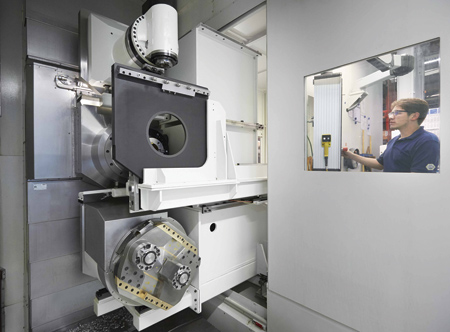
The facing head can be exchanged automatically and turns any machine from the redeveloped ECOFORCE series into a flexible, all-round solution for small and large components. In an ECOFORCE 1 HT2, the automatic pick-up magazine for the P700 facing head and the angled milling head are designed to simplify the entire machining workflow in a single clamping process.
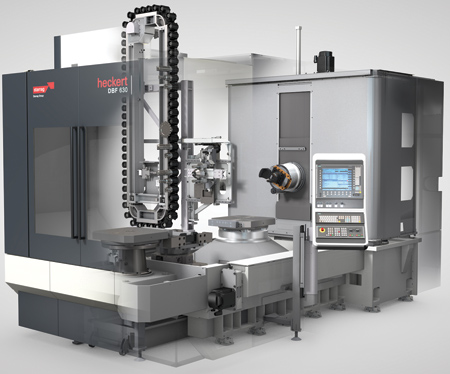
The interaction of the combined turning/drilling/milling head and radial facing slide designed as the NC axis in the Heckert DBF 630 HMC enables precise and cost-efficient machining of complex, asymmetrical workpieces in a single clamping.
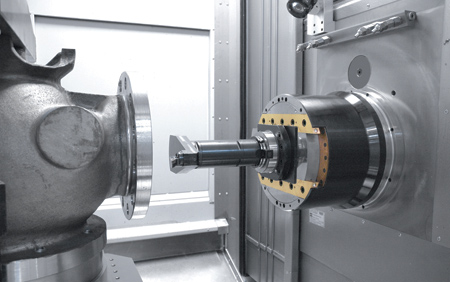
Internal and face turning work at the valve housing with the Heckert DBF 630 horizontal machining center
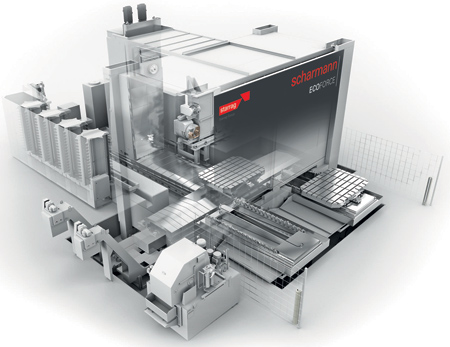
Scharmann ECOFORCE HMC
The Starrag Group offers with the product lines Scharmann ECOFORCE and Heckert DBF innovative machining solutions designed especially for valve and pump manufacturing.
The Heckert DBF horizontal machining centers (HMCs) with the integrated turning, drilling and milling head enable the turning, drilling and milling of non-rotation symmetrical parts in a single clamping using just one toolholder. The DBF machines feature accuracies of up to 0.00024" and 1,254 ft-lbs. of torque. These machining centers are particularly suited to complete machining of pump and valve housings, fittings, packing flanges, rock bits and chassis components.
A radial facing slide designed as the NC axis in the Heckert DBF HMCs is engineered to enable precise and cost-efficient machining of complex, asymmetrical workpieces in a single clamping. The variable speed 60 HP spindle drives milling or drilling tools at a maximum speed of 3,500 RPM in their center setting. The slide displaces the rotating turning tool radially by +/-1" when turning on the fixed workpiece. Compensation weights integrated into the machining head combined with balanced tools automatically compensate for any imbalances during the turning process and enable speeds of up to 1,200 RPM and cost-efficient cutting speeds of up to 9,843 IPM.
The DBF range can be purchased in a variety of sizes with pallet dimensions of 25" x 25" to 39" x 49". Working areas tailored to the size of the workpieces allow the DBF to adapt to each application.
The Scharmann ECOFORCE series shares many of the same features and equipment. The column in central design is one of the key features of the ECOFORCE machines, which includes an extensive range of core components developed and produced in-house. These components allow the series to be adapted to virtually any machining task, and include main spindles, gears and tables, as well as a variety of attachment heads that can be exchanged automatically. The facing head can also be exchanged automatically. It enables turning work to be carried out on the machine. This option turns a machine from the ECOFORCE series into a multi-functional, all-round solution that allows users to drill, cut and turn materials in a single clamping process.
The series can be used for full 5-sided or 5-axis machining in a table or pallet design with its spindle box and moveable quill (W-axis). It can machine workpieces weighing 22,046 to 88,185 lbs. in a continuous process. The four table sizes (49" x 63" to 98" x 118") or eight potential pallet sizes (39" x 39" to 79" x 98") enable a wide range of workpieces to be cut. There are three different main spindles available (with a power of 60, 72 or 86 HP) for machining different types of material. These main spindles can be operated in S1 continuous duty at high nominal torque of 1,475 to 2,950 ft-lbs. (maximum speed 4,000 RPM).
For more information contact:
Starrag USA Inc.
North American Headquarters
Skyport Business Park
2379 Progress Drive
Hebron, KY 41048
859-534-5201
ussales@starrag.com
www.starrag.com