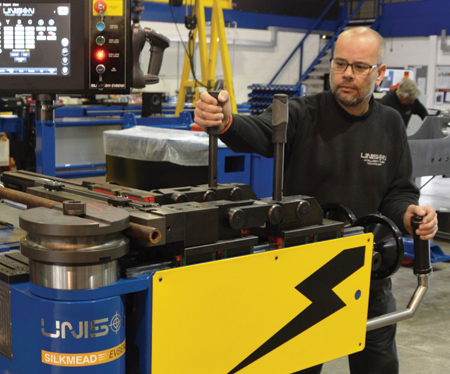
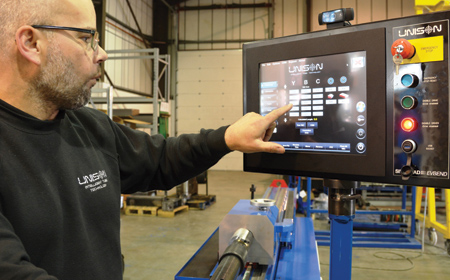
A new CNC-controlled tube bending machine from Unison with a semi-manual action is designed to lower the cost and skill level required to produce precision tubular parts in small volumes.
Unison has launched its tube bending machine designed to lower the cost and skill level required to produce precision tubular parts in small volumes. Target sectors for the new machine - which can bend tube diameters of up to 2" - include shipbuilding and equipment for oil, gas and other processing sectors.
"The new EvBend 2000 rotary-draw tube bending machine has a unique architecture combining manual set-up with semi-manual operation of the bending arm, which has servomotor power assistance," said a company spokesperson. "This approach makes the machine easy to understand and use, requiring just a few minutes of training, and inherently safe. Precise tube bending results are also assured by a CNC control system for the tube feed, carriage rotation and bend axes."
EvBend 2000 is a variant of Unison's EvBend 1000 manual machine which can handle tubing diameters up to 7/8" and is used in the aerospace sector. The new 2000 series machines can provide a bend torque of up to 4,056 ft-lbs. to assist operation of the bend arm. This design allows machines to handle larger tubing diameters up to 2", including tubing made from hard high-performance alloy materials.
"With EvBend 2000, operator safety continues to be assured by the requirement for human force on the bend arm to engage the power assistance, plus a form of 'dead man's switch,' which provides a fail-safe mechanism that instantly removes the power assistance if the operator lets go or relaxes the grip on the handle," said the spokesperson.
"The project to design a larger version of EvBend was started in response to user demand," said Brian Julien, CEO of Unison's North American sales and service partner ITEC. "The machine is amazingly easy to use. There is no need for a safety fence, mat or scanner. It is also cost effective. If a company has a demand for precision tubular parts in low volume, EvBend 2000 can provide a solution that has both a lower capital equipment cost and a reduced need for operator skill."
"EvBend machines reduce the entry costs to precision rotary draw tube bending by using manual operations to feed and rotate tubing and move the bending arm, but with smart CNC-controlled braking on the carriage feed, rotation and bend arm axes ensure part shapes are formed accurately," said the spokesperson. "Making prototypes or small quantities, and reverse engineering of part shapes, is easy using this process as the bending program can be broken down into simple steps and reviewed.
"There is almost no limit to the intricacy and multi-bend complexity of tubular shapes that can be formed, due to EvBend's ultra-compact bending head, and the versatility that manual/semi-manual operation brings to the manipulation process."
Users can create bending programs in two ways. First, operators may enter the standard tube bending information (XYZ/YBC/LRA values, or the distance tube is fed out, rotated and the angle of bend) into dialog screens on the EvBend's Windows operator interface; this data can also be transferred from a coordinate measuring machine. Alternatively, users can program the machine using a teaching mode. "This latter method is particularly powerful," said the spokesperson. "It is so simple to use that a part can be reverse-engineered by bending and comparing a tube against an existing part - with the user capturing the underlying material feed, rotation and angle of bend information as the desired points are reached."
Once the required bend data is entered, the user can start bending parts under the interactive guidance of the machine. EvBend's touchscreen Windows HMI displays the actions required in sequence with real-time feedback of positional data as tubing is fed, rotated or bent. "The precision and repeatability of these feed, rotation and bending operations is assured by a smart electromagnetic braking system," said the spokesperson. "Encoder feedback on each axis ensures that all movements are made with precision. EvBend machines may also be fitted with a pneumatic mandrel. The Windows HMI makes it easy to integrate EvBend into factory networks and access Unison's CAD tools and interfaces for the automated creation of tube bending programs."
EvBend machines can be configured with a right-hand or left-hand bending head. This orientation can also be changed by the user in approximately 15 minutes.
For more information contact:
Brian Julien
ITEC/Unison
Innovative Tube Equipment Corporation
1807 W. Sunnyside Ave.
Chicago, IL 60640
866-574-TUBE (8823)
info@tube-equipment.com
www.tube-equipment.com
www.unisonltd.com/products/bending-machines/evbend/