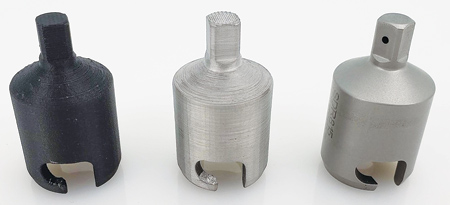
Helicopter sockets, which allow total screw construct removal, were first prototyped to allow orthopedic surgeons to test form and fit of the entire surgical tool.
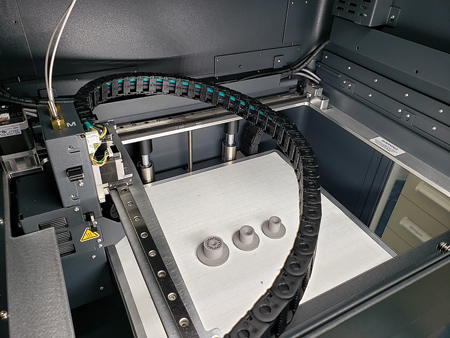
Shukla Medical prototyped the parts using 3D printed 17-4 PH stainless steel.
Markforged, a provider of metal and carbon fiber 3D printers, has announced that surgical tool manufacturer Shukla Medical-a subsidiary of aerospace manufacturer S.S. White Technologies-saved hundreds of thousands of dollars per year by utilizing a Markforged Metal X system to fabricate prototypes for its surgical instruments.
Known for their simple, intuitive designs, Shukla Medical's products are engineered for orthopedic surgeons and include time-saving features like quick-connections and multiple extraction options. The products need to be prototyped and tested by orthopedic implant surgeons before the final parts are manufactured, with surgeons checking for form and fit. Utilizing CNC machining, Shukla Medical often found that long lead times were presenting major slowdowns in iterating on prototypes and preventing them from quickly getting their product to market.
Shukla Medical engineers purchased a 3D printer from Markforged in 2017 and used it to create functional prototypes out of carbon fiber for surgeons to check for form and fit. "We put a lot of load on our instruments, and carbon fiber gives them more stiffness so it does not feel like a toy," said Adam Gosik-Wolfe, Mechanical Engineer at Shukla Medical.
The team was so impressed by the precision of its carbon fiber 3D printer that they decided to also invest in a Markforged Metal X system. Shukla chose the Metal X for its ease of use, wide range of materials and the safety it provided to its users.
Shukla Medical currently uses stainless steel when fabricating its end product, so the 17-4PH stainless steel material from Markforged proved to be the right option for prototyping. The team can conduct tests on the 3D printed metal prototype to verify and validate it, and surgeons can practice using it. "3D printing the prototype product helps our surgeons test the part in their hands before going into the operating room, so they already have the experience and confidence in the tool," said Zack Sweitzer, Product Development Manager at Shukla Medical. "The metal 3D printed prototypes have the look and feel of the final product, and are vastly different to the prototypes the surgeons are used to testing.
"The Metal X has let us print more complicated parts to conform to implant geometry that would have otherwise been very expensive to machine," said Gosik-Wolfe. "I think we are at the tip of the iceberg with what we will be able to make with the Metal X in the coming years."
With Markforged technology, Shukla is able to minimize time spent in the operating room, as well as increase safety and reduce recovery time for patients. "We are going to bring a lot more products to market faster with our Markforged printers, and we finally have the design freedom to do it," said Sweitzer.
For more information contact:
Markforged
480 Pleasant St.
Watertown, MA 02472
www.markforged.com