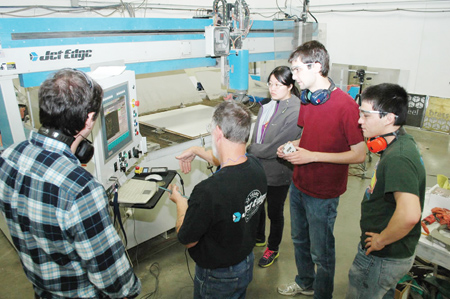
Jet Edge R&D Engineer Michael Wheeler (left) and Machinist Brian Wallace (center) discuss the waterjet cutting process with members of the University of Minnesota Solar Vehicle Project, Shiping Yi, Jacob Herbers and Chris Yamaguchi.
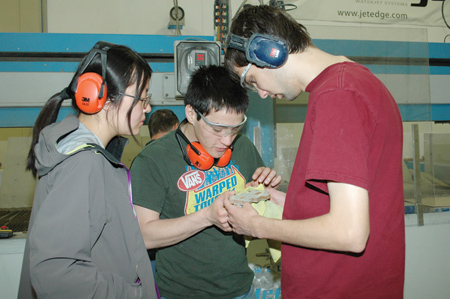
UMNSVP team members inspect a waterjet cut part. From left to right: Shiping Yi, Chris Yamaguchi, Jacob Herbers.
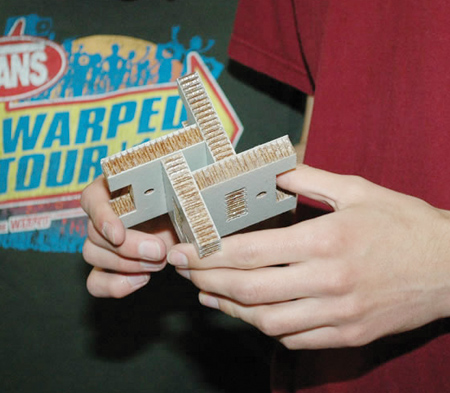
UMNSVP team members inspect a test cut piece for fit.
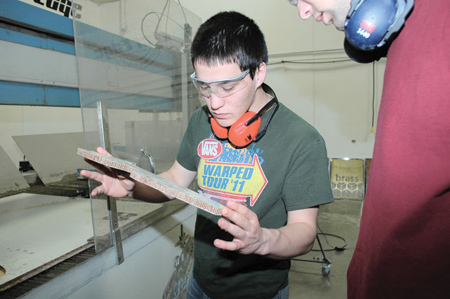
UMNSVP members Chris Yamaguchi (left) and Jacob Herbers inspect a chassis part.
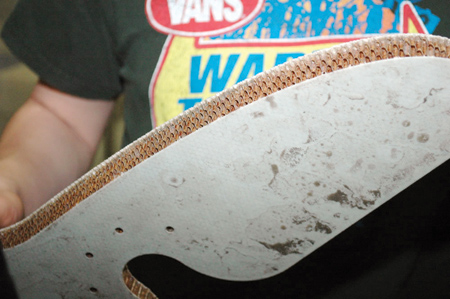
A side view of a finished part reveals the waterjet's precise cut and excellent edge quality.
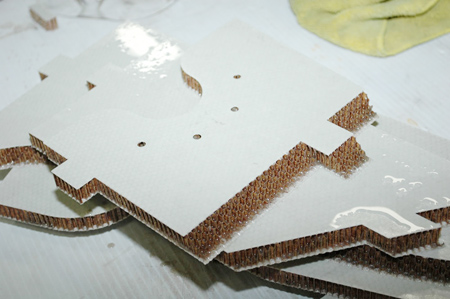
Many of the parts included beveled edges and small holes.
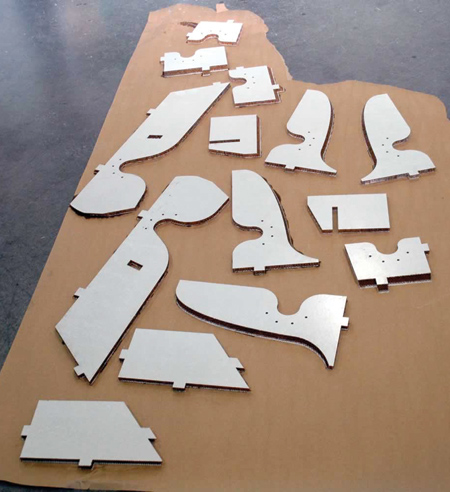
The team cut 14 finished parts at Jet Edge's waterjet test lab in St. Michael, MN.
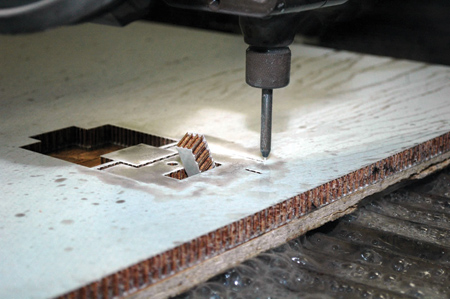
Waterjet systems manufacturer Jet Edge, Inc. recently helped the University of Minnesota Solar Vehicle Project (UMNSVP) by waterjetting several fiberglass composite chassis components for the team's new car, "Eos."
St. Michael-based Jet Edge is one of several Minnesota companies that has helped the student solar car team design and manufacture its two-person Cruiser Class car that competed in the three-day Formula Sun Grand Prix track race at Circuit of the Americas in Austin, TX, in July and will compete in the 3,000 km (1,877 mile) World Solar Challenge in Australia in October. The 40-member student-run team has been working on Eos for a year and a half.
Eos is the UMNSVP's 12th car since the project's inception in 1990. The project has raced numerous times in both the American Solar Challenge and the World Solar Challenge. Over the years, the project's teams have placed either first or second 15 times and have traveled to Canada, Australia, Japan and Taiwan. The project has given students invaluable real world experience since they are responsible for designing, funding, building, testing and racing each vehicle. "It also has helped advance solar technology by serving as an innovation test bed, and has helped advance electric motor technologies, paving the way for today's successful electric car companies," said a spokesperson.
The project has benefited from the tremendous support of Twin Cities businesses, noted Jacob Herbers, who recently completed his undergraduate degree in mechanical engineering.
"There are hundreds of different parts in the car, including the carbon composite outer shell, the carbon and fiberglass composite chassis panels, aluminum and steel mechanical components, solar cells, electric motors and controllers, lithium-ion batteries, electrical wiring, etc.," Herbers explained. "Our project would be impossible without the help of local manufacturers who have helped us with layups, laser cutting, tube bending, CNC milling and lathing, heat treating, soldering and waterjet cutting."
Herbers explained that the car's chassis components and other parts are cut from as light of material as possible to help the car achieve faster speeds. The team's previous car topped out at 80 miles per hour.
"The finished weight is estimated to be 500 lbs.," he said. "Every added pound of weight on the car would cause us to have to drive slower in the race."
Jet Edge's role in the project was to cut 14 parts from a 0.53" thick composite material that consisted of a layer of fiberglass on either side of 0.5" thick aramid honeycomb core. The waterjet manufacturer cut the parts in its St. Michael test lab, using its latest EDGE X-5 5-axis waterjet cutting system.
Prior to cutting the parts, Jet Edge's R&D engineer Michael Wheeler and Machinist Brian Wallace worked with the team to create DXF files from 3D files supplied by the team. They then used IGEMS waterjet CAD/CAM nesting software to produce the complicated bevels and to create the CNC programs. While the parts were already nested by the team, Wallace fine-tuned the nesting using IGEMS to save material.
"We cut the parts at 78,000 PSI using a 0.010/0.030 orifice/nozzle combination," said Wallace. "We used 0.4 pounds per minute of 80 grit garnet abrasive. We cut the holes at 10 inches per minute and the external shapes at 60 inches per minute. We adjusted the speed down appropriately for the bevels cuts. We only had one sheet of material to work with, so we utilized our nesting software to get the most parts out of that sheet. It took about 30 minutes to cut all 14 parts.
"This was first time I have cut a honeycombed composite material with the 5-axis. It worked perfectly. We probably could have cut the part without abrasive, but we did not have a lot of material to experiment with, so I decided to use abrasive. The material was not hard, but with the honeycomb and the bevels, you are cutting through open areas that interrupt the waterjet, and you are cutting through thicker and thinner material as it bevels."
To Herbers' knowledge, the team has always used waterjet to cut its composite components. "It is very precise and ensures a good fit when we assemble the chassis panels," he said.
Herbers encouraged other students to get involved in the Solar Vehicle Project. The UMNSVP is open to all University of Minnesota students, regardless of their area of study, he noted. Members can have as much or as little involvement as they want, but everyone works on designing and manufacturing a part of the car and more experienced members hold leadership positions.
"It is very interesting to visit with local manufacturers and see their processes," said Herbers, who is pursuing a career that will allow him to use his knowledge to save energy and protect the environment. "I have learned a lot about how to design parts for manufacturability, and have gotten to see firsthand how parts of different materials get made, which are things that mostly are not taught in school. These experiences will definitely help prepare me for a career in mechanical engineering."
For more information contact:
Jet Edge, Inc.
12070 43rd St. NE
St. Michael, MN 55376
800-JET-EDGE
sales@jetedge.com
www.jetedge.com
University of Minnesota
Solar Vehicle Project
612-460-7876
svp@umn.edu
www.umnsvp.org