




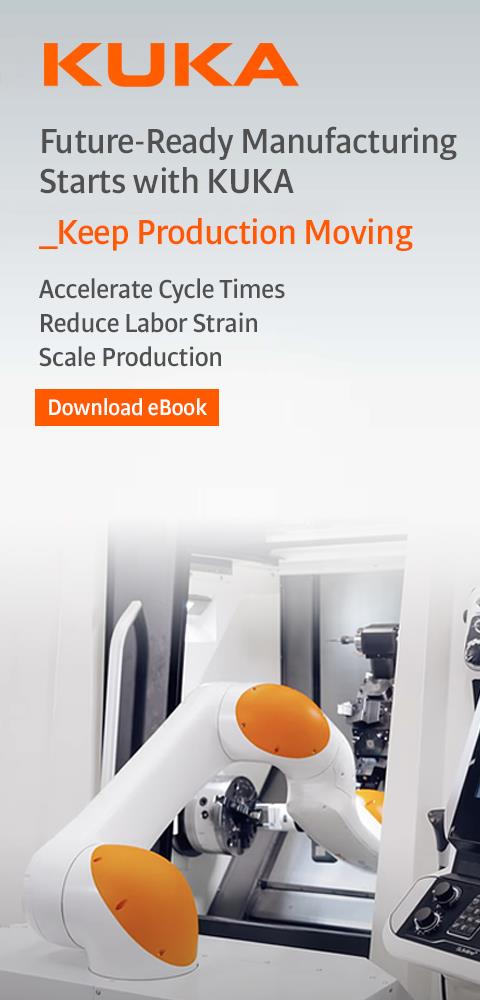
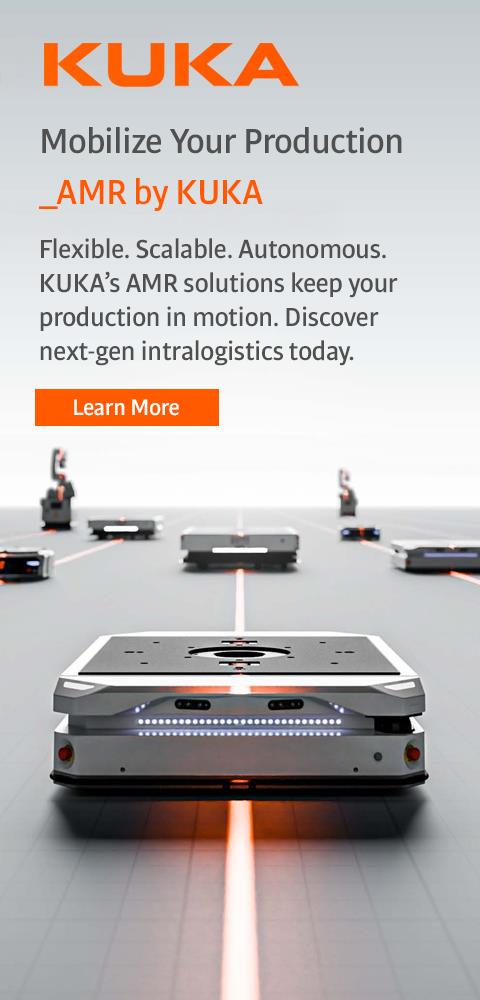
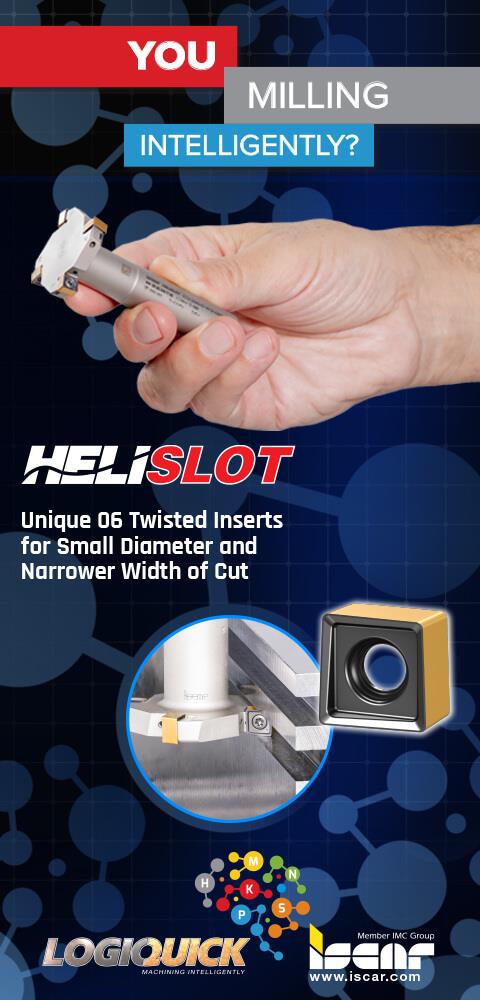
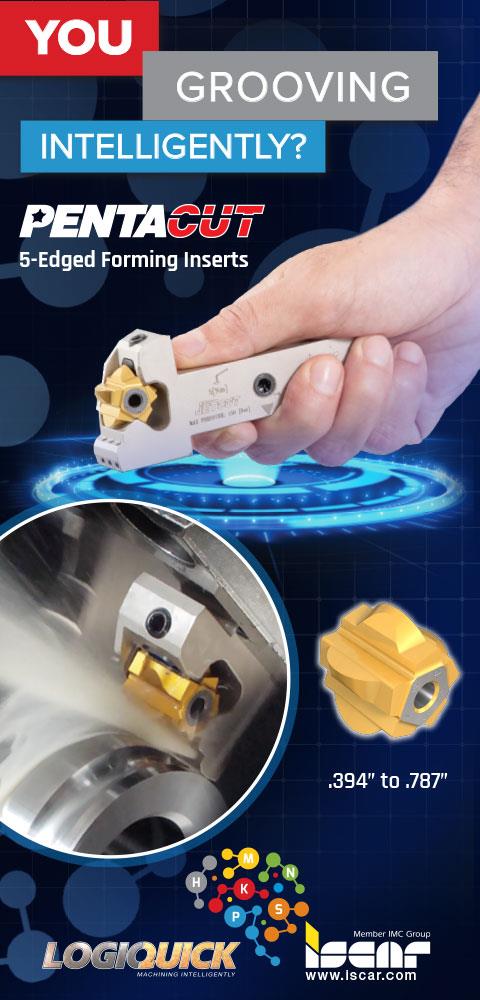
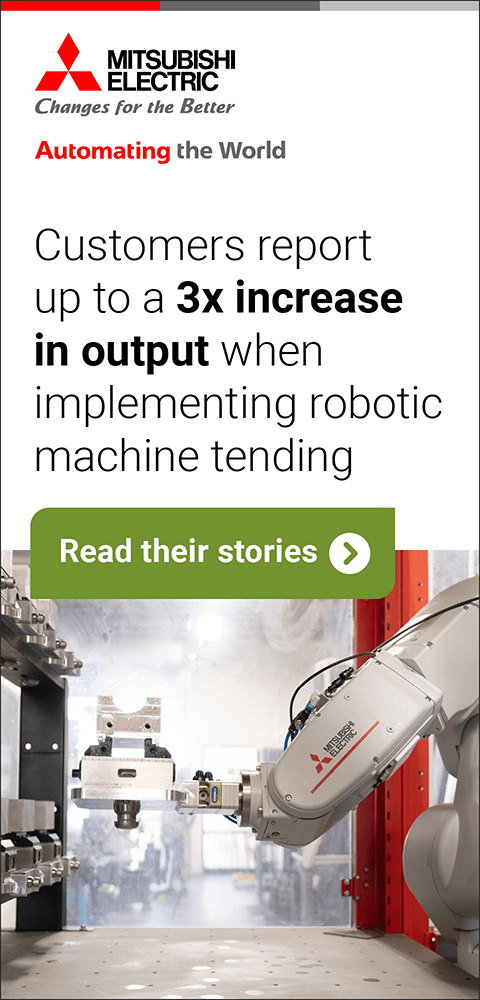
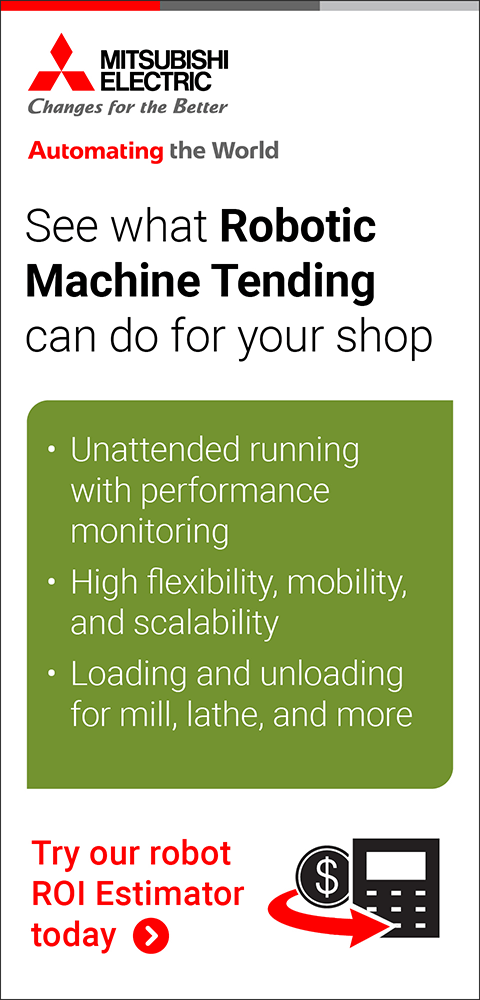
Grinding and Eroding Technology in One Machine
November 1, 2020
UNITED GRINDING Group has further extended its Two-in-One machine concept with the WALTER HELITRONIC RAPTOR DIAMOND. It offers enhanced flexibility when resharpening carbide or PCD tools for use with wood or metalcutting applications.
"WALTER eroding technology achieves low cycle times and better performance due to FINE PULSE TECHNOLOGY, which produces tools with smoother, more perfect exteriors and cutting edges along with super-fine finishes that match the level of visible shine generally reserved for polished tools," said a company spokesperson. "FINE PULSE TECHNOLOGY finely finishes tools made from the most common PCD types, from 10 µm grain size to coarse-grained formulations."
Developed especially for the re-sharpening and production of rotationally symmetrical PCD tools, the WALTER HELITRONIC RAPTOR DIAMOND is particularly well-suited for shops that do not require features such as automatic tool support systems or automatic grinding wheel/electrode changers, but still need a high degree of flexibility in the working area for diverse types of tools. "This ensures that manufacturers have access to WALTER quality with exactly the features they need for part-production and re-sharpening success," said the spokesperson.
The HELITRONIC RAPTOR DIAMOND has a 15.4 HP (11.5 kW) spindle and a work envelope that can accommodate tools up to 15.7" (400 mm) in diameter and 10.6" (270 mm) in length, including end face operations. Like other WALTER Two-in-One EDM and grinding machines, an HSK interface for electrode/wheel grinding is standard. For enhanced tool grinding and eroding efficiency, from tool design to part production as well as re-sharpening, the machine uses WALTER HELITRONIC TOOL STUDIO.
In addition to its low-vibration gray cast iron frame and gantry-type construction, the HELITRONIC RAPTOR DIAMOND is designed to accommodate a range of options, including top loaders with up to 500-tool capacities integrated in the working area. Other options include glass scales, A-axis torque drive, a grinding wheel measuring probe and a manual support steady rest.
For more information contact:
UNITED GRINDING North America Inc.
2100 UNITED GRINDING Blvd.
Miamisburg, OH 45342
937-859-1975
info@grinding.com
www.grinding.com
< back