
New touchscreen CNC control panel for large capacity rubber roller machine
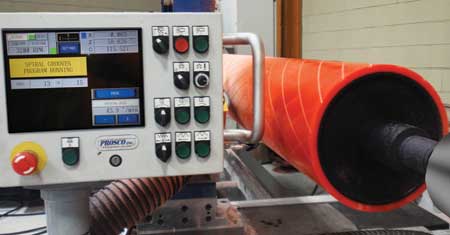
Groove pattern being applied to roller using new machine
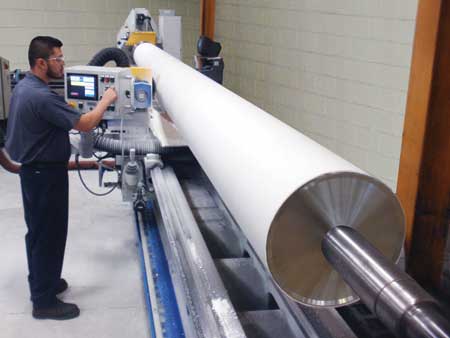
O.D. modification underway on silicone covered roller
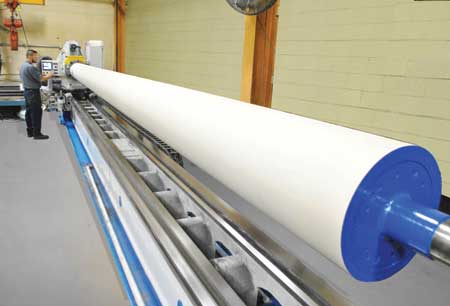
28' long rubber covered roller on new machine
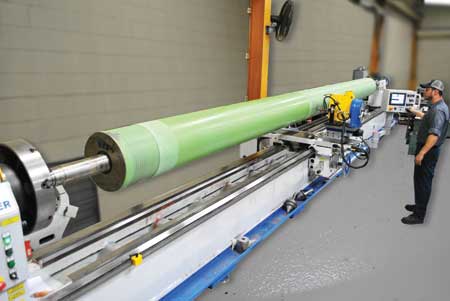
Large roller on new machine preparing for new cover
Menges Roller, a designer and manufacturer of industrial rollers for the plastic and paper converting industries, has extended the size capacity and technical capabilities of its Rubber Division with the purchase of a new machine.
The new state-of-the-art machine gives Menges an ability to handle rollers up to 10 meters (approx. 33'). The machine utilizes the latest computer interface and CNC technology to form precision groove patterns into rollcovers made from rubber, silicone, urethane and other synthetic compounds. Precise outside diameter modifications can also be made with this machine, including the formation of parabolic crowns and reverse crowns, in increments as small as a thousandth of an inch.
For rubber covered rollers, proper diameter specifications and surface finishes are critical - potentially having a big impact on a converting operation's output and quality.
Matthew Menges, President of Menges Roller explained the investment, "We are serving converters with wider and wider web widths - that is the nature of today's converting business - and this 10 meter capacity allows us to serve those customers. Plus, this machine's technology delivers accuracy and repeatability. Converting plants need precision engineered rollers that perform at a very high level, and that is what Menges Roller will continue to offer."
This capacity expansion is part of Menges Roller's Rubber Division, which offers dozens of rollcover compounds, from high-release silicones for corona treaters to abrasion-resistant urethanes and standard rollcover compounds such as EPDM, hypalon and nitrile. Many rollcover compounds are custom-formulated by Menges Engineers to meet specific hardness, slip and temperature profiles.
Menges's new machine will be relied upon to form precise groove patterns, such as diamond patterns (often applied to rollers with air pocket release functions), chevron and herringbone grooves (for push/pull rolls) and spiral serrations (for wrinkle removing rollers). Precision grooves, serrations and crowns can improve a roller's material handling characteristics, enhancing the efficiency of the overall converting operation.
For more information contact:
Menges Roller Company
260 Industrial Dr.
Wauconda, IL 60084
847-487-8877
www.mengesroller.com