool stations in both turrets can thus accommodate live tools. There is a practical innovation in this respect as well: while the lower tool carrier was limited previously to a maximum of 4,500 RPM, this limitation has been lifted in the new ABC and the performance has been raised to a maximum speed of 6,000 RPM (power 3.8 kW, torque 7.5 Nm at 25% DC) - the same as on the upper turret.
The synchronous spindle in the upper tool carrier (max. speed 4,500 RPM, power 5 kW and torque 10 Nm at 25% DC) allows machining of workpieces completely from the back with up to five available back-boring stations.
Two of these back-boring stations can have a separate tool drive with up to 6,000 RPM, 4.1 kW of power and 6.5 Nm of torque (at 25% DC).
Simultaneous centric machining of workpieces with the upper turret on the main spindle as well as one of the three stations of the back-boring unit with the synchronous spindle is possible at the same feedrate on the main and synchronous spindles.
In addition, the lower turret can be used at the same time on the main spindle, so that workpieces can be machined synchronously and productively with up to three tools.
Options
The INDEX ABC production lathe is equipped with a gantry-type removal unit with which the finished parts can be removed gently during main time from the synchronous or main spindle towards the right out of the machine. Bar remnants can be discharged from the main spindle in this way using a separate tray.
The use of the INDEX LMI loading magazine, suitable for bar stock up to 3.2 m length, saves valuable time. The storage tray of the bar support is approximately 300 mm, allowing it to accommodate up to six D50 bars.
Furthermore, a thread milling and polygon turning unit are available with a separate drive (6,000 RPM, 5 kW power at 25% DC). This INDEX development is particularly vibration-absorbing, because the power is transmitted via a toothed belt. Also the polygon turning tool head made of heavy metal provides largely vibration-free running through its high inertia. A company spokesperson stated that this allows a hexagon bar to be produced with high-quality surfaces in a fraction of a second, even in steel, for which cutters would need much more time.
Easy to Use and Process-Reliable
Like all newly developed INDEX machines, the ABC will also be equipped with the INDEX C200 sl control generation, which is based on the Siemens Sinumerik 840D sl (solution line) and an 18.5" touch-sensitive wide-screen monitor. The control panel concept developed by INDEX reduces the complexity in using the control by integrating numerous rotary and tip switches on the machine control panel directly on the touchscreen.
The operating panel can, however, do more than just operate the machine. It features a second input, which INDEX uses for its Virtual Machine (VM) option. On the push of a button, the operator can switch to the "VM on Board," for example, to use the simulation independently from the running machine operation. The VM, which can be run purely with CNC code, works with a VPC box installed in the control cabinet that offers many additional possibilities.
Other VM features developed by INDEX include CrashStop and RealTime. CrashStop allows the advanced simulation of workpiece programs on the machine. RealTime allows the simulation of the machine program simultaneously on the control panel, providing a real-time view of the machining sequence.
Another new feature is the openness for information technology through the XPanel operating concept, which is included as standard. The machine operator can also use the control panel to obtain information from the corporate network, such as component drawings to set up the machine.
Cost Reduction Through Full-Featured Packages
For more than a year, INDEX has provided the ABC also as full-featured package solutions, which offers the machine and includes selected equipment features and options.
The advantage of this package idea is better planning of production, as well as quantity effects, which reduce cost.
For more information contact:
INDEX Corporation
14700 North Pointe Blvd.
Noblesville, IN 46060
317-770-6300
sales@index-usa.com
www.indextraub.com
Southwest
N. TX
G.B. Newbury Machine Sales
6301 Windhaven Parkway #314
Plano, TX 75093
214-914-8869
newburymachine@yahoo.com
OK
Gage Machine Tool
10668 Widmer Rd.
Lenexa, KS 66215
913-894-1233
www.gagemachinetool.com
Southeast
AL, GA
Applied Machine Solutions, Inc.
2200 Airport Industrial Dr., Suite 300
Ball Ground, GA 30107
678-880-0893
info@appliedmachine.com
www.appliedmachine.com
NC, SC, VA
Advance Machinery Sales, Inc.
416-C Gallimore Dairy Rd.
Greensboro, NC 27409
336-665-9114
FL
MIT (Magna Innovative Technologies)
18 South Brooksville Ave.
Brooksville, FL 34601
352-799-2211
sales@mitcnc.com
www.mitcnc.com
Northeast
DE, MD, E. PA, NJ, NYC, Long Island
Automation Solutions, Inc.
2 Hagerty Blvd., Ste. 300
West Chester, PA 19382
610-430-3670
inquire@asi-pa.com
www.asi-pa.com
N. NY
Britton Machinery Sales
330 Castlebar Rd.
Rochester, NY 14610
585-924-9335
www.brittonmachinery.com
W. PA
Marcus Machinery
106 Bellefield Court
Gibsonia, PA 15044
412-862-0803
info@marcusmachinery.com
www.marcusmachinery.com
MA, CT, RI, ME, NH, VT
Northeast CNC, LLC
36 Bartlett Rd., Unit 1
Gorham, ME 04038
207-775-5510
sales@necnc.com
www.necnc.com
Midwest
KS, W. MO
Gage Machine Tool
10668 Widmer Rd.
Lenexa, KS 66215
913-894-1233
www.gagemachinetool.com
WI (except w. counties)
Iverson & Company
441 North 3rd Ave.
Des Plaines, IL 60016
847-299-2461
sales@iversonandco.com
www.iversonandco.com
MI
Methods & Equipment Associates
31731 Glendale Ave.
Livonia, MI 48150
734-293-0660
sales@methods-equipment.com
www.methods-equipment.com
MN, IA, ND, SD, NE (eastern counties), WI (western counties)
Hales Machine Tool, Inc.
2730 Niagara Lane North
Plymouth, MN 55447
763-553-1711
sales@halesmachinetool.com
www.halesmachinetool.com
West
OR, WA
Ellis Machinery & Equipment, Inc.
6225 20th Street E.
Fife, WA 98424
253-926-6868
sales@ellismachinery.com
www.ellismachinery.com